Sintering is a critical process in manufacturing, particularly for creating strong, durable components from powdered materials. The machines used for sintering vary depending on the material and the specific requirements of the process. Common sintering machines include sintering furnaces, which can operate under atmospheric pressure or vacuum conditions. These furnaces are designed to heat materials to high temperatures, often using protective gases like hydrogen, nitrogen, or carbon monoxide to prevent oxidation and ensure consistent results. The choice of machine depends on the material being sintered, such as metals (aluminum, brass, bronze, stainless steel) or ceramics, and the desired properties of the final product.
Key Points Explained:
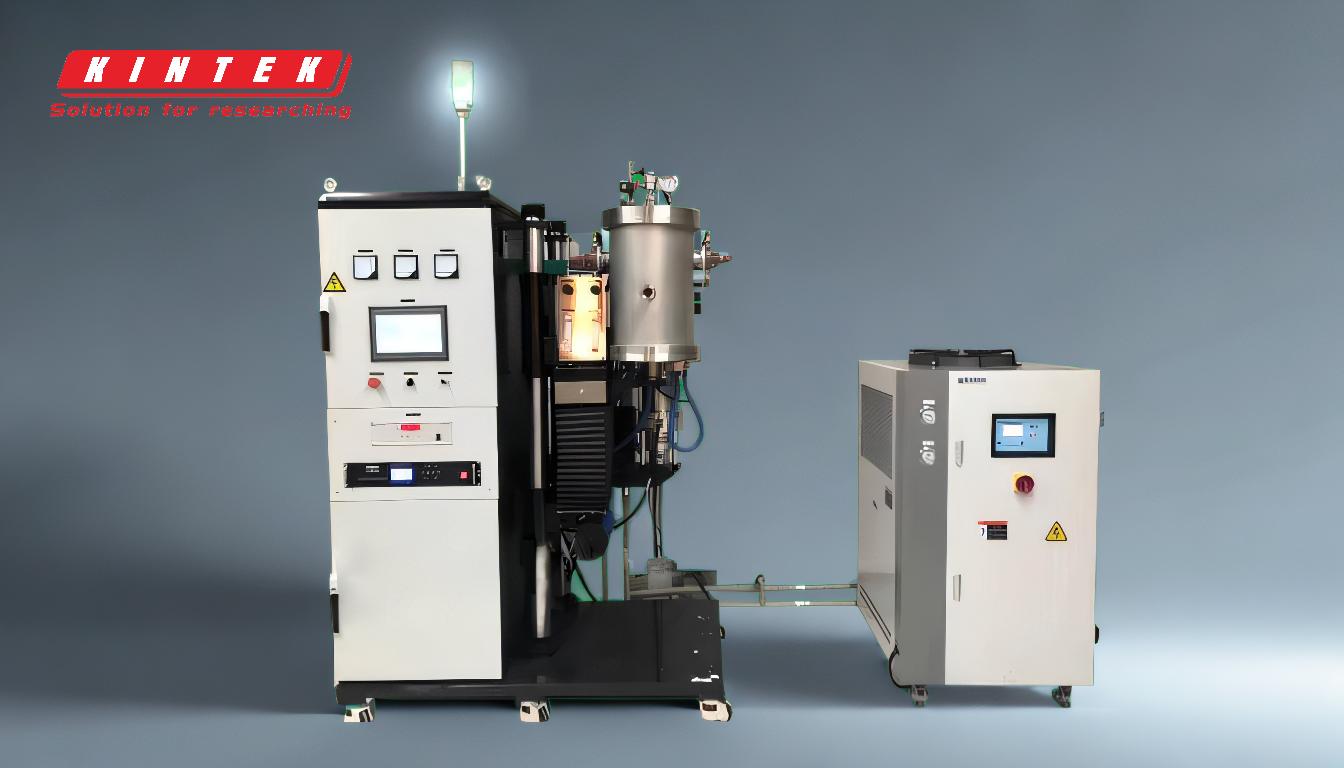
-
Types of Sintering Machines:
- Sintering Furnaces: These are the most common machines used for sintering. They are designed to heat materials to high temperatures, often in a controlled atmosphere to prevent oxidation. Furnaces can operate under atmospheric pressure or vacuum conditions, depending on the material and process requirements.
- Vacuum Sintering Furnaces: These are particularly useful for metals with very high melting points, such as tungsten and molybdenum. The vacuum environment prevents contamination and ensures a clean sintering process.
- Atmospheric Sintering Furnaces: These furnaces use protective gases like hydrogen, nitrogen, or carbon monoxide to create a controlled environment. This is essential for materials like stainless steel, aluminum, and other metals that require protection from oxidation.
-
Materials Used in Sintering:
- Metals: Common metals used in sintering include aluminum, brass, bronze, and stainless steel. These materials are chosen for their ability to form strong, durable components when sintered.
- Ceramics: Sintering is also used for ceramics, where the process helps to create dense, strong materials from powdered ceramic precursors.
- Plastics: Although less common, some plastics can also be sintered, particularly in additive manufacturing processes.
-
Protective Gases in Sintering:
- Hydrogen: Often used in sintering to reduce oxides and prevent oxidation. It is particularly effective for metals like stainless steel.
- Nitrogen: Provides an inert atmosphere, preventing oxidation and decarburization. It is commonly used in sintering operations for a variety of metals.
- Carbon Monoxide: Used in some sintering processes to create a reducing atmosphere, which helps in the densification of the material.
-
Advantages of Sintering:
- Control Over Manufacturing: Sintering allows for precise control over the manufacturing process, resulting in consistent and high-quality products.
- Complex Shapes: The process enables the creation of complex structural parts that would be difficult or impossible to produce using traditional manufacturing methods.
- Material Efficiency: Sintering uses powdered materials, which can be more efficient and result in less waste compared to traditional machining processes.
-
Applications of Sintering:
- Additive Manufacturing: Sintering is widely used in additive manufacturing (3D printing) to create metal and ceramic parts layer by layer.
- Automotive Industry: Sintered parts are commonly used in the automotive industry for components like gears, bearings, and other high-strength parts.
- Aerospace: The aerospace industry uses sintering to produce lightweight, high-strength components from materials like titanium alloys.
In summary, sintering machines, particularly sintering furnaces, are essential for creating high-quality, durable components from powdered materials. The choice of machine and process parameters depends on the material being sintered and the desired properties of the final product. Protective gases play a crucial role in ensuring the success of the sintering process, particularly for metals that are prone to oxidation.
Summary Table:
Aspect | Details |
---|---|
Types of Machines | Sintering Furnaces, Vacuum Sintering Furnaces, Atmospheric Sintering Furnaces |
Materials | Metals (aluminum, brass, bronze, stainless steel), Ceramics, Plastics |
Protective Gases | Hydrogen, Nitrogen, Carbon Monoxide |
Advantages | Precise control, complex shapes, material efficiency |
Applications | Additive manufacturing, automotive, aerospace |
Need the right sintering machine for your project? Contact us today for expert guidance!