Protective atmospheres are essential in sintering to ensure the quality and integrity of the final product. They prevent oxidation, regulate chemical reactions such as decarburization and deoxidization, and maintain the desired carbon content in powdered metals. By using inert gases, hydrogen, or specific gas mixtures, the sintering process can achieve a clean, carbon-rich, and deoxidized product, free from contaminants like pressing lubricants. The choice of atmosphere depends on the metallic compounds being sintered and is critical for optimizing both the material properties and the cost-effectiveness of the process. Protective atmospheres also support surface treatment and enhance furnace efficiency, making them indispensable in sintering.
Key Points Explained:
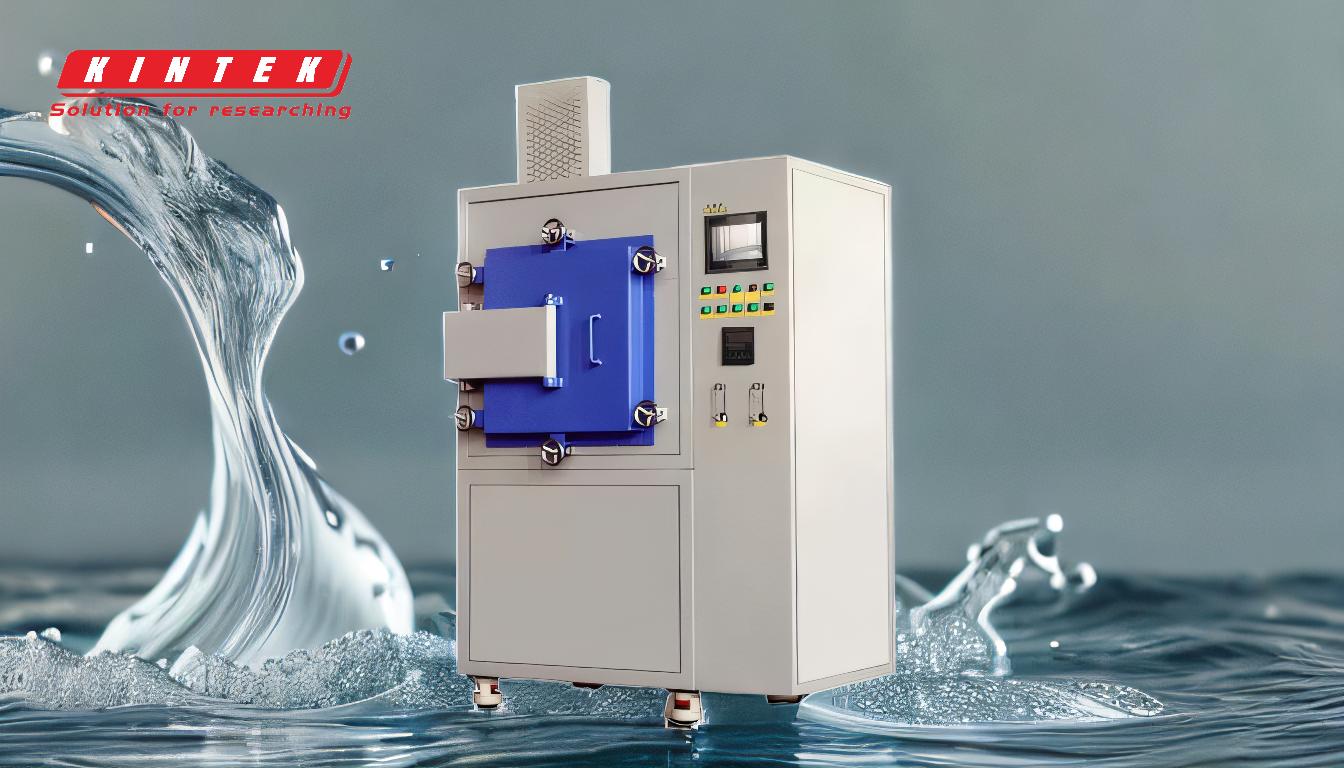
-
Prevention of Oxidation:
- Sintering involves heating powdered metals to high temperatures, which can cause oxidation if exposed to air. Oxidation degrades the material's properties, leading to poor-quality products.
- Protective atmospheres, such as inert gases (e.g., argon, nitrogen) or hydrogen, create an oxygen-free environment, preventing oxidation and ensuring the material retains its desired properties.
-
Regulation of Chemical Reactions:
- Protective atmospheres help control critical chemical reactions during sintering, such as decarburization (loss of carbon) and deoxidization (removal of oxygen).
- For example, active oxygenless atmospheres like hydrogen-nitrogen mixtures or methane additives are used to maintain carbon-rich conditions and ensure complete deoxidization of the powdered metals.
-
Maintenance of Carbon Content:
- Carbon plays a vital role in determining the hardness, strength, and wear resistance of sintered products. Protective atmospheres help preserve the carbon content in powdered metals, ensuring the final product meets the required specifications.
-
Removal of Contaminants:
- Pressing lubricants, used during the compaction of powdered metals, must be removed during sintering to avoid contamination. Protective atmospheres facilitate the decomposition and removal of these lubricants, resulting in a clean and high-quality sintered product.
-
Optimization of Material Properties:
- The choice of sintering atmosphere directly impacts the mechanical and physical properties of the final product. For instance, hydrogen atmospheres are often used for sintering stainless steel to achieve a bright, oxide-free surface.
-
Cost-Effectiveness:
- Selecting the appropriate protective atmosphere ensures a balance between achieving the desired material properties and minimizing operating costs. For example, nitrogen-based atmospheres are often more cost-effective than pure hydrogen for certain applications.
-
Support for Surface Treatment:
- Protective atmospheres contribute to the cleanliness of the sintered product, making it easier to apply subsequent surface treatments like coating or plating. This enhances the functionality and durability of the final product.
-
Enhanced Furnace Efficiency:
- By maintaining a controlled atmosphere, sintering furnaces operate more efficiently, reducing energy consumption and improving overall process reliability.
In summary, protective atmospheres are a critical component of the sintering process, ensuring high-quality products by preventing oxidation, regulating chemical reactions, maintaining carbon content, and removing contaminants. The choice of atmosphere depends on the specific metallic compounds and desired outcomes, balancing performance and cost-effectiveness.
Summary Table:
Key Benefits of Protective Atmospheres | Details |
---|---|
Prevention of Oxidation | Inert gases or hydrogen create oxygen-free environments to prevent material degradation. |
Regulation of Chemical Reactions | Controls decarburization and deoxidization for optimal carbon-rich conditions. |
Maintenance of Carbon Content | Preserves hardness, strength, and wear resistance in sintered products. |
Removal of Contaminants | Eliminates pressing lubricants for clean, high-quality results. |
Optimization of Material Properties | Enhances mechanical and physical properties for specific applications. |
Cost-Effectiveness | Balances performance and operating costs with tailored gas mixtures. |
Support for Surface Treatment | Ensures cleanliness for effective coating or plating. |
Enhanced Furnace Efficiency | Improves energy efficiency and process reliability. |
Optimize your sintering process with the right protective atmosphere—contact our experts today for tailored solutions!