Ceramics are widely used in dentistry due to their unique combination of biocompatibility, aesthetic appeal, and durability. They closely mimic the natural appearance of teeth, making them ideal for restorative and cosmetic dental procedures. Additionally, ceramics are chemically inert, resistant to wear, and can be precisely shaped to fit dental structures. Their ability to bond with dental tissues and withstand the oral environment further enhances their suitability for dental applications. This makes ceramics a preferred material for crowns, veneers, inlays, onlays, and even dental implants.
Key Points Explained:
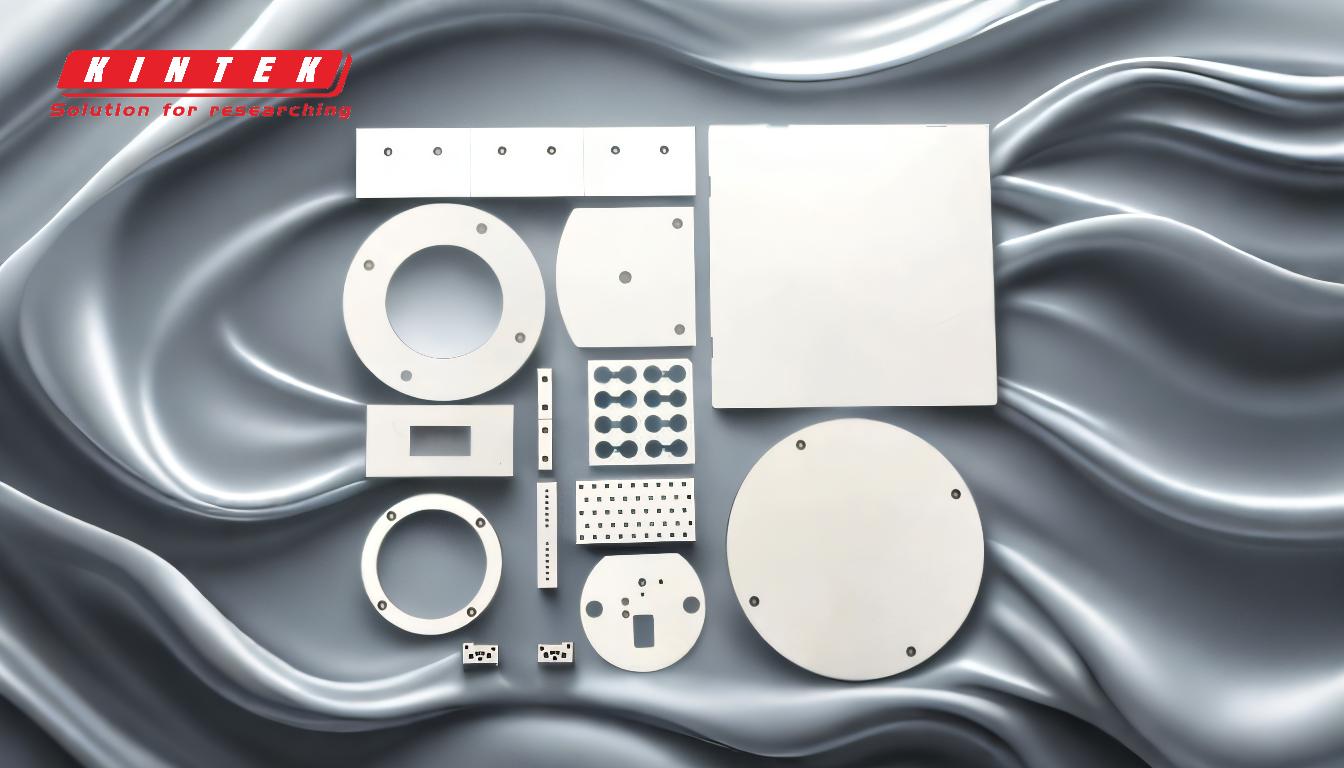
-
Aesthetic Appeal:
- Ceramics are highly valued in dentistry for their ability to replicate the natural appearance of teeth. They can be color-matched to the patient's existing teeth, ensuring a seamless and aesthetically pleasing result.
- The translucency and light-reflecting properties of ceramics closely resemble those of natural tooth enamel, making them ideal for front teeth restorations where appearance is critical.
-
Biocompatibility:
- Ceramics are biocompatible, meaning they are well-tolerated by the human body and do not cause adverse reactions. This is crucial for dental materials that remain in the mouth for extended periods.
- Unlike some metals, ceramics do not corrode or release harmful ions, reducing the risk of allergic reactions or tissue irritation.
-
Durability and Strength:
- Modern dental ceramics are engineered to be highly durable and resistant to wear. They can withstand the forces of chewing and biting, making them suitable for long-term use.
- Advanced ceramics, such as zirconia, offer exceptional strength and are often used for posterior teeth restorations where higher mechanical loads are expected.
-
Chemical Stability:
- Ceramics are chemically inert, meaning they do not react with saliva, food, or other substances in the oral environment. This ensures the longevity of the restoration and prevents degradation over time.
- Their resistance to staining and discoloration helps maintain the aesthetic quality of dental restorations for years.
-
Precision and Customization:
- Ceramics can be precisely shaped and customized to fit the unique contours of a patient's teeth. This ensures a comfortable fit and optimal function.
- CAD/CAM (Computer-Aided Design/Computer-Aided Manufacturing) technology allows for highly accurate fabrication of ceramic restorations, further enhancing their fit and performance.
-
Bonding with Dental Tissues:
- Ceramics can bond effectively with dental tissues, particularly when used with modern adhesive techniques. This creates a strong and stable interface between the restoration and the natural tooth structure.
- The bonding process helps distribute forces evenly across the restoration, reducing the risk of fractures or failures.
-
Versatility in Applications:
- Ceramics are used in a wide range of dental applications, including crowns, veneers, inlays, onlays, and bridges. They are also increasingly being used in dental implants due to their biocompatibility and aesthetic properties.
- Their versatility allows dentists to address various dental issues, from minor cosmetic corrections to major restorative procedures.
-
Advancements in Ceramic Technology:
- Ongoing research and development have led to the creation of advanced ceramic materials, such as lithium disilicate and zirconia, which offer improved strength, durability, and aesthetic properties.
- These advancements have expanded the use of ceramics in dentistry, making them a reliable and preferred choice for both patients and dental professionals.
In summary, ceramics are a cornerstone of modern dentistry due to their exceptional combination of aesthetics, biocompatibility, durability, and versatility. Their ability to closely mimic natural teeth, coupled with advancements in material science, ensures that they remain a top choice for dental restorations and cosmetic procedures.
Summary Table:
Key Benefits of Ceramics in Dentistry | Details |
---|---|
Aesthetic Appeal | Mimics natural teeth, color-matching, and light-reflecting properties. |
Biocompatibility | Non-reactive, hypoallergenic, and safe for long-term use. |
Durability & Strength | Resistant to wear, suitable for chewing forces, and ideal for posterior teeth. |
Chemical Stability | Resists staining, discoloration, and degradation in the oral environment. |
Precision & Customization | CAD/CAM technology ensures accurate fit and optimal function. |
Bonding with Dental Tissues | Strong adhesion with natural tooth structure, reducing fracture risks. |
Versatility | Used in crowns, veneers, inlays, onlays, bridges, and implants. |
Advancements | Zirconia and lithium disilicate offer enhanced strength and aesthetics. |
Learn more about how ceramic dental solutions can transform your smile—contact our experts today!