The "best" heating element depends on the specific application, as different materials and designs excel under varying conditions. Nickel-Chromium (NiCr) alloys are ideal for many applications due to their high resistance and efficient conversion of electrical energy into heat. However, factors such as required temperature, furnace atmosphere, material reactivity, and cost must also be considered. For example, ferrochromium-aluminum wires are suitable for temperatures up to 1200°C, while silicon carbide bars can handle up to 1400°C. The choice of heating element should align with the operational environment, including temperature uniformity, watt loading, and compatibility with the furnace atmosphere.
Key Points Explained:
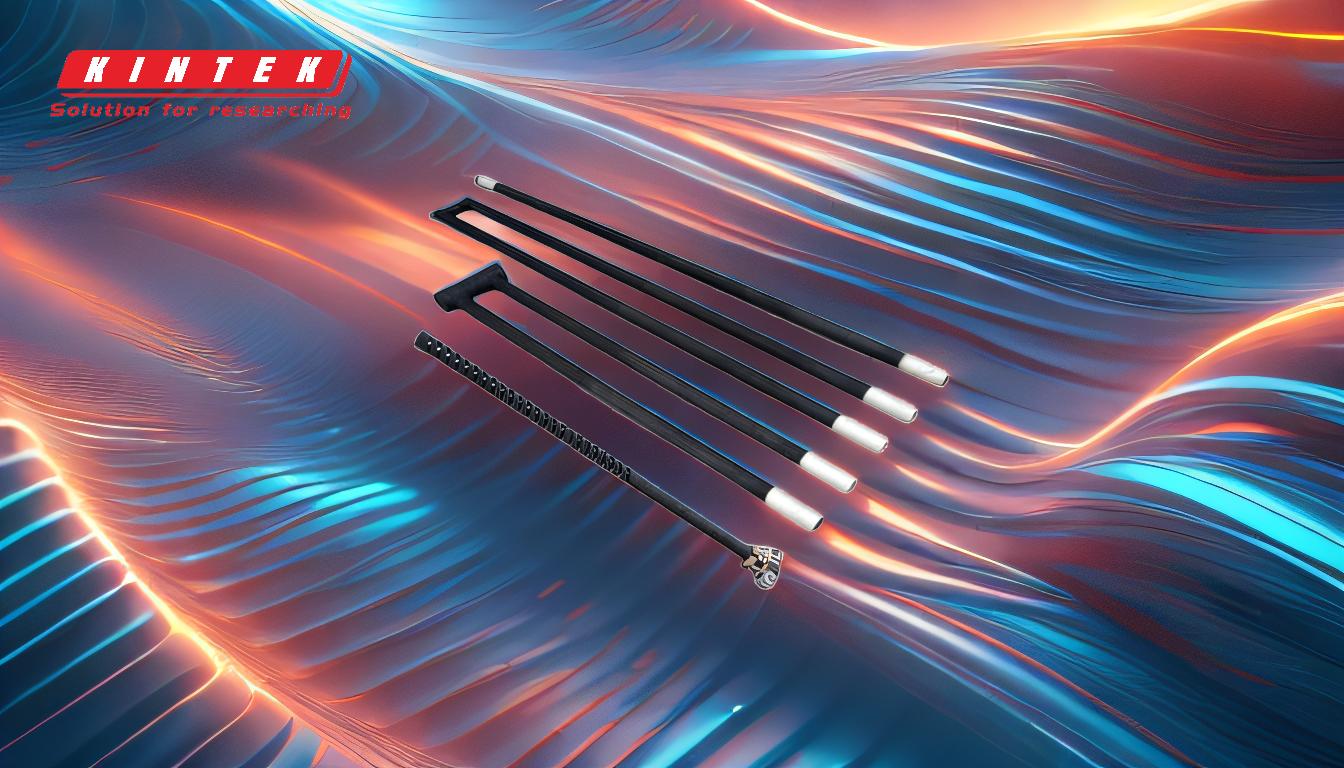
-
Material Suitability Based on Temperature Requirements:
- Nickel-Chromium (NiCr) Alloys: Ideal for general-purpose heating due to their high resistance and efficient heat conversion. They are widely used in applications requiring moderate temperatures.
- Ferrochromium-Aluminum Wires: Suitable for temperatures up to 1200°C, making them a good choice for medium-high temperature applications.
- Silicon Carbide Bars: Capable of withstanding temperatures up to 1400°C, making them suitable for high-temperature industrial furnaces.
-
Operational Environment and Atmosphere:
- The furnace atmosphere (e.g., endo gas, low-pressure carburizing) significantly influences the choice of heating element. Some materials perform better in specific atmospheres, while others may degrade or require protective measures.
- Reactivity to oxygen is another critical factor. Materials that can tolerate elevated temperatures in the presence of oxygen are preferred for certain applications, while others may need protective environments.
-
Heating Element Design and Performance:
- Tubular Electric Heaters: Commonly used for their durability and ability to provide uniform heating.
- Resistance Heating Elements: Efficient for converting electrical energy into heat, with designs tailored to specific watt loading and voltage requirements.
- Ceramic Heating Elements: Their properties, such as alloy composition and dimensions, must be carefully considered to ensure optimal performance.
-
Cost and Application-Specific Considerations:
- The cost of materials and their suitability for specific process applications play a significant role in selection. For example, NiCr alloys are cost-effective for many industrial applications, while silicon carbide may be reserved for specialized high-temperature processes.
- Temperature uniformity and the ability to heat workloads evenly are critical for achieving consistent results in heat treatment and other applications.
In summary, the "best" heating element is context-dependent, with NiCr alloys being a versatile and reliable choice for many scenarios. However, specific requirements such as temperature range, furnace atmosphere, and cost must guide the final decision.
Summary Table:
Material | Max Temperature | Key Features |
---|---|---|
Nickel-Chromium (NiCr) Alloys | Moderate Temperatures | High resistance, efficient heat conversion, cost-effective, general-purpose use |
Ferrochromium-Aluminum Wires | Up to 1200°C | Suitable for medium-high temperature applications |
Silicon Carbide Bars | Up to 1400°C | Ideal for high-temperature industrial furnaces |
Tubular Electric Heaters | Varies | Durable, provides uniform heating |
Ceramic Heating Elements | Varies | Alloy composition and dimensions tailored for optimal performance |
Need help choosing the right heating element for your furnace? Contact our experts today for personalized advice!