Microwave sintering is a versatile and advanced material preparation technique used to produce a wide range of materials, including ceramics, metals, alloys, and specialized compounds. This method leverages microwave energy to achieve high-quality sintering, offering advantages such as high production efficiency, low unit cost, and the ability to produce materials with improved mechanical properties. The process is particularly effective for preparing sub-meter or even micron-level ceramic materials, making it suitable for applications in electronics, optics, and advanced material science. Microwave sintering is used to prepare materials such as optical fiber components, ferrites, superconducting materials, lithium hydride, nanomaterials, and various high-quality ceramics and electronic ceramic devices.
Key Points Explained:
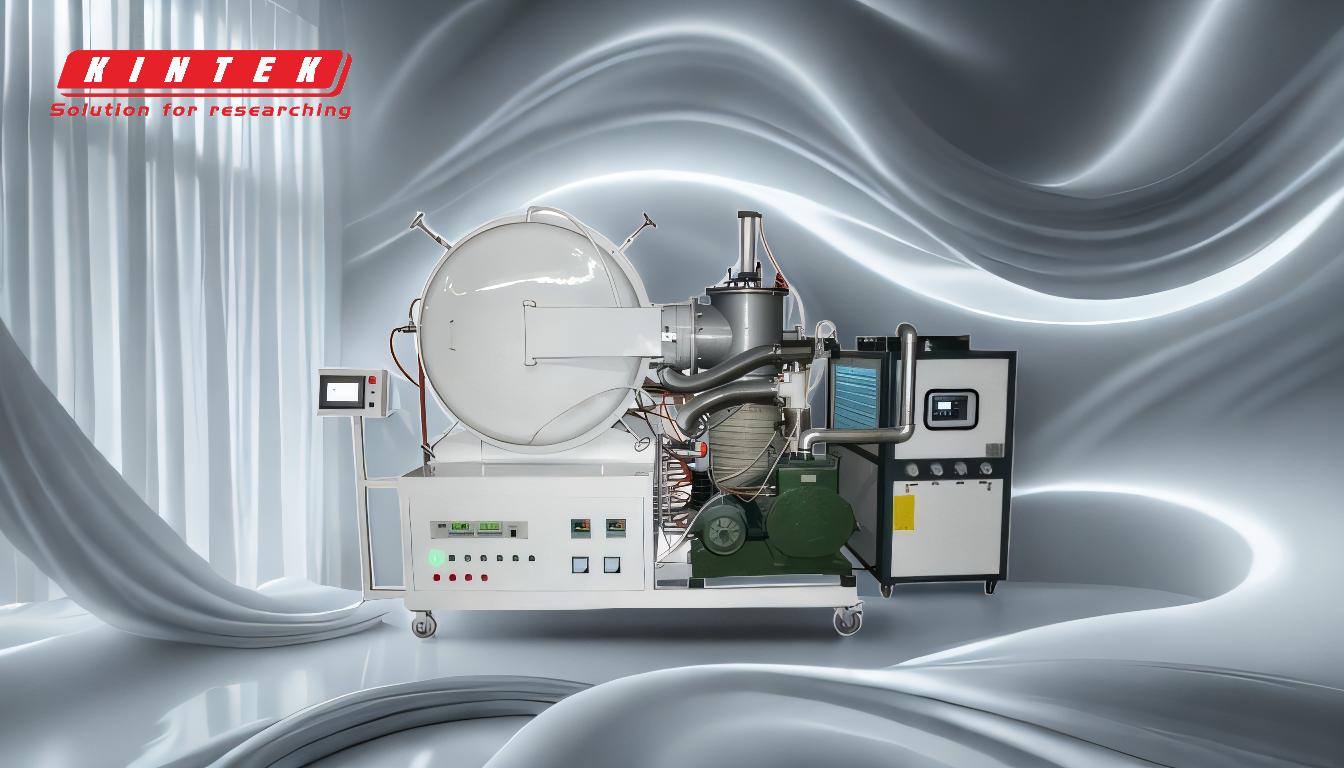
-
Categories of Materials Prepared by Microwave Sintering:
- Ceramics: Microwave sintering is widely used to produce high-quality ceramics, including silicon nitride, silicon carbide, aluminum oxide, aluminum nitride, zirconium oxide, and magnesium hydroxide. It is also used for electronic ceramic devices such as PZT piezoelectric ceramics and varistors.
- Metals and Alloys: Virtually all metals, alloys, and intermetallics in powdered form can be microwave sintered. This process produces highly sintered bodies with improved mechanical properties.
- Specialized Compounds: Microwave sintering is used to prepare materials such as lithium cobalt oxide, cobalt sulfate, cobalt oxalate, and vanadium oxide.
- Advanced Materials: The technology is also applied to produce optical fiber materials, ferrites, superconducting materials, lithium hydride, and nanomaterials.
-
Advantages of Microwave Sintering:
- High Production Efficiency: Microwave sintering offers faster heating rates and shorter processing times compared to conventional sintering methods.
- Low Unit Cost: The process does not require a traditional heat source, reducing energy consumption and overall costs.
- Improved Material Properties: Microwave sintering can produce materials with enhanced mechanical properties, such as higher density and improved microstructure.
- Precision and Control: The method is capable of producing sub-meter or even micron-level ceramic materials, making it suitable for advanced applications.
-
Microwave Sintering Process:
- Charging: The ceramic or metal powder is placed into the sintering furnace.
- Vacuuming: The furnace is evacuated to remove gases and impurities, ensuring a clean sintering environment.
- Microwave Heating: Microwave energy is used to heat the material to the required sintering temperature. This step is crucial for achieving the desired material properties.
- Insulation: The material is maintained at the sintering temperature for a specific period to allow chemical reactions and crystallization to occur.
- Cooling: The sintered material is gradually cooled to room temperature, completing the process.
-
Applications of Microwave Sintering:
- Electronics: Microwave sintering is used to produce electronic ceramic devices such as PZT piezoelectric ceramics and varistors, which are essential components in electronic circuits.
- Optics: The technology is applied in the preparation of optical fiber materials, which are critical for telecommunications and data transmission.
- Advanced Materials: Microwave sintering is used to produce superconducting materials, ferrites, and nanomaterials, which have applications in various high-tech industries.
-
Future Prospects:
- **Microwave sintering has broad application prospects in preparing advanced ceramic materials with sub-meter or even micron-level precision. Its ability to produce high-quality materials efficiently and cost-effectively makes it a promising method for future material science developments.
In conclusion, microwave sintering is a highly effective method for preparing a wide range of materials, including ceramics, metals, alloys, and specialized compounds. Its advantages in terms of efficiency, cost, and material properties make it a valuable technique in various industries, particularly in electronics, optics, and advanced material science.
Summary Table:
Aspect | Details |
---|---|
Materials Prepared | Ceramics, metals, alloys, specialized compounds, advanced materials |
Key Advantages | High efficiency, low cost, improved mechanical properties, precision control |
Applications | Electronics, optics, advanced material science |
Process Steps | Charging, vacuuming, microwave heating, insulation, cooling |
Future Prospects | Sub-meter and micron-level precision for advanced ceramics |
Unlock the potential of microwave sintering for your materials—contact us today to learn more!