Hydrogen is used in sintering furnaces primarily due to its unique properties that enhance the sintering process. It acts as an excellent deoxidizer, reducing surface oxides and impurities, which is crucial for achieving high-quality sintered products. Hydrogen's high purity (>99.9995%) ensures a clean and controlled atmosphere, preventing metal oxidation and improving the mechanical properties and surface finish of the sintered parts. Additionally, hydrogen facilitates redox reactions that eliminate impurities, leading to better furnace performance and significant operational savings. However, it is essential to manage hydrogen's potential to cause hydrogen embrittlement in high carbon substances.
Key Points Explained:
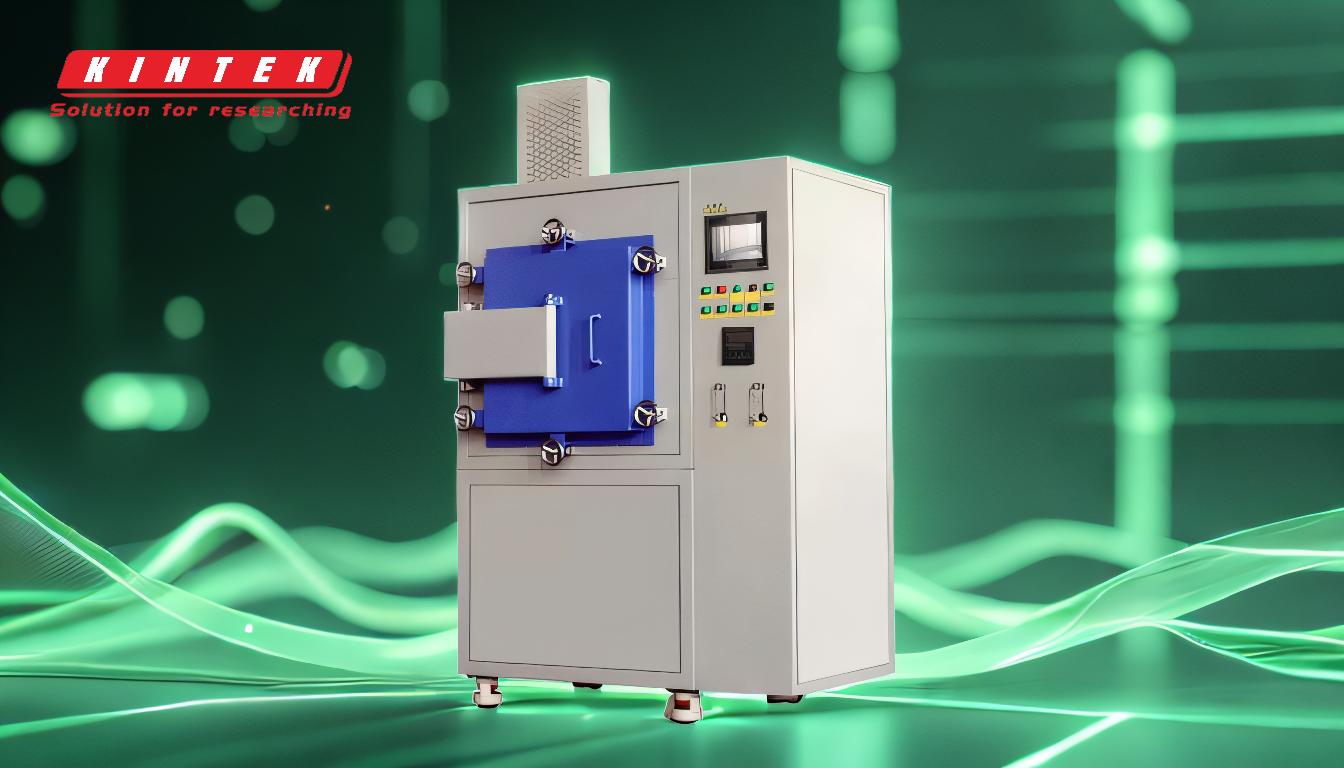
-
Deoxidizing Properties of Hydrogen:
- Hydrogen is an excellent deoxidizer, which means it can effectively reduce surface oxides on metals. This is particularly important in sintering processes where the presence of oxides can degrade the quality of the final product.
- In a dry state, hydrogen can decarburize high carbon substances at extremely high temperatures, forming methane. This helps in reducing impurities and improving the overall quality of the sintered materials.
-
High Purity Atmosphere:
- Commercial hydrogen used in sintering furnaces is highly pure, typically ranging from 98% to 99.9%. This high purity is essential for creating a controlled atmosphere that prevents metal oxidation.
- The high-purity hydrogen atmosphere facilitates redox reactions that eliminate impurities, resulting in parts with superior mechanical qualities and a bright surface finish.
-
Enhanced Furnace Performance:
- The use of hydrogen in sintering furnaces leads to better furnace performance due to its ability to provide a high-quality atmosphere. This atmosphere enhances reducing conditions, which are beneficial for the sintering process.
- Lower dew points in a hydrogen atmosphere further enhance the reducing conditions, leading to better sintering outcomes.
-
Prevention of Metal Oxidation:
- One of the critical roles of hydrogen in sintering furnaces is to prevent metal oxidation. Oxidation can reduce the powders' aggregation ratio, leading to poor-quality sintered products.
- By maintaining a reducing atmosphere, hydrogen ensures that the metal powders remain free from oxides, resulting in better mechanical properties and surface finish.
-
Operational Benefits:
- The use of hydrogen in sintering furnaces leads to substantial savings by reducing the need for additional purification steps and minimizing waste.
- It also reduces air pollution and minimizes risks for personnel, making it a safer and more environmentally friendly option compared to other gases.
-
Applications in Sintering:
- Hydrogen is used in sintering a variety of materials, including tungsten carbide, metal powder components, low carbon steels, and stainless steels. It is also used in the direct reduction of metal ores.
- The controlled hydrogen atmosphere is particularly beneficial for sintering special high-temperature materials, where maintaining a clean and reducing environment is crucial.
-
Potential Challenges:
- While hydrogen offers many benefits, it can cause hydrogen embrittlement in high carbon substances. This is a phenomenon where hydrogen atoms diffuse into the metal lattice, making it brittle and prone to cracking.
- Proper management and control of hydrogen atmosphere are essential to mitigate this risk and ensure the integrity of the sintered products.
In summary, hydrogen is used in sintering furnaces due to its deoxidizing properties, ability to create a high-purity atmosphere, and enhancement of furnace performance. These benefits lead to superior mechanical qualities and surface finish of sintered parts, along with operational savings and environmental advantages. However, careful management is required to avoid potential issues like hydrogen embrittlement.
Summary Table:
Key Benefits of Hydrogen in Sintering | Details |
---|---|
Deoxidizing Properties | Reduces surface oxides and impurities, improving material quality. |
High Purity Atmosphere | Prevents metal oxidation, ensuring superior mechanical properties. |
Enhanced Furnace Performance | Improves reducing conditions for better sintering outcomes. |
Operational Savings | Reduces purification steps, waste, and environmental impact. |
Applications | Used for tungsten carbide, metal powders, low carbon steels, and more. |
Challenges | Risk of hydrogen embrittlement in high carbon substances. |
Learn how hydrogen can optimize your sintering process—contact our experts today!