Sintering is a versatile manufacturing process used to create components from a wide range of materials, including metals, ceramics, polymers, and composites. The process involves compacting and heating powdered materials below their melting points to form solid structures with enhanced properties. Commonly used materials include iron and carbon steels, stainless steel, aluminum, nickel, copper, titanium alloys, molybdenum, tungsten, and ceramics. These materials are chosen based on their specific properties and the desired application, such as high-temperature resistance, strength, or durability. Sintering is particularly beneficial for materials with high melting points and is widely used in powder metallurgy, additive manufacturing, and the production of components like gears, bearings, and filters.
Key Points Explained:
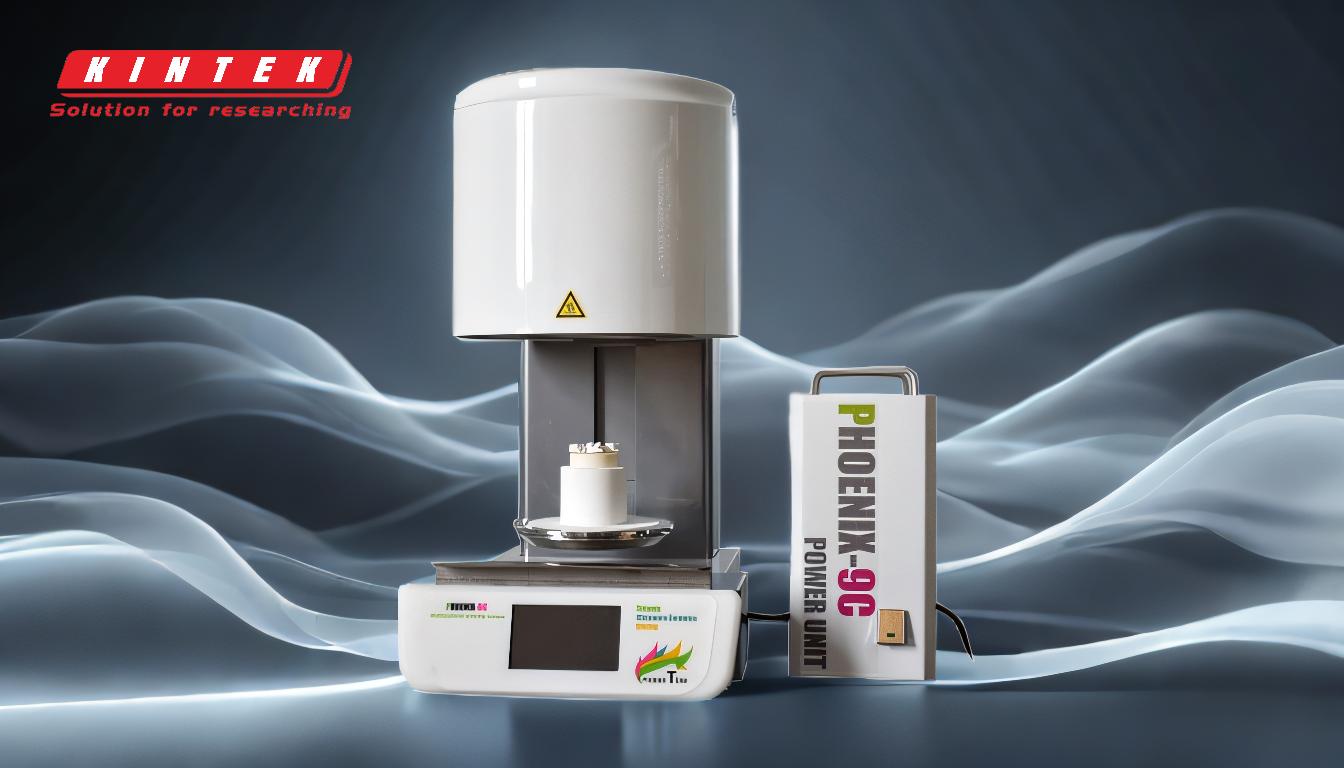
-
Materials Commonly Used in Sintering:
- Iron and Carbon Steels: Widely used in sintering due to their strength and affordability. They are often processed to enhance mechanical properties like hardness and wear resistance.
- Stainless Steel: Known for its corrosion resistance and durability, stainless steel is a popular choice for sintered components in industries like automotive and aerospace.
- Aluminum: Lightweight and corrosion-resistant, aluminum is used in sintering for applications requiring reduced weight and high thermal conductivity.
- Nickel and Copper Alloys: These materials are valued for their electrical conductivity, thermal resistance, and strength, making them suitable for electrical and high-temperature applications.
- Titanium Alloys: Used in sintering for their high strength-to-weight ratio and biocompatibility, often in medical and aerospace applications.
- Molybdenum and Tungsten: These high-melting-point metals are sintered for applications requiring extreme temperature resistance, such as in furnace components and aerospace parts.
- Ceramics: Sintered ceramics are used for their high-temperature stability, wear resistance, and electrical insulation properties, making them ideal for components like bearings and insulators.
- Polymers: Sintered polymers are used in rapid prototyping and filter manufacturing due to their versatility and ease of processing.
-
Applications of Sintered Materials:
- Powder Metallurgy: Sintering is a key process in powder metallurgy, where metal powders are compacted and sintered to produce small components like gears, pulleys, and bearings.
- Additive Manufacturing: Advanced sintering technologies, such as selective laser sintering (SLS), are used in 3D printing to create complex components from metal and polymer powders.
- High-Temperature Components: Materials like molybdenum, tungsten, and ceramics are sintered for use in high-temperature environments, such as furnace parts and aerospace components.
- Filters and Prototypes: Sintered polymers and metals are used to manufacture filters and prototypes, leveraging the process's ability to create porous and intricate structures.
-
Benefits of Sintering:
- Enhanced Material Properties: Sintering improves the mechanical, thermal, and electrical properties of materials, making them suitable for demanding applications.
- Cost-Effectiveness: The process allows for the production of complex shapes with minimal material waste, reducing costs.
- Versatility: Sintering can be applied to a wide range of materials, including metals, ceramics, and polymers, enabling the production of diverse components.
- Sustainability: Sintering often uses recycled materials and produces less waste compared to traditional manufacturing methods.
-
Technological Advancements in Sintering:
- Improved Sintering Techniques: Advances in sintering technologies, such as spark plasma sintering (SPS) and microwave sintering, have enhanced the efficiency and precision of the process.
- Additive Manufacturing Integration: Sintering is increasingly integrated with additive manufacturing techniques, enabling the production of complex, high-performance components.
- Material Refinement: Ongoing research and development have led to the refinement of sintered materials, improving their properties and expanding their applications.
By understanding the materials and processes involved in sintering, manufacturers can select the appropriate materials and techniques to meet specific application requirements, ensuring optimal performance and cost-effectiveness.
Summary Table:
Material | Key Properties | Common Applications |
---|---|---|
Iron & Carbon Steels | Strength, affordability, wear resistance | Gears, bearings, automotive parts |
Stainless Steel | Corrosion resistance, durability | Aerospace, medical devices |
Aluminum | Lightweight, thermal conductivity | Heat exchangers, lightweight components |
Nickel & Copper Alloys | Electrical conductivity, thermal resistance | Electrical components, high-temperature parts |
Titanium Alloys | High strength-to-weight ratio, biocompatibility | Medical implants, aerospace components |
Molybdenum & Tungsten | Extreme temperature resistance | Furnace parts, aerospace components |
Ceramics | High-temperature stability, wear resistance | Bearings, insulators |
Polymers | Versatility, ease of processing | Filters, rapid prototyping |
Need help selecting the right materials for your sintering process? Contact our experts today!