Heat treatment is a critical process in casting because it enhances the physical and mechanical properties of the cast metal, making it suitable for specific industrial applications. By subjecting the material to controlled heating and cooling, heat treatment can improve strength, ductility, temperature resistance, and surface hardness. It also addresses issues like residual stress and porosity, which are common in cast components. This process ensures that the final product meets the desired balance between cost and quality, making it indispensable in industries such as aerospace, automotive, and manufacturing.
Key Points Explained:
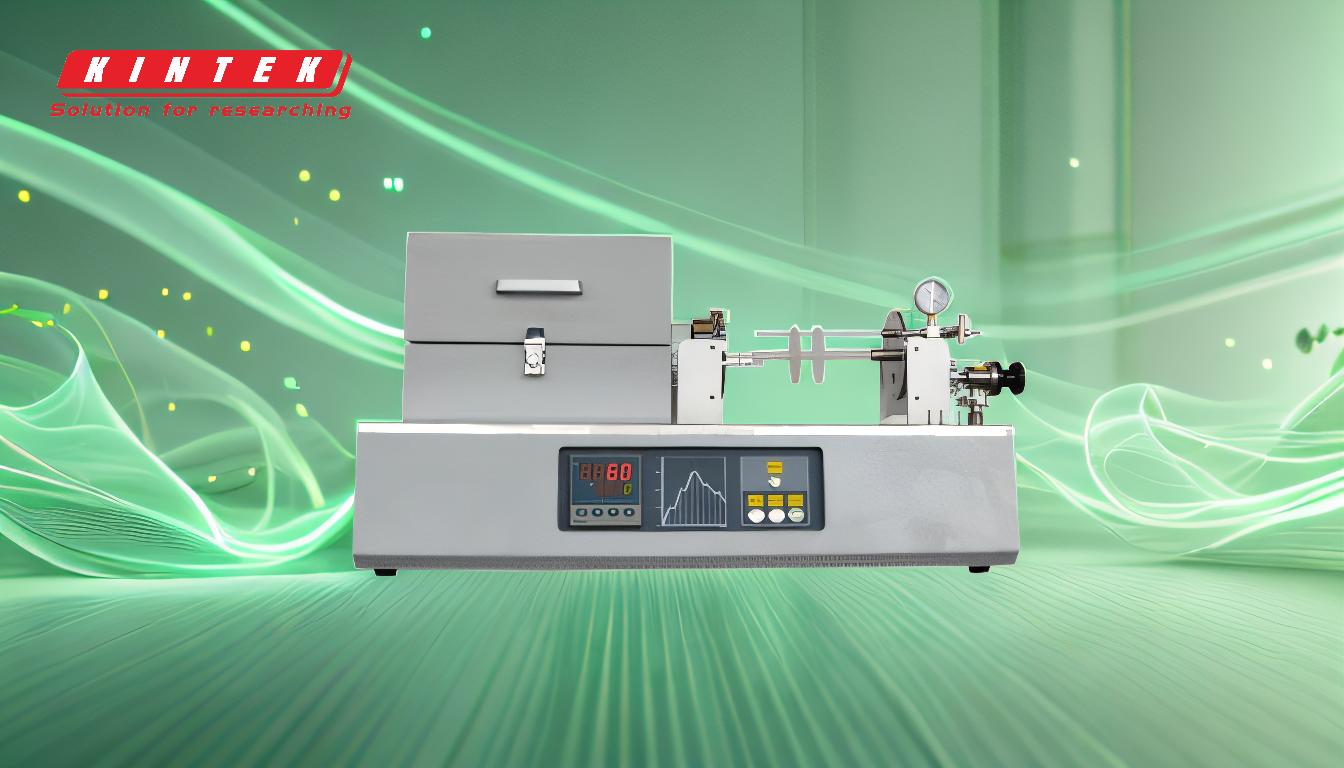
-
Altering Physical and Chemical Properties:
- Heat treatment involves controlled heating and cooling to modify the internal structure of metals. This process can enhance properties like strength, ductility, and hardness, which are crucial for the performance of cast components in demanding environments.
-
Residual Stress Relief:
- Casting processes often introduce residual stresses due to uneven cooling. Heat treatment helps relieve these stresses, reducing the risk of deformation or cracking during use. This is particularly important for components subjected to high loads or cyclic stresses.
-
Porosity Reduction:
- Cast metals may contain microscopic pores or voids, which can weaken the material. Heat treatment can reduce porosity by promoting diffusion and grain boundary movement, resulting in a denser and more uniform structure.
-
Mechanical Property Improvement:
- Heat treatment can significantly enhance mechanical properties such as toughness, wear resistance, and fatigue strength. For example, processes like annealing, quenching, and tempering are tailored to achieve specific property improvements based on the application.
-
Cost-Quality Balance:
- Heat treatment ensures that cast components meet the required quality standards without excessive material waste or additional processing. This balance is essential for industries like aerospace and automotive, where both performance and cost efficiency are critical.
-
Application in Specific Industries:
- Heat treatment is widely used in industries that demand high-performance materials. For instance, aircraft components require excellent strength-to-weight ratios, while automotive parts need durability and wear resistance. Heat treatment makes these properties achievable in cast metals.
-
Versatility Across Metals:
- Heat treatment is applicable to both ferrous (e.g., steel, cast iron) and non-ferrous metals (e.g., aluminum, copper). This versatility allows manufacturers to tailor the properties of a wide range of materials to suit specific applications.
By addressing these key aspects, heat treatment ensures that cast components are not only functional but also reliable and durable, meeting the stringent requirements of modern industrial applications.
Summary Table:
Key Benefits of Heat Treatment in Casting | Description |
---|---|
Alters Physical & Chemical Properties | Enhances strength, ductility, and hardness for demanding environments. |
Relieves Residual Stress | Reduces deformation and cracking risks in high-load applications. |
Reduces Porosity | Promotes denser, more uniform metal structures. |
Improves Mechanical Properties | Boosts toughness, wear resistance, and fatigue strength. |
Balances Cost & Quality | Ensures high-quality components without excessive material waste. |
Wide Industry Applications | Used in aerospace, automotive, and manufacturing for high-performance materials. |
Versatile Across Metals | Applicable to ferrous and non-ferrous metals like steel, aluminum, and copper. |
Optimize your casting process with heat treatment—contact our experts today for tailored solutions!