In the chemical vapor deposition (CVD) process for graphene synthesis, hydrogen gas (H₂) and inert gases such as argon (Ar) are commonly used as carrier gases. These gases play a critical role in enhancing surface reactions, improving reaction rates, and facilitating the deposition of graphene onto the substrate. Hydrogen is particularly important for its ability to act as a reducing agent and stabilize the carbon atoms during the graphene formation process. Inert gases like argon provide a stable environment, preventing unwanted chemical reactions and ensuring uniform deposition. The choice of carrier gas depends on the specific requirements of the graphene synthesis process, such as the desired quality, growth rate, and substrate compatibility.
Key Points Explained:
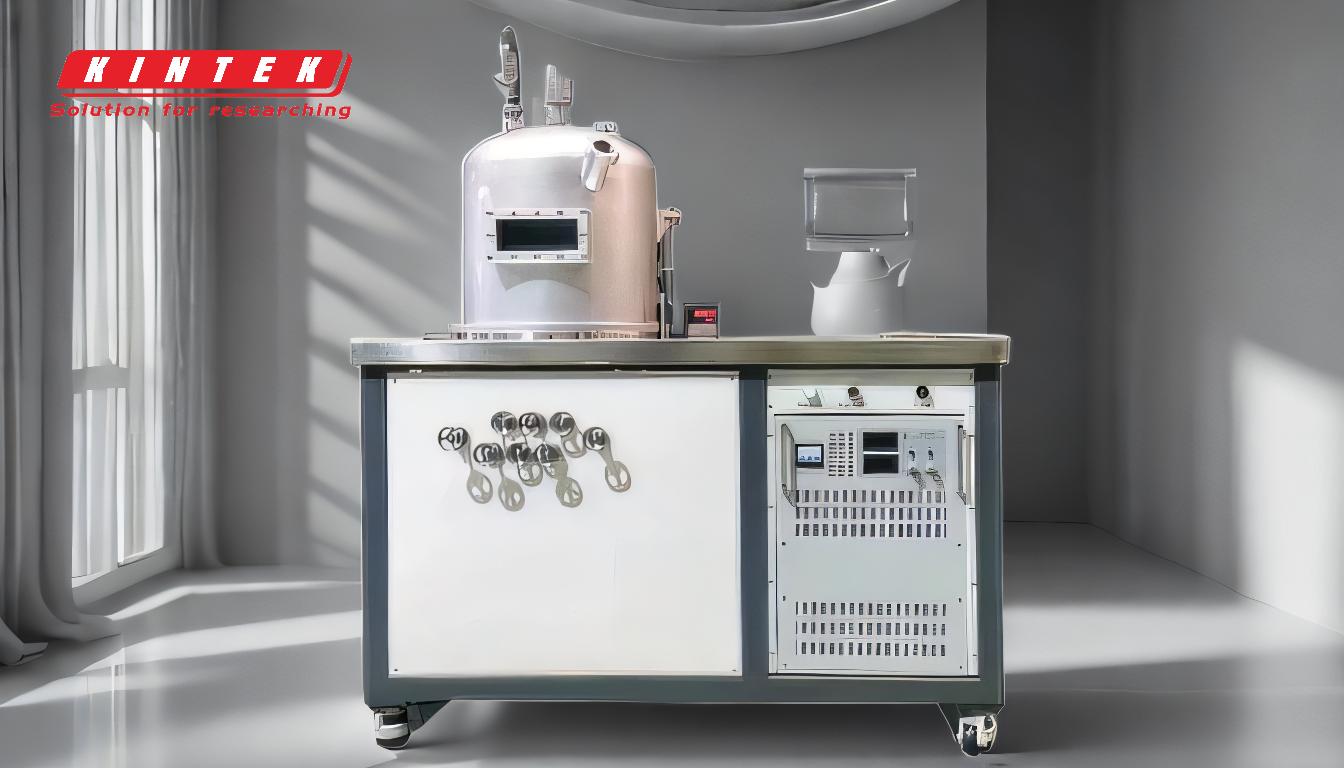
-
Primary Carrier Gases in CVD Graphene Synthesis:
-
Hydrogen (H₂):
- Acts as a reducing agent, removing oxygen and other impurities from the substrate surface.
- Stabilizes carbon atoms during the graphene formation process, promoting uniformity.
- Enhances surface reactions and improves the overall reaction rate.
-
Inert Gases (e.g., Argon, Ar):
- Provide a chemically inert environment, preventing unwanted side reactions.
- Ensure consistent and uniform deposition of graphene onto the substrate.
- Help maintain a stable pressure and temperature during the CVD process.
-
Hydrogen (H₂):
-
Role of Carrier Gases in Graphene Synthesis:
-
Surface Reaction Enhancement:
- Carrier gases facilitate the transport of carbon precursors to the substrate surface.
- Hydrogen aids in the dissociation of carbon-containing precursors, enabling the formation of graphene.
-
Improved Reaction Rates:
- The presence of hydrogen accelerates the decomposition of carbon sources, leading to faster graphene growth.
- Inert gases help maintain optimal conditions for the reaction to proceed efficiently.
-
Deposition Quality:
- Carrier gases ensure the even distribution of carbon atoms, resulting in high-quality graphene with fewer defects.
- Hydrogen helps control the nucleation density, affecting the thickness and uniformity of the graphene layer.
-
Surface Reaction Enhancement:
-
Factors Influencing Carrier Gas Selection:
-
Substrate Compatibility:
- The choice of carrier gas depends on the type of substrate used, as some materials may react differently with hydrogen or inert gases.
-
Process Requirements:
- For high-quality graphene, a precise balance of hydrogen and inert gases is necessary to optimize growth conditions.
-
Cost and Availability:
- Inert gases like argon are more expensive than hydrogen, which may influence the choice depending on the scale of production.
-
Substrate Compatibility:
-
Comparison with Other CVD Processes:
- While hydrogen and argon are commonly used in graphene synthesis, other CVD processes (e.g., diamond growth) may use different gas combinations, such as methane and hydrogen, depending on the desired material properties.
-
Practical Considerations for Equipment and Consumables:
-
Gas Delivery Systems:
- Precise control of gas flow rates is essential for consistent graphene growth.
- Mass flow controllers and modulating valves are critical components in CVD systems.
-
Safety Measures:
- Hydrogen is highly flammable, requiring proper handling and storage.
- Inert gases, while non-reactive, must be used in well-ventilated areas to prevent asphyxiation risks.
-
Gas Delivery Systems:
By understanding the roles and properties of these carrier gases, purchasers can make informed decisions about the equipment and consumables needed for efficient and high-quality graphene synthesis.
Summary Table:
Carrier Gas | Role in Graphene Synthesis | Key Benefits |
---|---|---|
Hydrogen (H₂) | Reducing agent, stabilizes carbon atoms | Enhances surface reactions, improves uniformity, accelerates growth |
Inert Gases (e.g., Argon) | Provides inert environment | Prevents unwanted reactions, ensures uniform deposition, maintains stable conditions |
Ready to optimize your graphene synthesis process? Contact our experts today for tailored solutions!