Thin films are essential in various industries, including electronics, optics, and energy, due to their unique properties and applications. They are created using a variety of deposition methods, which can be broadly categorized into chemical and physical methods. Chemical methods involve processes like electroplating, sol-gel, dip coating, spin coating, chemical vapor deposition (CVD), plasma-enhanced CVD (PECVD), and atomic layer deposition (ALD). Physical methods include sputtering, thermal evaporation, carbon coating, electron beam evaporation, molecular beam epitaxy (MBE), and pulsed laser deposition (PLD). These methods allow for precise control over the thickness and properties of the thin films, making them suitable for a wide range of applications.
Key Points Explained:
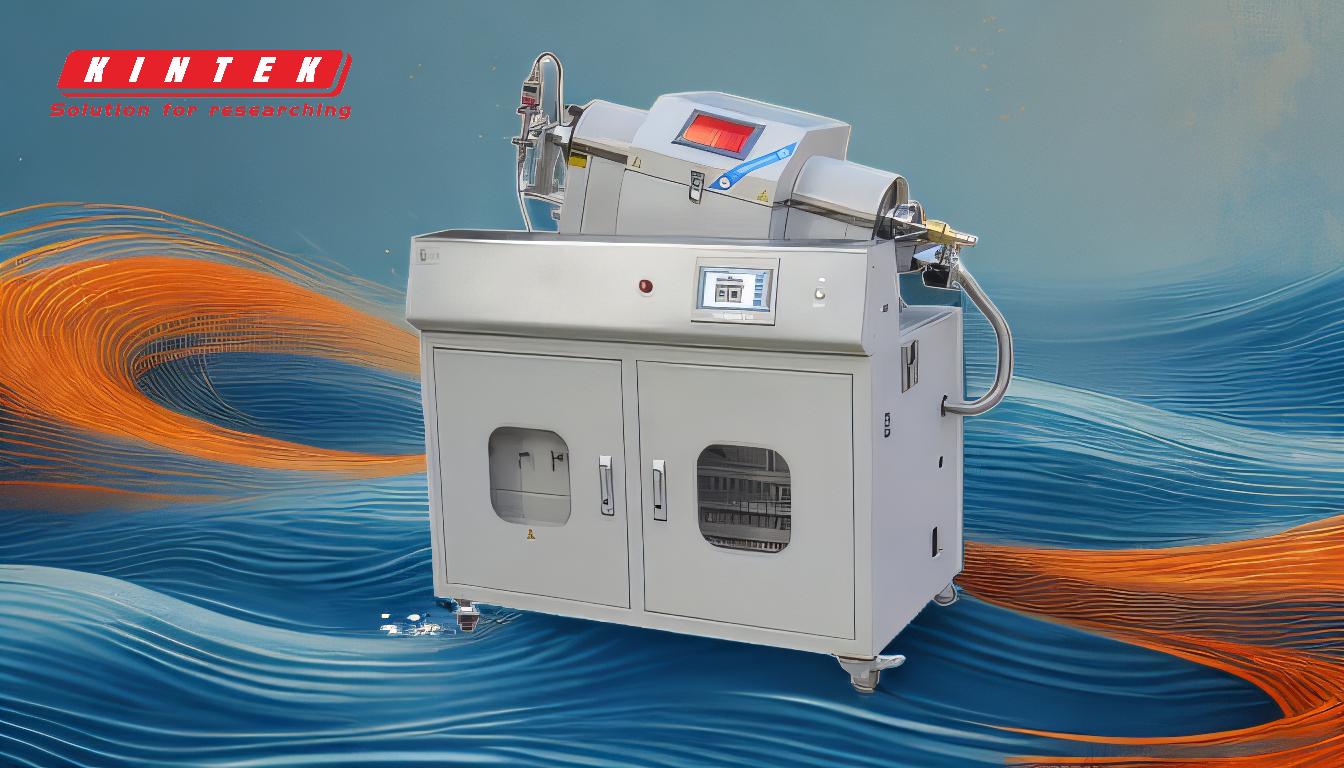
-
Chemical Deposition Methods:
- Electroplating: This method involves the deposition of a thin layer of metal onto a substrate using an electric current. It is commonly used for creating conductive layers in electronic devices.
- Sol-Gel: A wet-chemical technique that involves the transition of a solution into a gel, which is then dried and sintered to form a thin film. This method is often used for creating oxide films.
- Dip Coating: The substrate is dipped into a solution and then withdrawn at a controlled speed, leaving a thin film on the surface. This method is simple and cost-effective.
- Spin Coating: A solution is applied to a substrate, which is then spun at high speeds to spread the solution evenly and form a thin film. This method is widely used in the semiconductor industry.
- Chemical Vapor Deposition (CVD): A process where a substrate is exposed to one or more volatile precursors, which react and/or decompose on the substrate surface to produce the desired thin film. CVD is used for high-quality, uniform films.
- Plasma-Enhanced CVD (PECVD): A variation of CVD that uses plasma to enhance the chemical reaction rates, allowing for lower temperature deposition. This is useful for temperature-sensitive substrates.
- Atomic Layer Deposition (ALD): A method that deposits films one atomic layer at a time, allowing for extremely precise control over film thickness and composition. ALD is used for high-performance applications.
-
Physical Deposition Methods:
- Sputtering: A process where atoms are ejected from a solid target material due to bombardment of the target by energetic particles. The ejected atoms then deposit onto a substrate to form a thin film. Sputtering is widely used in the production of thin films for electronics and optics.
- Thermal Evaporation: A method where the source material is heated to a high temperature in a vacuum, causing it to evaporate and deposit onto a substrate. This is commonly used for creating metallic thin films.
- Carbon Coating: A specialized form of sputtering or evaporation used to deposit thin layers of carbon, often used in electron microscopy.
- Electron Beam Evaporation: A technique where an electron beam is used to heat the source material, causing it to evaporate and deposit onto a substrate. This method allows for high-purity films.
- Molecular Beam Epitaxy (MBE): A highly controlled process where beams of atoms or molecules are directed at a substrate to grow a thin film layer by layer. MBE is used for high-quality semiconductor films.
- Pulsed Laser Deposition (PLD): A method where a high-power pulsed laser is used to ablate material from a target, which then deposits onto a substrate. PLD is used for complex oxide films.
-
Materials Used in Thin Films:
- Polymers: Organic materials that can be used to create flexible and lightweight thin films, often used in flexible electronics and solar cells.
- Ceramics: Inorganic, non-metallic materials that are used for their high thermal and chemical stability, often used in protective coatings and sensors.
- Inorganic Compounds: Materials like oxides, nitrides, and sulfides that are used for their electrical, optical, and mechanical properties, often used in semiconductors and optical coatings.
-
Applications of Thin Films:
- Electronics: Thin films are used in the production of semiconductors, integrated circuits, and displays.
- Optics: Thin films are used to create anti-reflective coatings, mirrors, and optical filters.
- Energy: Thin films are used in solar cells, batteries, and fuel cells.
- Protective Coatings: Thin films are used to protect surfaces from corrosion, wear, and environmental damage.
By understanding the various methods and materials used in thin film deposition, one can select the most appropriate technique for a specific application, ensuring optimal performance and efficiency.
Summary Table:
Category | Methods | Applications |
---|---|---|
Chemical Methods | Electroplating, Sol-Gel, Dip Coating, Spin Coating, CVD, PECVD, ALD | Electronics, Optics, Energy, Protective Coatings |
Physical Methods | Sputtering, Thermal Evaporation, Carbon Coating, MBE, PLD | Electronics, Optics, Energy, High-Performance Films |
Materials | Polymers, Ceramics, Inorganic Compounds (Oxides, Nitrides, Sulfides) | Flexible Electronics, Solar Cells, Protective Coatings, Semiconductors |
Need help selecting the right thin film deposition method? Contact our experts today!