A tilting furnace, such as a rotating furnace, is a versatile piece of equipment used in metal melting processes. It is designed to handle a wide range of metals, including base metals like copper, aluminum, iron, and steel, as well as precious metals such as gold, silver, and rhodium. The furnace's ability to tilt allows for efficient pouring of molten metal into molds or other containers. The melting process is influenced by the furnace's design, heating method, and the specific melting points of the metals involved. Understanding these factors ensures the furnace is suitable for the intended application.
Key Points Explained:
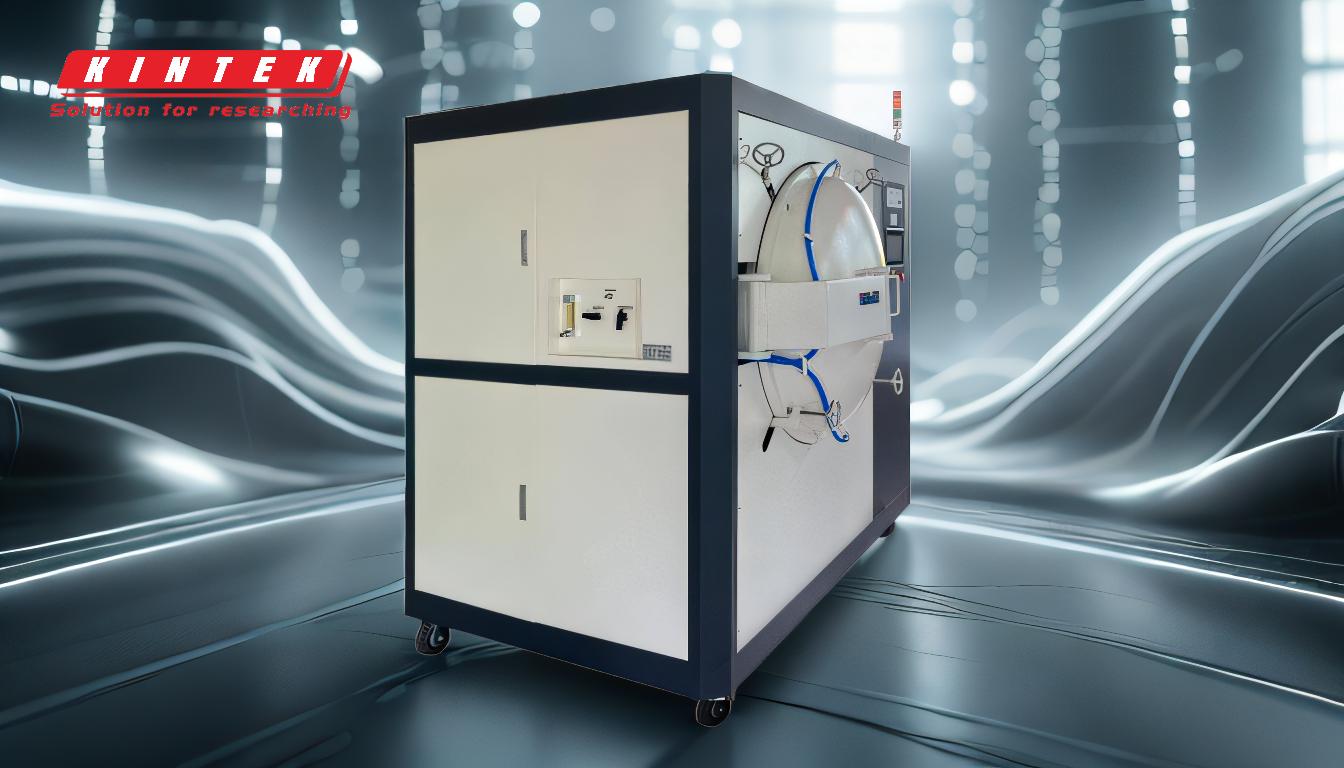
-
Types of Metals Suitable for Tilting Furnaces:
-
Base Metals: Tilting furnaces are commonly used to melt base metals such as:
- Copper: Widely used in electrical applications due to its excellent conductivity.
- Aluminum: Lightweight and corrosion-resistant, used in aerospace and automotive industries.
- Iron and Steel: Essential for construction and manufacturing, with steel being an alloy of iron and carbon.
-
Precious Metals: These furnaces can also handle precious metals like:
- Gold and Silver: Used in jewelry, electronics, and investment.
- Rhodium: A rare metal used in catalytic converters and jewelry plating.
-
Base Metals: Tilting furnaces are commonly used to melt base metals such as:
-
Melting Points and Furnace Suitability:
- Each metal has a unique melting point, which determines the furnace's required temperature range. For example:
- Steel: Melts at approximately 1,370°C.
- Copper: Melts at around 1,085°C.
- Aluminum: Melts at about 660°C.
- Gold: Melts at 1,064°C.
- The furnace must be capable of reaching and maintaining these temperatures to ensure efficient melting.
- Each metal has a unique melting point, which determines the furnace's required temperature range. For example:
-
Design and Functionality of Tilting Furnaces:
- Tilting furnaces are designed with a tilting mechanism that allows for precise pouring of molten metal. This feature is particularly useful in foundries and metal casting operations.
- The furnace typically includes an input door at the top for loading metal into the melting chamber.
- Heating methods can vary, including gas, oil, or electric induction, depending on the furnace type and application.
-
Applications of Tilting Furnaces:
- Foundries: Used for casting metal parts by melting and pouring metal into molds.
- Jewelry Making: Ideal for melting precious metals for crafting intricate designs.
- Manufacturing: Used in the production of components for various industries, including automotive, aerospace, and electronics.
-
Advantages of Using Tilting Furnaces:
- Efficiency: The tilting mechanism allows for controlled pouring, reducing waste and improving precision.
- Versatility: Capable of melting a wide range of metals, making it suitable for diverse applications.
- Safety: The design minimizes the risk of spills and accidents during the pouring process.
In conclusion, tilting furnaces, including rotating furnaces, are highly effective for melting a variety of metals, from base metals like copper and aluminum to precious metals like gold and silver. Their design, combined with the ability to reach high temperatures, makes them indispensable in industries requiring precise and efficient metal melting processes.
Summary Table:
Metal Type | Examples | Melting Point | Applications |
---|---|---|---|
Base Metals | Copper, Aluminum, Iron, Steel | 660°C - 1,370°C | Electrical, aerospace, automotive, construction, manufacturing |
Precious Metals | Gold, Silver, Rhodium | 1,064°C - 1,964°C | Jewelry, electronics, investment, catalytic converters, jewelry plating |
Discover the perfect tilting furnace for your metal melting needs—contact us today to learn more!