An induction furnace can blast or experience explosions due to several reasons, primarily related to improper operation, equipment failure, or material-related issues. The most common causes include moisture in the charge material, overloading, electrical faults, or cooling system failures. When moisture enters the furnace, it rapidly turns into steam, causing a sudden increase in pressure that can lead to an explosion. Electrical faults, such as short circuits or issues with the IGBT (Insulated Gate Bipolar Transistor) system, can also cause overheating or arcing, leading to blasts. Proper maintenance, monitoring, and adherence to safety protocols are crucial to prevent such incidents.
Key Points Explained:
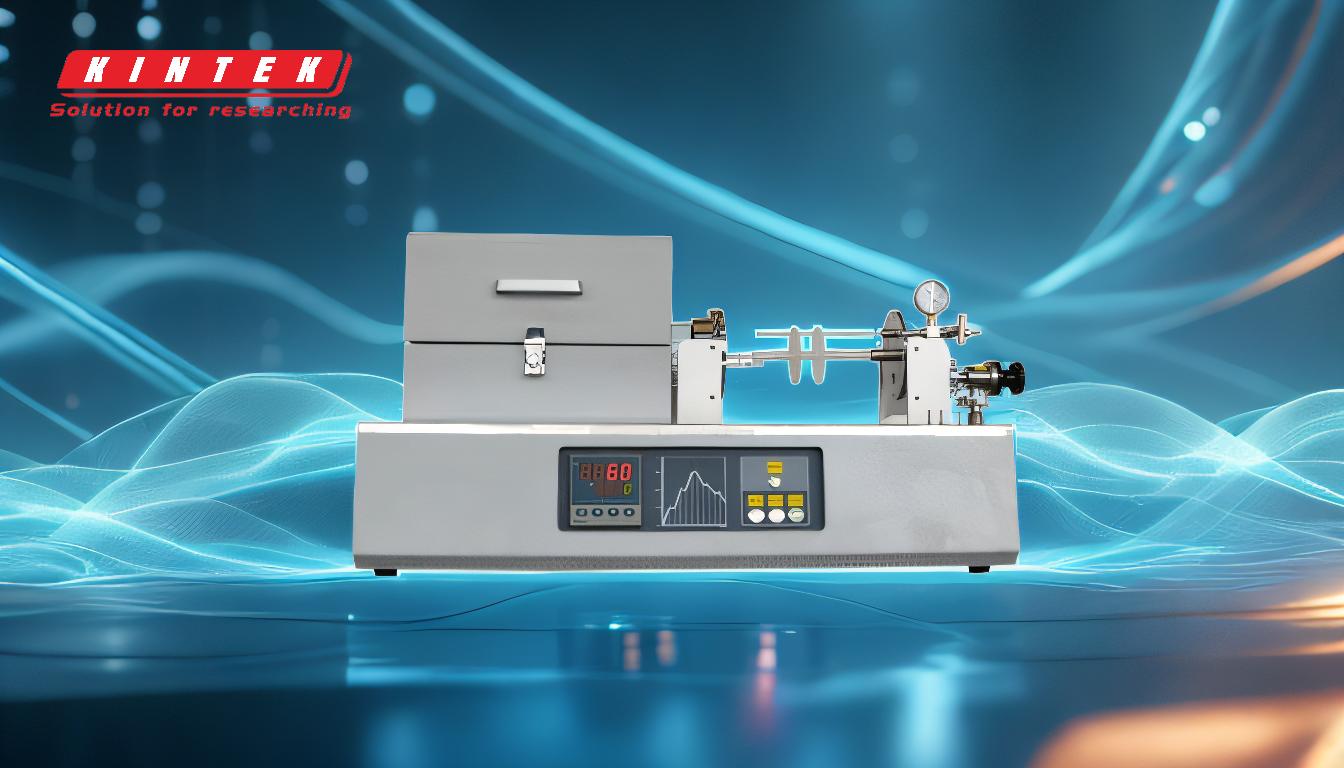
-
Moisture in Charge Material:
- When moisture is present in the charge material, it vaporizes rapidly upon contact with the high temperatures inside the furnace.
- This sudden vaporization creates a significant increase in pressure, which can lead to an explosion.
- To prevent this, ensure that all materials are thoroughly dried before being introduced into the furnace.
-
Overloading the Furnace:
- Overloading the furnace beyond its capacity can cause excessive heat buildup and pressure.
- This can lead to structural damage or even an explosion if the furnace cannot handle the load.
- Always adhere to the manufacturer's recommended capacity limits.
-
Electrical Faults:
- Electrical issues, such as short circuits or problems with the IGBT induction furnace system, can cause overheating or arcing.
- These faults can lead to sudden blasts if not detected and addressed promptly.
- Regular inspection and maintenance of the electrical components are essential to prevent such incidents.
-
Cooling System Failures:
- The cooling system is crucial for maintaining safe operating temperatures in the furnace.
- If the cooling system fails, the furnace can overheat, leading to potential explosions.
- Ensure that the cooling system is functioning correctly and that there are no blockages or leaks.
-
Improper Operation:
- Incorrect operation, such as rapid heating or cooling, can cause thermal stress on the furnace lining.
- This stress can lead to cracks or failures, increasing the risk of explosions.
- Follow proper operating procedures and avoid sudden temperature changes.
-
Material Contamination:
- Contaminants in the charge material, such as oils or other volatile substances, can react violently at high temperatures.
- These reactions can cause sudden pressure increases, leading to blasts.
- Ensure that all materials are clean and free from contaminants before use.
-
Lining Erosion:
- Over time, the furnace lining can erode due to the high temperatures and chemical reactions.
- If the lining becomes too thin, it can fail, leading to a blast.
- Regularly inspect and replace the furnace lining as needed to maintain safety.
-
Safety Protocols and Maintenance:
- Adhering to safety protocols and performing regular maintenance are critical to preventing blasts.
- This includes routine inspections, cleaning, and testing of all components.
- Ensure that all operators are trained and follow safety guidelines.
By understanding these key points and taking appropriate preventive measures, the risk of an induction furnace blast can be significantly reduced. Proper operation, regular maintenance, and adherence to safety protocols are essential to ensure the safe and efficient functioning of the furnace.
Summary Table:
Cause | Impact | Prevention |
---|---|---|
Moisture in Charge Material | Rapid vaporization causes pressure increase, leading to explosions. | Dry materials thoroughly before use. |
Overloading the Furnace | Excessive heat and pressure can cause structural damage or explosions. | Follow manufacturer’s capacity limits. |
Electrical Faults | Short circuits or IGBT issues cause overheating or arcing, leading to blasts. | Regularly inspect and maintain electrical components. |
Cooling System Failures | Overheating due to cooling system failure can lead to explosions. | Ensure cooling systems are functional and free of blockages or leaks. |
Improper Operation | Rapid heating/cooling causes thermal stress, increasing explosion risks. | Follow proper operating procedures and avoid sudden temperature changes. |
Material Contamination | Volatile substances react violently, causing pressure spikes and blasts. | Ensure materials are clean and free from contaminants. |
Lining Erosion | Thin or eroded lining can fail, leading to explosions. | Regularly inspect and replace the furnace lining as needed. |
Safety Protocols | Lack of maintenance and safety adherence increases blast risks. | Train operators and follow routine inspections, cleaning, and testing. |
Ensure your induction furnace operates safely—contact our experts today for maintenance and safety solutions!