Chemical vapor deposition (CVD) is a widely used technique for depositing thin films and coatings on various substrates. It is favored for its versatility, precision, and ability to produce high-quality, durable materials. CVD is employed across industries, including electronics, manufacturing, and energy, due to its ability to deposit a wide range of materials, such as metals, ceramics, and semiconductors. The process involves chemical reactions in the vapor phase, which allows for precise control over film properties and thickness. This makes it ideal for applications like semiconductor fabrication, corrosion-resistant coatings, and solar cell production. Its advantages include high purity, durability, and the ability to coat complex surfaces, making it a cornerstone of modern material science and engineering.
Key Points Explained:
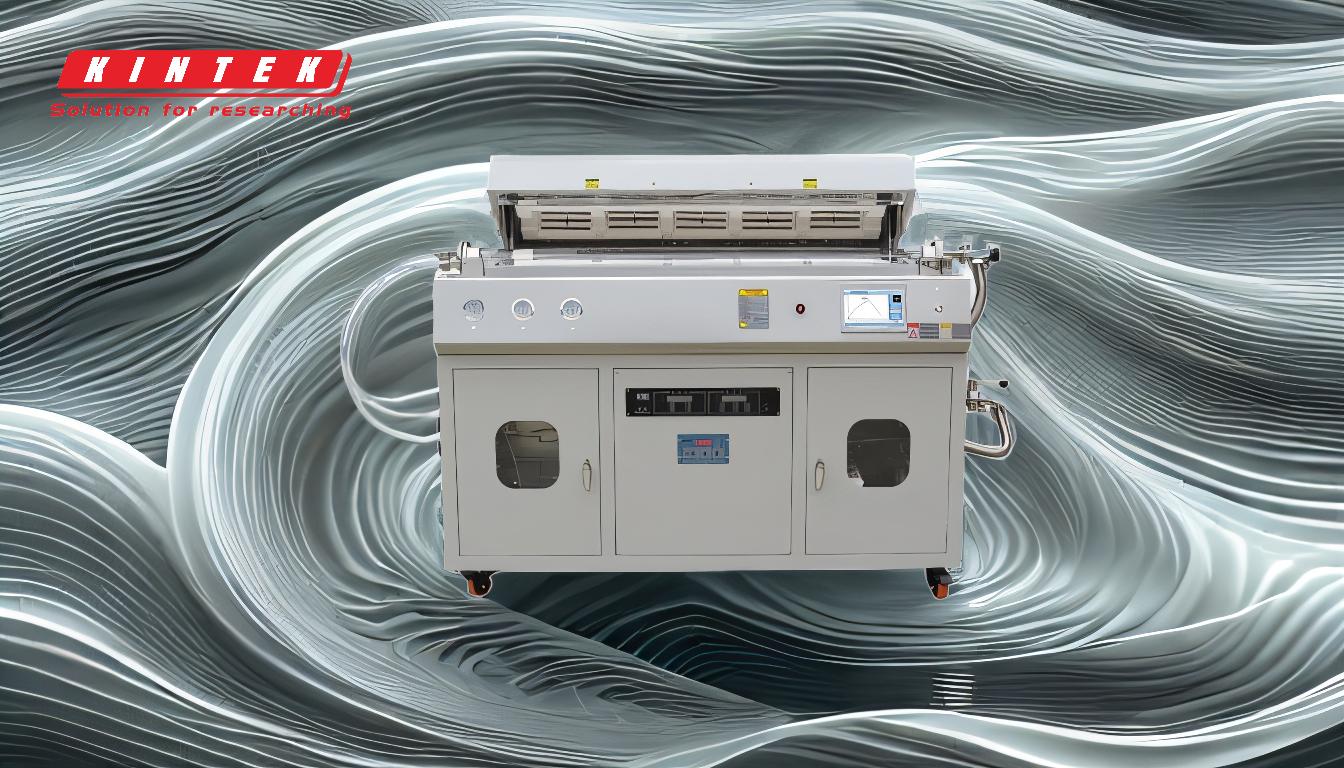
-
Versatility in Material Deposition
- Chemical vapor deposition (CVD) is capable of depositing a wide variety of materials, including metals, ceramics, and semiconductors. This makes it suitable for diverse applications, from electronics to cutting tools.
- For example, it is used to grow carbon nanotubes, GaN nanowires, and other advanced materials, as well as to deposit thin films for semiconductors and photovoltaic materials in solar cells.
-
High-Quality and Durable Coatings
- CVD produces coatings with high purity, density, and durability. These coatings can withstand high-stress environments, extreme temperatures, and temperature variations.
- The process ensures good crystallinity and low residual stress, which are critical for applications requiring precise material properties.
-
Precision and Control
- CVD allows for precise control over the deposition process, including timing, thickness, and material properties. This is achieved by adjusting parameters such as temperature, pressure, and gas composition.
- This level of control is essential for creating ultra-thin layers, which are crucial in applications like electrical circuits and semiconductor devices.
-
Ability to Coat Complex Surfaces
- One of the standout features of CVD is its ability to coat complex and precision surfaces with uniform layers. This "wrap-around" property ensures consistent coverage even on intricate geometries.
- This makes it ideal for applications in cutting tools, where coatings must protect against wear and corrosion, and in electronics, where uniform thin films are required.
-
Wide Range of Applications
- CVD is used across multiple industries, including electronics, manufacturing, and renewable energy. For instance:
- In electronics, it deposits thin films on semiconductors.
- In manufacturing, it creates wear-resistant coatings for cutting tools.
- In renewable energy, it is used to produce thin-film solar cells by depositing photovoltaic materials on substrates.
- CVD is used across multiple industries, including electronics, manufacturing, and renewable energy. For instance:
-
Advantages Over Physical Vapor Deposition (PVD)
- Unlike physical processes like evaporation and sputtering (used in PVD), CVD relies on chemical reactions in the vapor phase. This allows for better control over film properties and the ability to deposit a wider range of materials.
- CVD is also more versatile and can produce coatings with superior durability and performance.
-
Ease of Operation and Maintenance
- CVD equipment is relatively simple to operate and maintain, making it accessible for industrial use. This ease of use, combined with its high performance, contributes to its widespread adoption.
-
Customizability for Specific Needs
- The gases used in CVD can be optimized for specific properties, such as corrosion resistance, abrasion resistance, or high purity. This customizability ensures that the coatings meet the exact requirements of the application.
By leveraging these advantages, chemical vapor deposition has become an indispensable tool in modern material science and engineering, enabling advancements in technology and industry.
Summary Table:
Key Feature | Description |
---|---|
Versatility | Deposits metals, ceramics, and semiconductors for diverse applications. |
High-Quality Coatings | Produces durable, high-purity coatings resistant to extreme conditions. |
Precision and Control | Enables precise control over film thickness, timing, and material properties. |
Complex Surface Coating | Uniformly coats intricate geometries, ideal for electronics and cutting tools. |
Wide Applications | Used in semiconductors, renewable energy, and wear-resistant coatings. |
Advantages Over PVD | Superior durability, versatility, and material range compared to PVD. |
Ease of Operation | Simple to operate and maintain, making it accessible for industrial use. |
Customizability | Gases can be optimized for specific properties like corrosion resistance. |
Ready to leverage the power of chemical vapor deposition for your projects? Contact us today to learn more!