When considering materials suitable for hardening, the choice depends on the specific application, desired properties, and the hardening process being used. Hardening typically involves increasing the hardness and strength of a material, often through heat treatment or mechanical processes. Metals like steel and certain alloys are commonly hardened due to their ability to undergo phase transformations that enhance mechanical properties. Other materials, such as ceramics and polymers, can also be hardened but through different mechanisms like sintering or cross-linking. Understanding the material's composition, structure, and the intended use is critical to selecting the right material for hardening.
Key Points Explained:
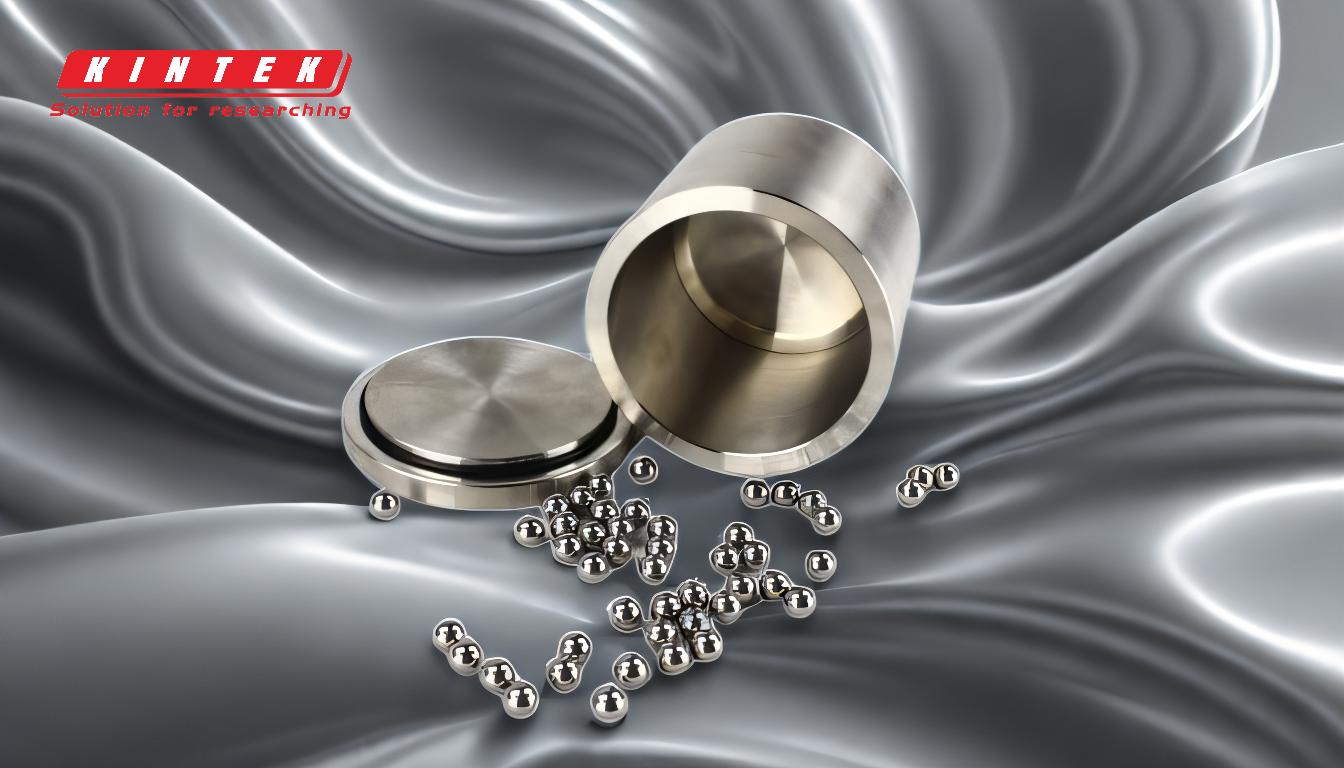
-
Steel and Its Alloys:
- Steel is the most common material for hardening due to its carbon content, which allows for heat treatment processes like quenching and tempering.
- Alloy steels, which include elements like chromium, nickel, and molybdenum, can achieve even higher hardness and wear resistance.
- Example: Tool steels are specifically designed for hardening and are used in cutting tools and dies.
-
Cast Iron:
- Certain types of cast iron, such as white cast iron, can be hardened to improve wear resistance.
- Hardening is typically achieved through heat treatment, but the process is more limited compared to steel due to the higher carbon content.
-
Non-Ferrous Metals:
- Aluminum alloys can be hardened through precipitation hardening or age hardening, which involves heat treatment to form fine precipitates that strengthen the material.
- Titanium alloys can also be hardened, often through heat treatment, to achieve high strength-to-weight ratios.
-
Ceramics:
- Ceramics can be hardened through processes like sintering, which increases density and strength.
- Advanced ceramics, such as silicon carbide or alumina, are often used in applications requiring extreme hardness and wear resistance.
-
Polymers:
- Polymers can be hardened through cross-linking, which increases their rigidity and strength.
- Example: Epoxy resins are often hardened through chemical reactions to create durable coatings or adhesives.
-
Factors Influencing Material Selection:
- The intended application (e.g., cutting tools, structural components) determines the required hardness and toughness.
- The hardening process must be compatible with the material’s properties to avoid issues like cracking or distortion.
- Cost and availability of the material also play a significant role in the selection process.
By carefully evaluating these factors, you can choose the most suitable material for hardening based on your specific needs.
Summary Table:
Material Type | Hardening Process | Key Applications |
---|---|---|
Steel & Alloys | Quenching, tempering, heat treatment | Cutting tools, dies, machinery |
Cast Iron | Heat treatment | Wear-resistant components |
Aluminum Alloys | Precipitation hardening | Aerospace, automotive parts |
Titanium Alloys | Heat treatment | High-strength, lightweight parts |
Ceramics | Sintering | Extreme hardness, wear resistance |
Polymers | Cross-linking | Coatings, adhesives |
Need help selecting the right material for hardening? Contact our experts today for personalized advice!