Furnace brazing is a highly efficient and cost-effective method for achieving high production rates, reduced costs, and uniform braze quality. It is particularly advantageous due to its ability to join dissimilar materials, form multiple joints simultaneously, and provide precise control over heating and cooling cycles. This process minimizes residual stress and distortion, making it ideal for high-precision assemblies. Additionally, furnace brazing can integrate heat treatments like hardening or annealing, further saving time and costs. The clean atmosphere used in furnace brazing often eliminates the need for fluxes and post-braze cleaning, enhancing overall efficiency and quality.
Key Points Explained:
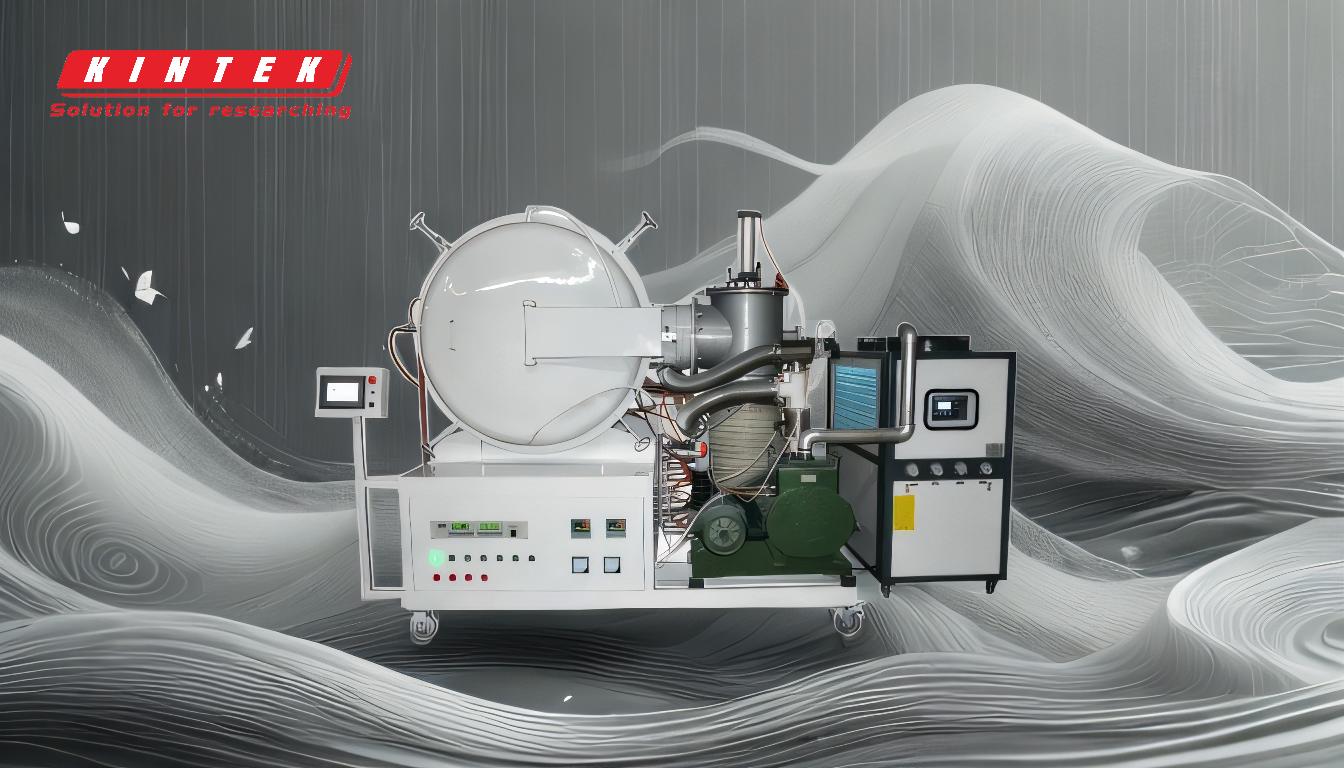
-
High Production Rate:
- Furnace brazing allows for the simultaneous joining of multiple joints, significantly increasing production rates. This is particularly beneficial in high-volume manufacturing environments where time efficiency is crucial.
-
Reduced Costs:
- The process eliminates the need for fluxes and post-braze cleaning, reducing material and labor costs. Additionally, the ability to combine heat treatments like hardening or annealing with the brazing process saves both time and money.
-
Uniform Braze Quality:
- Precise control over heating and cooling cycles ensures temperature uniformity, leading to minimal distortion and consistent braze quality. This is essential for high-precision assemblies where uniformity is critical.
-
Joining Dissimilar Materials:
- Furnace brazing is capable of joining dissimilar materials, which is often a challenge with other brazing methods. This versatility expands the range of applications and materials that can be effectively brazed.
-
Minimal Distortion and Residual Stress:
- The controlled environment of furnace brazing minimizes residual stress and distortion, ensuring the integrity and precision of the final product. This is particularly important for components that require high dimensional accuracy.
-
Step Brazing and Multiple Alloys:
- Furnace brazing supports step brazing using multiple braze alloys, allowing for complex assemblies with varying material requirements. This flexibility enhances the process's applicability to a wide range of industrial applications.
-
Integration with Heat Treatments:
- The ability to combine brazing with other heat treatments like hardening or annealing not only saves time but also improves the mechanical properties of the final product. This integration is a significant advantage in terms of both efficiency and performance.
In summary, furnace brazing stands out as a superior method for achieving high production rates, reduced costs, and uniform braze quality. Its ability to handle multiple joints, join dissimilar materials, and integrate with other heat treatments makes it an ideal choice for a wide range of industrial applications.
Summary Table:
Advantages of Furnace Brazing | Key Benefits |
---|---|
High Production Rate | Simultaneous joining of multiple joints for faster production. |
Reduced Costs | Eliminates fluxes and post-braze cleaning, saving time and labor. |
Uniform Braze Quality | Precise control over heating and cooling ensures consistent results. |
Joining Dissimilar Materials | Versatile process for brazing different materials effectively. |
Minimal Distortion and Stress | Controlled environment reduces distortion and ensures precision. |
Step Brazing with Multiple Alloys | Supports complex assemblies with varying material needs. |
Integration with Heat Treatments | Combines brazing with hardening or annealing for enhanced efficiency. |
Ready to optimize your brazing process? Contact us today to learn how furnace brazing can benefit your operations!