Scanning Electron Microscopy (SEM) is a powerful tool used to observe the surface morphology of samples at a very high resolution. However, many samples, especially non-conductive ones, can accumulate static charges when exposed to the electron beam, leading to image distortions and poor quality. Coating samples with a thin layer of carbon is a common practice to mitigate these issues. Carbon coating provides conductivity, reduces charging effects, and enhances the secondary electron emission, which improves image clarity and detail. Additionally, carbon is chosen because it is relatively inert, does not interfere with the sample's composition, and is compatible with high-vacuum environments.
Key Points Explained:
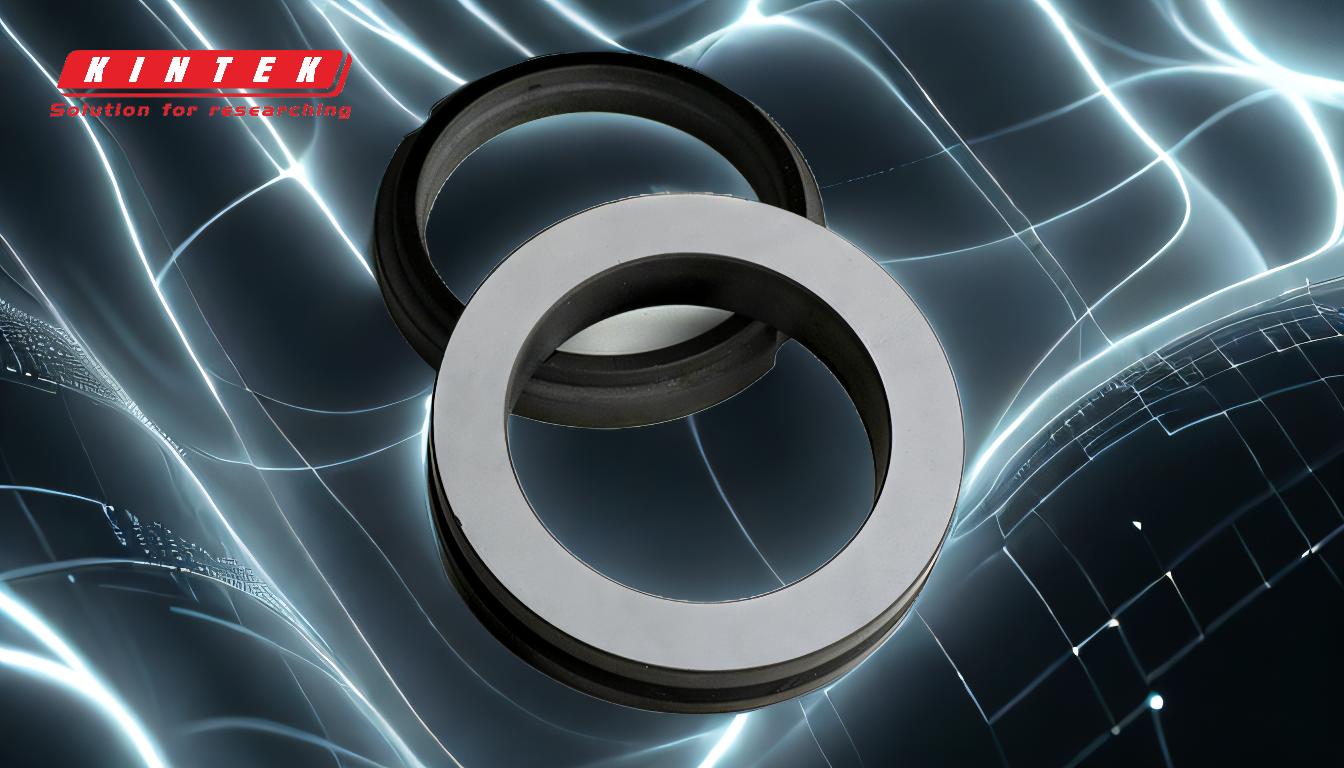
-
Prevention of Charging Effects:
- Non-conductive samples tend to accumulate static electric charges when bombarded with the electron beam in SEM. This charging can distort the image and make it difficult to obtain clear, high-resolution pictures.
- Carbon coating provides a conductive layer that dissipates these charges, ensuring that the electron beam interacts uniformly with the sample surface. This results in clearer and more accurate imaging.
-
Enhancement of Secondary Electron Emission:
- Secondary electrons are crucial for creating the detailed surface images in SEM. Carbon coating increases the emission of secondary electrons from the sample surface.
- This enhancement leads to better contrast and resolution in the SEM images, allowing for more detailed analysis of the sample's surface features.
-
Compatibility with High-Vacuum Environments:
- SEM operates under high vacuum conditions to prevent scattering of the electron beam by air molecules. Carbon is stable and does not outgas significantly under these conditions.
- This stability ensures that the vacuum integrity is maintained, and the carbon coating does not introduce contaminants that could interfere with the imaging process.
-
Chemical Inertness and Minimal Interference:
- Carbon is chemically inert and does not react with most samples. This inertness ensures that the coating does not alter the sample's composition or structure.
- For samples that require elemental analysis, carbon coating is preferable because it does not introduce additional elements that could complicate the analysis.
-
Uniform Coating and Thin Layer Application:
- Carbon can be applied in very thin, uniform layers using techniques like sputter coating or evaporation. This uniformity is crucial for maintaining the sample's surface features without obscuring them.
- The thin layer is sufficient to provide conductivity and enhance electron emission without adding significant thickness that could mask fine details.
-
Cost-Effectiveness and Availability:
- Carbon is relatively inexpensive and readily available, making it a practical choice for routine SEM sample preparation.
- The ease of application and the effectiveness of carbon coating make it a standard practice in many SEM laboratories.
In summary, coating SEM samples with carbon is essential for preventing charging effects, enhancing image quality, and ensuring compatibility with the high-vacuum environment of the SEM. Its chemical inertness, ability to form uniform thin layers, and cost-effectiveness make it an ideal choice for improving the performance and reliability of SEM imaging.
Summary Table:
Key Benefits of Carbon Coating | Details |
---|---|
Prevents Charging Effects | Dissipates static charges, ensuring clear imaging. |
Enhances Secondary Electron Emission | Improves image contrast and resolution. |
Compatible with High-Vacuum | Stable under SEM conditions, maintains vacuum integrity. |
Chemically Inert | Does not alter sample composition or interfere with analysis. |
Uniform Thin Layer Application | Preserves surface features without masking details. |
Cost-Effective | Affordable and widely available for routine use. |
Need help optimizing your SEM sample preparation? Contact our experts today for tailored solutions!