Cold pressing and regular pressing (often referred to as uniaxial pressing) are two distinct methods used in material compaction, each with unique advantages and applications. Cold pressing, specifically cold isostatic pressing (CIP), involves applying uniform pressure from all directions using a liquid or gaseous medium, which eliminates density gradients and allows for the compaction of complex shapes. Regular pressing, on the other hand, applies pressure in a single direction, which can lead to density gradients and limitations in shape complexity. The choice between these methods depends on the desired material properties, shape complexity, and application requirements.
Key Points Explained:
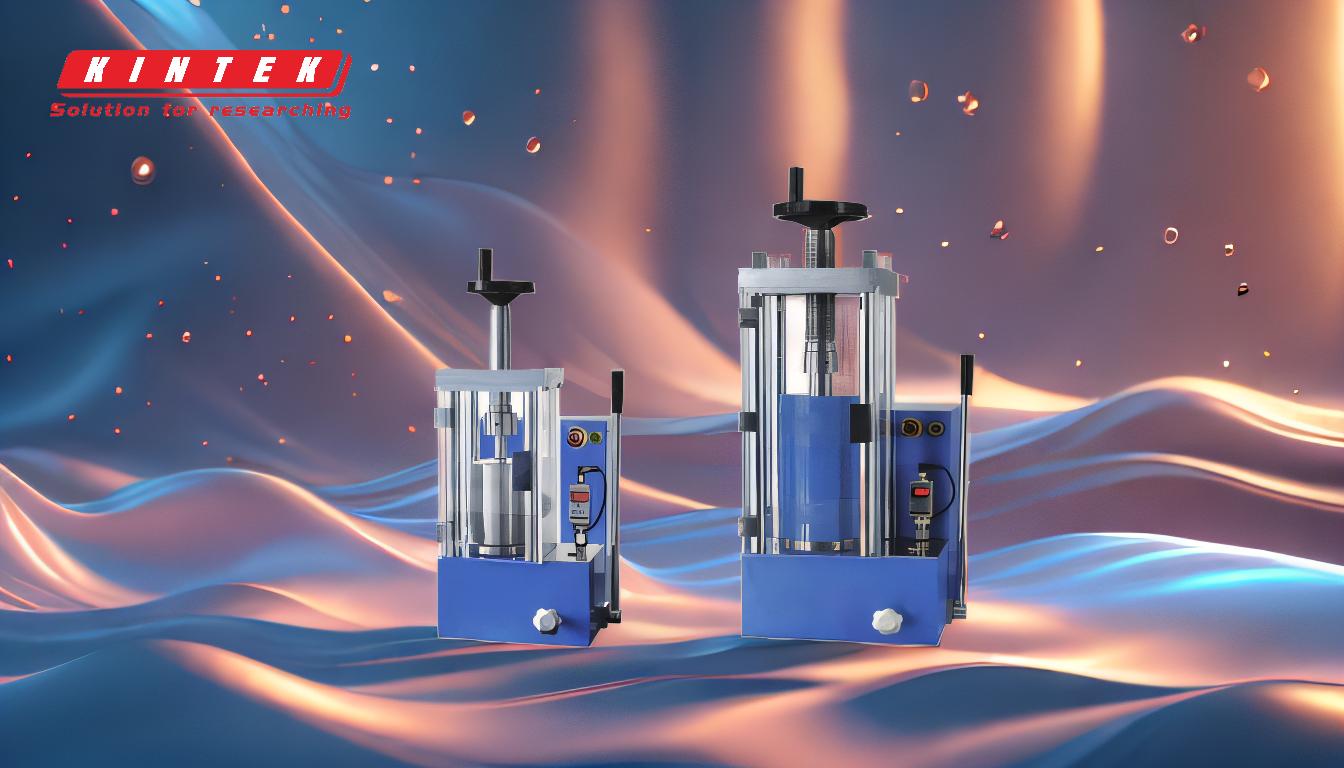
-
Uniformity of Pressure Application:
- Cold Isostatic Pressing (CIP): CIP applies pressure uniformly from all directions using a liquid or gaseous medium. This method ensures that the entire surface of the material is subjected to equal pressure, eliminating die-wall friction and resulting in more uniform densities. This is particularly beneficial for complex shapes and materials that require high density and uniformity.
- Regular Pressing (Uniaxial Pressing): Regular pressing applies pressure in a single direction, typically through mechanical means. This can lead to density gradients within the material, as the pressure is not uniformly distributed. The resulting parts may have varying densities, which can affect their mechanical properties and performance.
-
Density and Shape Complexity:
- CIP: The uniform pressure application in CIP allows for higher pressed densities and the compaction of more complex shapes. This method is particularly useful for materials that require high density and intricate geometries, as it avoids the limitations imposed by die-wall friction and density gradients.
- Regular Pressing: Regular pressing is generally limited to simpler shapes due to the unidirectional pressure application. The resulting parts may have lower densities and less uniform properties, which can be a limitation for high-performance applications.
-
Temperature Considerations:
- CIP: CIP is conducted at ambient temperatures, making it suitable for materials that cannot withstand high temperatures. This method is ideal for green parts that need to be compacted without the risk of thermal degradation.
- Regular Pressing: Regular pressing can be conducted at various temperatures, including elevated temperatures for certain applications. However, the temperature range is typically limited compared to hot isostatic pressing (HIP), which involves both high temperature and pressure.
-
Applications and Material Suitability:
- CIP: CIP is widely used for materials that require high density and uniformity, such as ceramics, metals, and composites. It is particularly beneficial for complex shapes and materials that are sensitive to temperature.
- Regular Pressing: Regular pressing is commonly used for simpler shapes and materials that do not require the high densities and uniformity provided by CIP. It is often used in the production of standard components and parts where cost and simplicity are prioritized over performance.
-
Equipment and Process Complexity:
- CIP: The equipment for CIP, such as the cold isostatic pressing machine, is more complex and typically more expensive than that used for regular pressing. The process also requires careful control of the pressure medium and conditions to ensure uniform compaction.
- Regular Pressing: Regular pressing equipment is generally simpler and less expensive, making it more accessible for a wide range of applications. The process is also more straightforward, with fewer variables to control compared to CIP.
In summary, the choice between cold pressing and regular pressing depends on the specific requirements of the material and application. CIP offers superior density and uniformity, making it ideal for complex shapes and high-performance materials, while regular pressing is more suitable for simpler shapes and cost-sensitive applications.
Summary Table:
Aspect | Cold Isostatic Pressing (CIP) | Regular Pressing (Uniaxial Pressing) |
---|---|---|
Pressure Uniformity | Uniform pressure from all directions, eliminating density gradients. | Pressure applied in a single direction, leading to density gradients. |
Density & Shape | Higher densities and ability to compact complex shapes. | Limited to simpler shapes with lower densities. |
Temperature | Conducted at ambient temperatures, ideal for temperature-sensitive materials. | Can be conducted at various temperatures, but limited compared to HIP. |
Applications | Suitable for ceramics, metals, and composites requiring high density and uniformity. | Used for simpler shapes and cost-sensitive applications. |
Equipment Complexity | More complex and expensive equipment, requiring precise control of pressure medium. | Simpler and less expensive equipment, easier to operate. |
Need help choosing the right pressing method for your materials? Contact our experts today for personalized advice!