Vacuum plays a crucial role in the coating process, particularly in ensuring the quality and durability of the final product. When applying coatings, especially in processes like Physical Vapor Deposition (PVD) or Chemical Vapor Deposition (CVD), maintaining a vacuum environment is essential. This environment prevents contamination from atmospheric gases, ensures uniform coating application, and enhances the adhesion of the coating material to the substrate. The vacuum cleaning furnace is particularly important in this context, as it helps maintain the cleanliness and efficiency of the vacuum environment, which is vital for achieving high-quality coatings.
Key Points Explained:
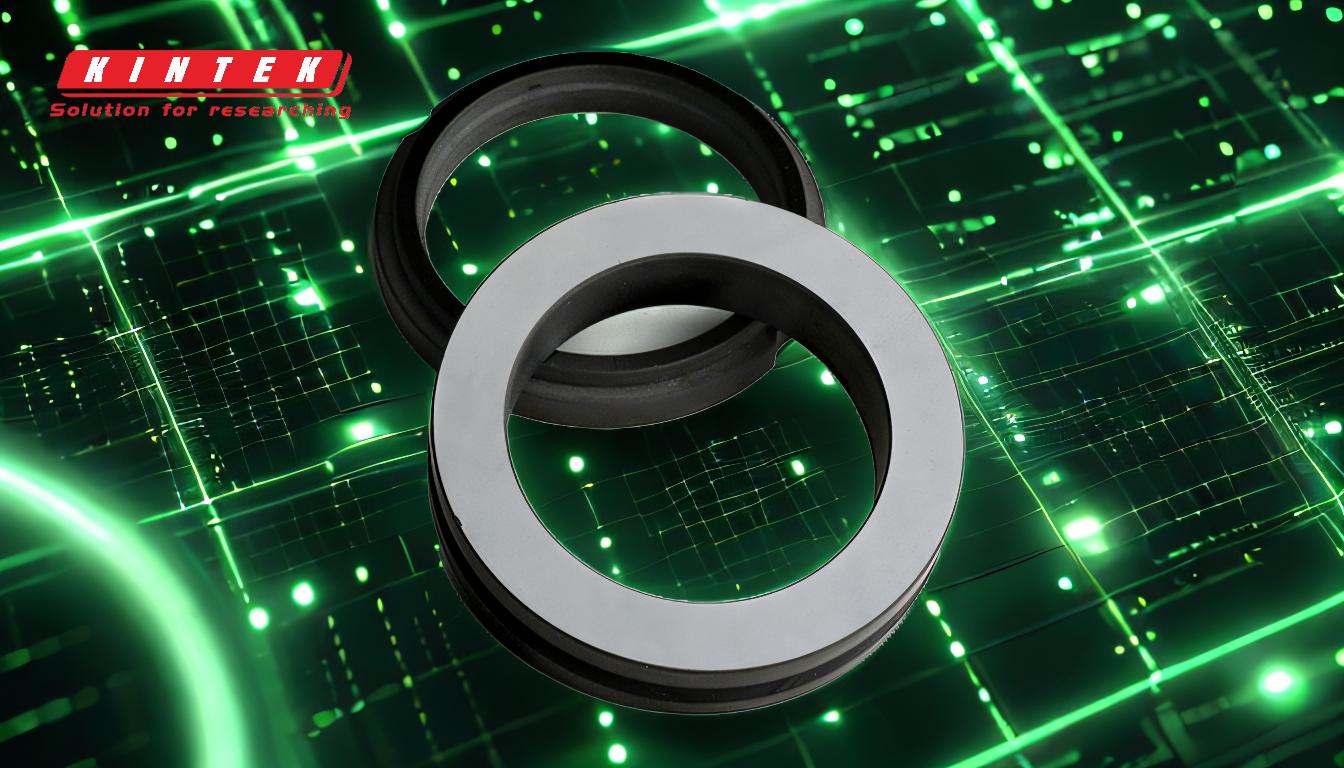
-
Prevention of Contamination:
- Atmospheric Gases: In a vacuum environment, the presence of atmospheric gases like oxygen, nitrogen, and water vapor is minimized. These gases can react with the coating material, leading to impurities and defects in the coating.
- Oxidation and Corrosion: Without a vacuum, metals and other materials can oxidize or corrode, which compromises the integrity of the coating. A vacuum environment prevents these reactions, ensuring a pure and stable coating process.
-
Uniform Coating Application:
- Even Distribution: In a vacuum, the coating material can be evenly distributed across the substrate. This is because the absence of air molecules allows the coating particles to travel in straight lines without interference, leading to a more uniform layer.
- Controlled Thickness: Vacuum conditions allow for precise control over the thickness of the coating. This is crucial for applications where specific thicknesses are required for optimal performance, such as in optical coatings or semiconductor devices.
-
Enhanced Adhesion:
- Surface Preparation: A vacuum environment helps in preparing the substrate surface by removing any adsorbed gases or contaminants. This clean surface allows for better adhesion of the coating material.
- Stronger Bonds: The absence of air molecules in a vacuum allows the coating material to form stronger bonds with the substrate. This results in a more durable and long-lasting coating.
-
Role of the Vacuum Cleaning Furnace:
- Maintaining Cleanliness: The vacuum cleaning furnace is essential for maintaining the cleanliness of the vacuum environment. It helps remove any residual contaminants that could affect the coating process.
- Efficiency: By keeping the vacuum environment clean, the furnace ensures that the coating process is efficient and that the equipment operates at optimal performance levels.
-
Calibration and Monitoring:
- Vacuum Pressure: As mentioned in the reference, vacuum pressure is a critical factor. A gradual slip in vacuum pressure can lead to issues in the final outcome of the coating. Regular calibration and monitoring of the vacuum pressure are necessary to maintain the desired conditions.
- Use of Vacuum Gauges: For older furnaces, a low-cost method to confirm the vacuum is to use a vacuum gauge. This tool helps in monitoring the vacuum pressure and ensuring that it remains within the required range.
In summary, the use of a vacuum in coating processes is indispensable for achieving high-quality, durable, and uniform coatings. The vacuum environment prevents contamination, ensures even distribution of the coating material, and enhances adhesion. The vacuum cleaning furnace plays a vital role in maintaining the cleanliness and efficiency of the vacuum environment, which is crucial for the success of the coating process. Regular monitoring and calibration of vacuum pressure are also essential to ensure optimal performance and quality of the final product.
Summary Table:
Key Benefits of Vacuum in Coating Processes | Details |
---|---|
Prevents Contamination | Minimizes atmospheric gases (e.g., oxygen, nitrogen) that can cause impurities and defects. |
Ensures Uniform Coating | Allows even distribution of coating material and precise thickness control. |
Enhances Adhesion | Prepares substrate surfaces for stronger, more durable bonds. |
Role of Vacuum Cleaning Furnace | Maintains cleanliness and efficiency of the vacuum environment. |
Calibration & Monitoring | Regular monitoring of vacuum pressure ensures optimal coating quality. |
Optimize your coating process with vacuum technology—contact our experts today for tailored solutions!