The choice of a crucible depends on several factors, including the type of metal being melted, operating temperature, chemical inertness, and specific operational requirements. Graphite crucibles, silicon carbide (SiC) crucibles, and those made from cast iron or steel are commonly used in industrial applications, while platinum, zirconium, and their alloys are preferred for scientific applications due to their high melting points and chemical stability. The shape of the crucible, such as 'A' shape or bilge shape, also plays a role in its performance. Ultimately, selecting the best crucible requires a detailed analysis of the specific furnace, alloy, and operational practices involved.
Key Points Explained:
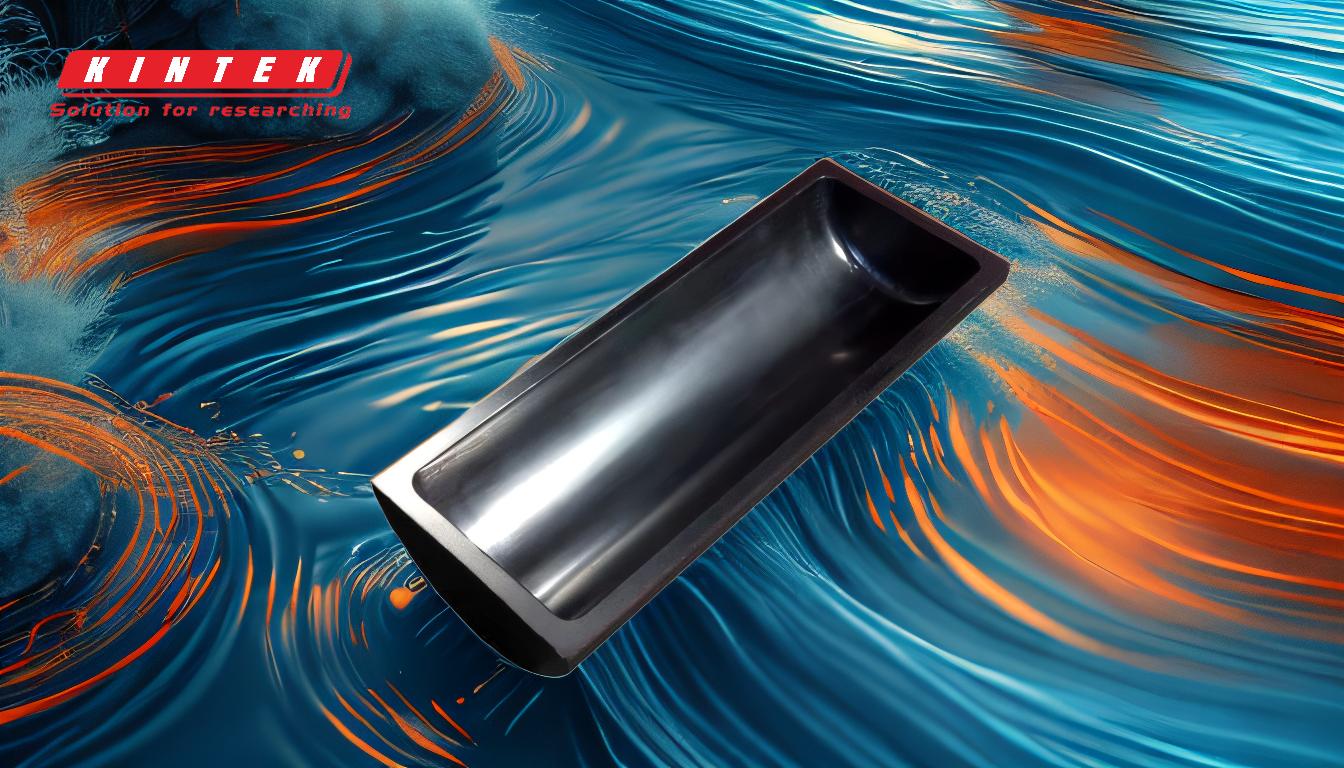
-
Material Selection:
- Graphite Crucibles: These are coated with a glazing layer and contain clay, making them suitable for general-purpose melting. They are cost-effective and widely used for non-ferrous metals like aluminum and copper.
- Silicon Carbide (SiC) Crucibles: Known for their high thermal conductivity and resistance to thermal shock, SiC crucibles are ideal for high-temperature applications and melting metals like iron and steel.
- Cast Iron/Steel Crucibles: These are typically used for melting magnesium and zinc alloys due to their durability and resistance to chemical reactions with these metals.
- Platinum and Platinum Alloys: These are used in scientific applications where chemical inertness and high melting points are critical. They prevent contamination of sensitive analytes and are essential for accurate analytical chemistry.
-
Operating Temperature:
- The crucible material must withstand the melting or holding temperature of the metal. For example, graphite and SiC crucibles are suitable for high-temperature applications, while cast iron or steel crucibles are better for lower-temperature metals like zinc and magnesium.
-
Chemical Inertness:
- In scientific applications, crucibles must not react with the analyte. Platinum and zirconium are preferred for their chemical stability, ensuring that the sample remains uncontaminated during analysis.
-
Shape and Design:
- 'A' Shape Crucibles: These have a slightly rough surface and coarse edges, but this does not affect their performance. They are often used in industrial settings where appearance is less critical.
- Bilge Shape Crucibles: These have a more polished and finished appearance, making them suitable for applications where aesthetics or ease of handling is important.
-
Operational Requirements:
- Factors such as furnace type, alloy composition, melting and holding temperatures, and specific processes like degassing or slag removal must be considered. For example, if cross-contamination is a concern, a crucible made of inert materials like platinum or zirconium should be used.
-
Application-Specific Considerations:
- Industrial Applications: The focus is on durability, thermal conductivity, and cost-effectiveness. Graphite and SiC crucibles are commonly used.
- Scientific Applications: The priority is chemical inertness and high-temperature stability, making platinum and zirconium crucibles the best choice.
By carefully evaluating these factors, you can select the crucible that best meets your specific needs, ensuring optimal performance and longevity.
Summary Table:
Factor | Description |
---|---|
Material Selection | Graphite, SiC, cast iron/steel for industrial use; platinum/zirconium for science. |
Operating Temperature | Choose materials that withstand the melting/holding temperature of the metal. |
Chemical Inertness | Essential for scientific applications to prevent contamination. |
Shape and Design | 'A' shape for industrial use; bilge shape for better aesthetics and handling. |
Operational Requirements | Consider furnace type, alloy, and processes like degassing or slag removal. |
Application-Specific | Industrial: durability and cost; scientific: chemical inertness and stability. |
Need help selecting the perfect crucible? Contact our experts today for tailored advice!