Argon is widely used in annealing processes due to its inert properties, which prevent oxidation and other chemical reactions with metals during high-temperature treatments. Its ability to create a non-reactive atmosphere ensures that the metal's surface remains clean and free from impurities, which is critical for maintaining the material's mechanical and chemical properties. Additionally, argon's low oxygen content and low dew point make it ideal for applications requiring precise control over the environment. While argon is more expensive than other gases, its benefits in preserving metal quality and preventing defects often justify its use in annealing processes.
Key Points Explained:
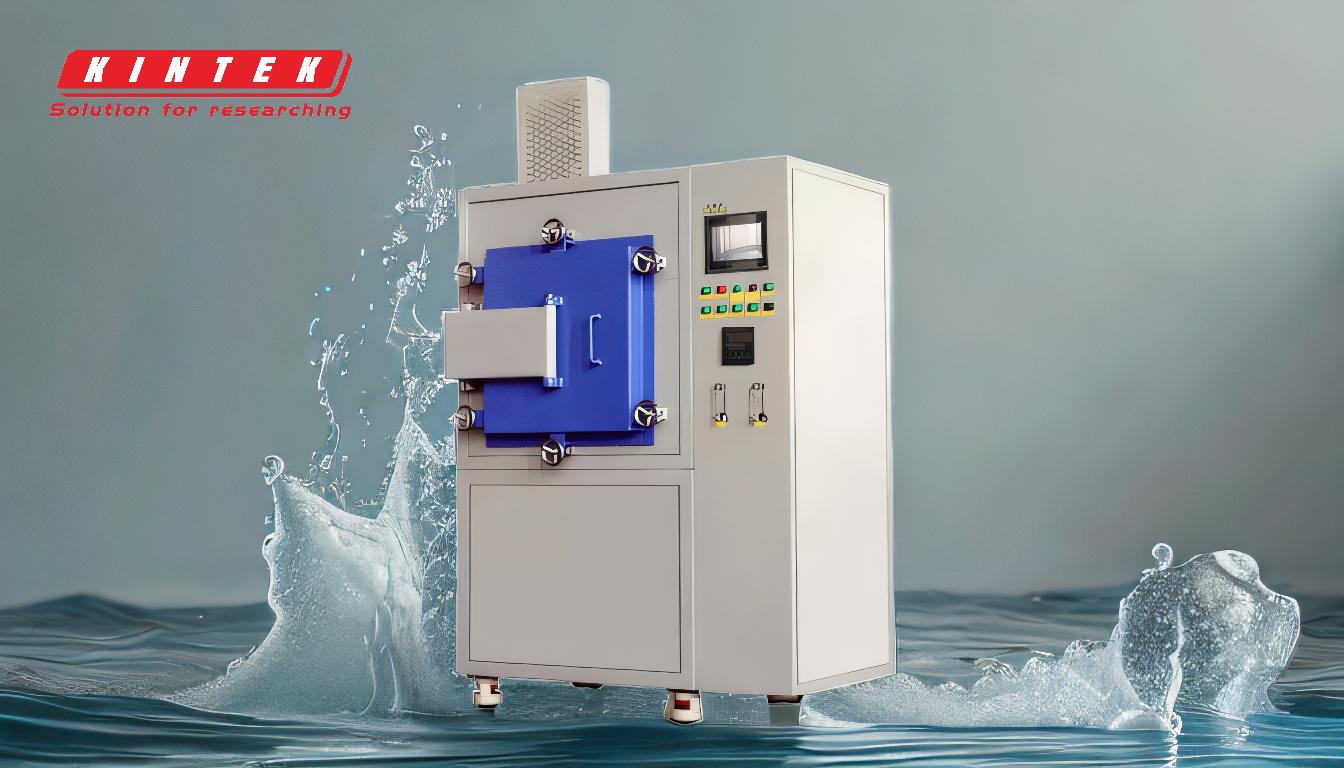
-
Inert Nature of Argon:
- Argon is a noble gas, meaning it is chemically inert and does not react with metals or other materials, even at high temperatures.
- This inertness is crucial in annealing, as it prevents oxidation, scaling, and other surface reactions that could degrade the metal's quality.
- By creating a non-reactive atmosphere, argon ensures that the metal retains its desired properties, such as strength, ductility, and corrosion resistance.
-
Prevention of Oxidation:
- During annealing, metals are heated to high temperatures, which can make them highly reactive with oxygen in the air.
- Oxidation can lead to the formation of oxides on the metal surface, which can weaken the material and cause defects.
- Argon's inert atmosphere eliminates the risk of oxidation, ensuring that the metal surface remains clean and free from impurities.
-
Low Oxygen Content and Dew Point:
- Argon is typically delivered with an oxygen content below 20 ppm and a dew point less than -75°F (-59°C).
- These specifications ensure that the annealing environment is free from moisture and oxygen, which are common sources of contamination.
- This level of purity is particularly important for high-precision applications, such as in the aerospace and electronics industries.
-
Applications in Specific Metals:
- Non-Ferrous Metals: Argon is commonly used for annealing non-ferrous metals like copper, aluminum, and titanium, which are highly susceptible to oxidation.
- Stainless Steel and Alloy Steel: Argon prevents the formation of chromium oxides and nitrides, which can compromise the corrosion resistance and mechanical properties of these materials.
- Specialty Alloys: Argon is essential for annealing specialty alloys, where even minor contamination can lead to significant performance issues.
-
Cost Considerations:
- While argon is more expensive than other gases like nitrogen, its benefits in preserving metal quality often outweigh the cost.
- In applications where high cooling rates cannot be achieved, argon-based mixtures are preferred to avoid the precipitation of harmful compounds like chromium nitrides.
- The cost of using argon is justified by the improved material properties and reduced risk of defects in the final product.
-
Additional Industrial Uses:
- Beyond annealing, argon is used in welding, casting, and other high-temperature processes where a non-reactive atmosphere is required.
- In steel manufacturing, argon reduces chromium losses, and in aluminum production, it aids in hydrogen removal and degasification.
- These applications further highlight argon's versatility and importance in maintaining material integrity across various industries.
By understanding these key points, it becomes clear why argon is the preferred choice for annealing processes, particularly in industries where material quality and performance are critical.
Summary Table:
Key Aspect | Details |
---|---|
Inert Nature | Prevents oxidation, scaling, and surface reactions at high temperatures. |
Oxidation Prevention | Eliminates risk of oxides forming on metal surfaces, ensuring cleanliness. |
Low Oxygen Content & Dew Point | Oxygen < 20 ppm, dew point < -75°F (-59°C) for contamination-free environments. |
Applications | Used for non-ferrous metals, stainless steel, alloy steel, and specialty alloys. |
Cost Justification | Higher cost offset by improved material quality and reduced defects. |
Industrial Uses | Welding, casting, steel manufacturing, and aluminum production. |
Interested in optimizing your annealing process with argon? Contact our experts today to learn more!