Brazing is a widely used joining process in various industries, but it comes with its own set of disadvantages. These drawbacks can impact the efficiency, cost, and quality of the final product. Some of the key disadvantages include reduced material hardness after high-temperature welding, high process requirements, technical difficulty, high energy consumption, long processing time, and high cleaning and environmental protection costs before welding. Additionally, furnace brazing has its own set of challenges, such as the necessity for close fits to facilitate capillary action, the annealing of component parts during the process, and the need to allow for the location of the brazing material in the design.
Key Points Explained:
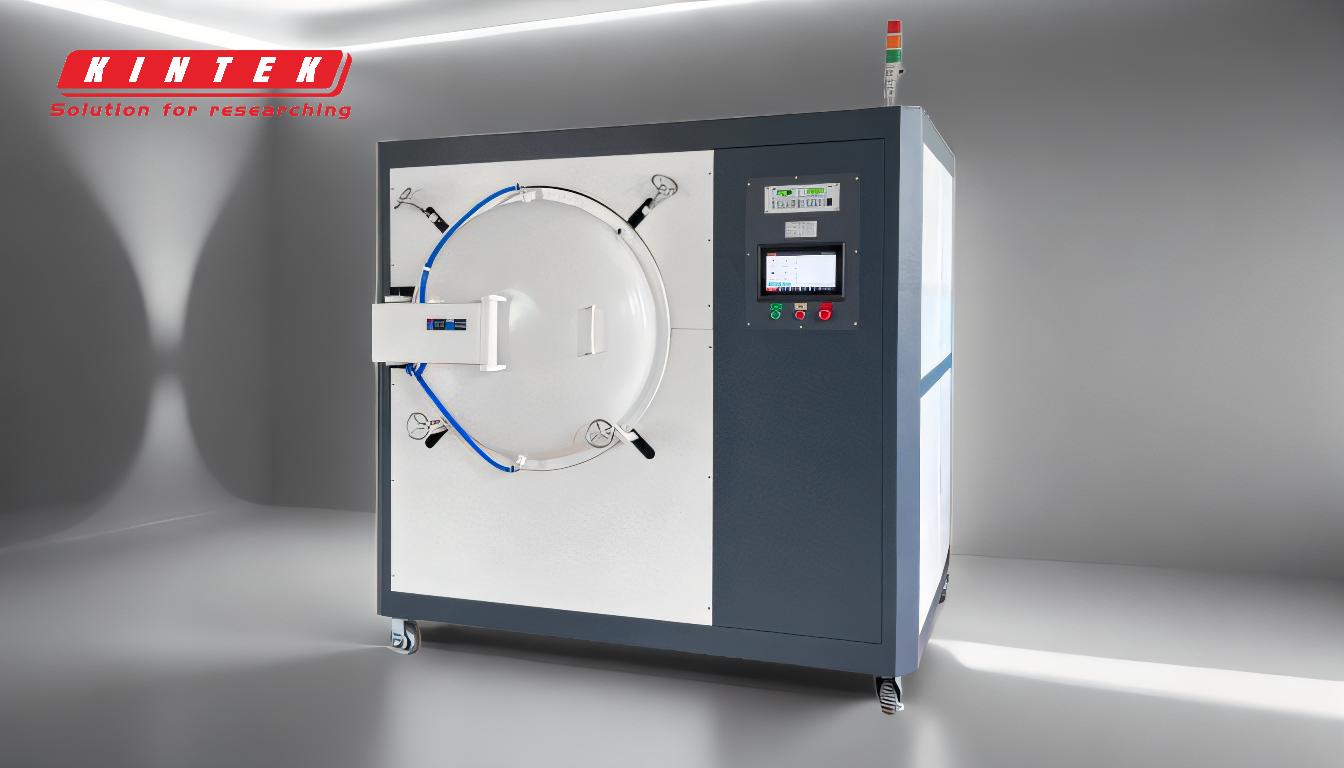
-
Reduced Material Hardness After High-Temperature Welding:
- One of the significant disadvantages of the brazing process, particularly vacuum brazing, is the reduction in material hardness after high-temperature welding. This occurs because the high temperatures used in brazing can alter the microstructure of the base materials, leading to a decrease in hardness. This can be particularly problematic for materials that rely on their hardness for performance, such as certain alloys used in aerospace or automotive applications.
-
High Process Requirements and Technical Difficulty:
- Brazing, especially vacuum brazing, demands high process requirements and technical expertise. The process involves precise control of temperature, atmosphere, and filler material placement. Any deviation from the optimal conditions can lead to defects such as incomplete joints or voids. This high level of precision requires skilled operators and sophisticated equipment, which can increase the overall cost and complexity of the process.
-
High Energy Consumption:
- The brazing process, particularly when performed in a vacuum or furnace, consumes a significant amount of energy. The need to maintain high temperatures for extended periods, along with the energy required to create and maintain a vacuum, contributes to high energy consumption. This not only increases operational costs but also has environmental implications due to the higher carbon footprint associated with energy-intensive processes.
-
Long Processing Time:
- Brazing often involves long processing times, especially when dealing with large or complex assemblies. The need to heat the components uniformly and maintain the temperature for a sufficient duration to ensure proper bonding can lead to extended cycle times. This can be a disadvantage in industries where rapid production cycles are critical, such as in mass manufacturing.
-
High Cleaning and Environmental Protection Costs Before Welding:
- Before brazing, components must be thoroughly cleaned to remove any contaminants that could interfere with the bonding process. This cleaning process can be costly and time-consuming, especially when dealing with intricate parts or materials that are prone to oxidation. Additionally, the disposal of cleaning agents and by-products must be managed in an environmentally responsible manner, adding to the overall cost and complexity of the process.
-
Necessity for Close Fits to Facilitate Capillary Action (Furnace Brazing):
- In furnace brazing, the components to be joined must have close fits to facilitate capillary action, which is essential for the proper flow and distribution of the brazing filler material. This requirement can limit the design flexibility and may necessitate additional machining or preparation of the components, increasing the overall cost and time of the process.
-
Annealing of Component Parts During the Process (Furnace Brazing):
- During furnace brazing, the component parts may undergo annealing, a process that softens the material by heating it to a specific temperature and then allowing it to cool slowly. While annealing can relieve internal stresses, it can also reduce the hardness and strength of the material, which may not be desirable for certain applications.
-
Need to Allow for the Location of the Brazing Material in the Design (Furnace Brazing):
- The design of components for furnace brazing must take into account the placement of the brazing material. This can limit design options and may require additional considerations during the design phase to ensure that the brazing material is properly located and that the joint will be strong and reliable.
In summary, while brazing offers several advantages, such as the ability to join complex assemblies and produce high-quality joints, it also comes with significant disadvantages. These include reduced material hardness, high process requirements, technical difficulty, high energy consumption, long processing times, and high cleaning and environmental protection costs. Additionally, furnace brazing has its own set of challenges, such as the need for close fits, annealing of components, and design considerations for brazing material placement. Understanding these disadvantages is crucial for making informed decisions about whether brazing is the appropriate joining method for a given application.
Summary Table:
Disadvantage | Description |
---|---|
Reduced Material Hardness | High temperatures can decrease material hardness, affecting performance. |
High Process Requirements | Requires precise control of temperature, atmosphere, and filler placement. |
High Energy Consumption | Significant energy use, especially in vacuum or furnace brazing. |
Long Processing Time | Extended heating and bonding times, slowing production cycles. |
High Cleaning Costs | Thorough cleaning before welding increases costs and time. |
Close Fits for Capillary Action | Limits design flexibility and increases preparation costs. |
Annealing of Components | May reduce hardness and strength of materials during the process. |
Design Considerations for Brazing Material | Requires careful placement of brazing material, limiting design options. |
Need help deciding if brazing is right for your application? Contact our experts today for tailored advice!