Depositing insulating thin films is a critical process in various industries, including semiconductors, optics, and electronics. The methods used for deposition can be broadly categorized into chemical and physical deposition techniques. Chemical methods, such as Chemical Vapor Deposition (CVD) and Atomic Layer Deposition (ALD), are widely used for their precision and ability to produce high-purity films. Physical methods, including sputtering and evaporation, are also commonly employed due to their versatility and ability to deposit a wide range of materials. The choice of method depends on factors such as the desired film properties, substrate material, and application requirements.
Key Points Explained:
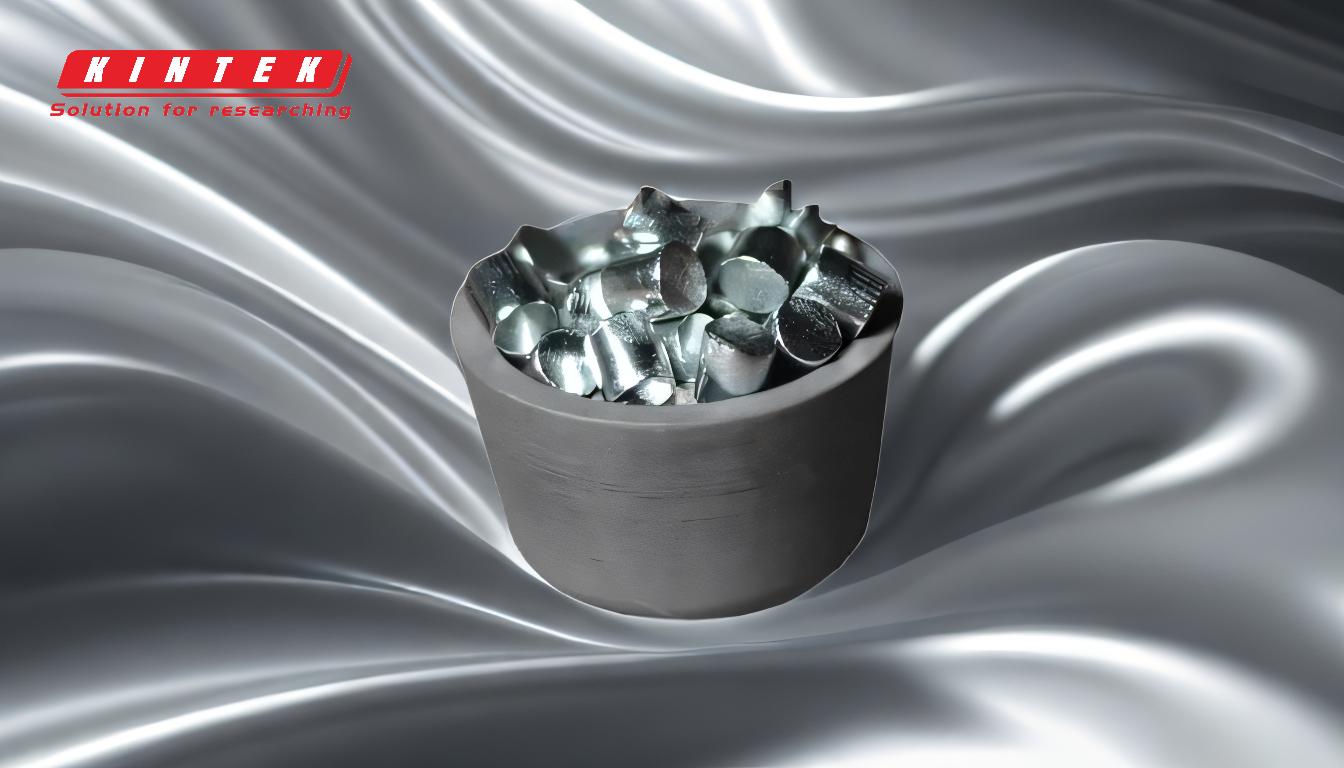
-
Chemical Vapor Deposition (CVD):
- Process: CVD involves the use of gaseous precursors that react on the substrate surface to form a thin film. The process typically occurs in a chamber where the substrate is exposed to the reactive gases.
- Advantages: CVD is known for its high precision and ability to produce uniform, high-purity films. It is particularly useful for depositing insulating materials like silicon dioxide (SiO₂) and silicon nitride (Si₃N₄).
- Applications: CVD is widely used in the semiconductor industry for creating insulating layers, as well as in the production of optical coatings and protective layers.
-
Plasma-Enhanced Chemical Vapor Deposition (PECVD):
- Process: PECVD is a variation of CVD that uses plasma to enhance the chemical reactions at lower temperatures. This makes it suitable for depositing films on temperature-sensitive substrates.
- Advantages: PECVD allows for deposition at lower temperatures compared to traditional CVD, which is beneficial for substrates that cannot withstand high temperatures.
- Applications: PECVD is commonly used for depositing insulating films in microelectronics and for creating passivation layers.
-
Atomic Layer Deposition (ALD):
- Process: ALD is a highly controlled deposition method where thin films are grown one atomic layer at a time. This is achieved by alternating the exposure of the substrate to different gaseous precursors.
- Advantages: ALD offers exceptional control over film thickness and uniformity, making it ideal for depositing ultra-thin insulating layers with precise thickness.
- Applications: ALD is used in advanced semiconductor manufacturing, particularly for creating high-k dielectric materials in transistors.
-
Physical Vapor Deposition (PVD):
- Process: PVD involves the physical transfer of material from a source to a substrate. Common PVD techniques include sputtering and evaporation.
- Advantages: PVD is versatile and can deposit a wide range of materials, including metals, ceramics, and insulators. It is also capable of producing high-purity films.
- Applications: PVD is used in various industries for depositing insulating films, such as in the production of optical coatings and protective layers.
-
Sputtering:
- Process: Sputtering involves bombarding a target material with high-energy ions, causing atoms to be ejected from the target and deposited onto the substrate.
- Advantages: Sputtering can produce high-quality films with excellent adhesion and uniformity. It is also suitable for depositing a wide range of materials, including insulators.
- Applications: Sputtering is widely used in the semiconductor industry for depositing insulating films, as well as in the production of thin-film solar cells and optical coatings.
-
Thermal Evaporation:
- Process: Thermal evaporation involves heating a material in a vacuum until it evaporates, and then condensing the vapor onto a substrate to form a thin film.
- Advantages: This method is simple and cost-effective, and it can produce high-purity films. However, it is less precise than other methods like CVD or ALD.
- Applications: Thermal evaporation is used for depositing insulating films in applications where high precision is not critical, such as in some optical coatings.
-
Electron Beam Evaporation:
- Process: Electron beam evaporation uses a focused electron beam to heat and evaporate the target material, which then deposits onto the substrate.
- Advantages: This method allows for the deposition of high-purity films and is particularly useful for materials with high melting points.
- Applications: Electron beam evaporation is used in the production of high-quality insulating films for optical and electronic applications.
-
Spin Coating:
- Process: Spin coating involves applying a liquid precursor onto a substrate and then spinning the substrate at high speed to spread the liquid into a thin, uniform layer. The liquid is then cured to form a solid film.
- Advantages: Spin coating is a simple and cost-effective method for depositing thin films, especially for organic and polymeric materials.
- Applications: Spin coating is commonly used in the production of insulating films for organic electronics, photovoltaics, and protective coatings.
In summary, the choice of deposition method for insulating thin films depends on the specific requirements of the application, including the desired film properties, substrate material, and process constraints. Chemical methods like CVD and ALD offer high precision and purity, while physical methods like sputtering and evaporation provide versatility and cost-effectiveness. Each method has its own advantages and is suited to different applications, making it essential to carefully select the appropriate technique based on the specific needs of the project.
Summary Table:
Method | Advantages | Applications |
---|---|---|
Chemical Vapor Deposition (CVD) | High precision, uniform, high-purity films | Semiconductor insulating layers, optical coatings, protective layers |
Plasma-Enhanced CVD (PECVD) | Lower temperature deposition, suitable for sensitive substrates | Microelectronics, passivation layers |
Atomic Layer Deposition (ALD) | Ultra-thin, precise thickness control | High-k dielectric materials in transistors |
Physical Vapor Deposition (PVD) | Versatile, deposits metals, ceramics, and insulators | Optical coatings, protective layers |
Sputtering | High-quality films, excellent adhesion, wide material range | Semiconductor films, thin-film solar cells, optical coatings |
Thermal Evaporation | Simple, cost-effective, high-purity films | Optical coatings (less precise applications) |
Electron Beam Evaporation | High-purity films, suitable for high melting point materials | High-quality insulating films for optical and electronic applications |
Spin Coating | Simple, cost-effective, ideal for organic and polymeric materials | Organic electronics, photovoltaics, protective coatings |
Need help selecting the right deposition method for your project? Contact our experts today for tailored solutions!