Chemical Vapor Deposition (CVD) is performed at low pressures to optimize the deposition process, enhance film quality, and ensure uniformity. Low-pressure environments facilitate better control over chemical reactions, improve mass transfer, and reduce contamination risks. Additionally, low pressures enable shorter free path lengths for reactive species, promoting uniform nucleation and high deposition rates. This controlled environment ensures the formation of stable, high-quality thin films, which are critical for applications in semiconductor manufacturing, coatings, and advanced materials. The choice of low pressure is a balance between reaction kinetics, diffusion, and film quality.
Key Points Explained:
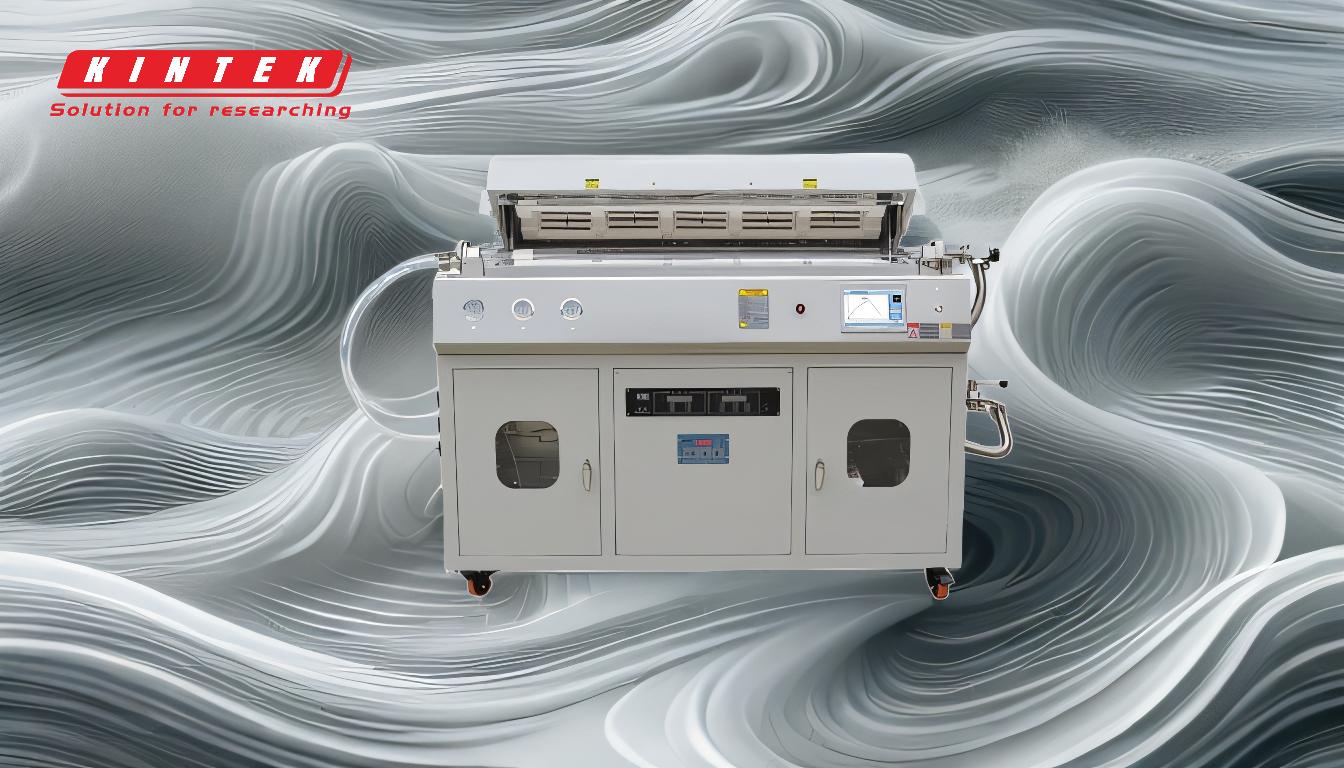
-
Enhanced Control Over Chemical Reactions:
- At low pressures, the reaction kinetics of precursor gases are more predictable and controllable. This allows for precise tuning of the deposition process, ensuring that the desired chemical reactions occur efficiently.
- Low-pressure environments reduce the likelihood of unwanted side reactions, which can compromise film quality or introduce impurities.
-
Improved Mass Transfer:
- Low pressures increase the mean free path of gas molecules, allowing them to travel longer distances without collisions. This enhances the diffusion of reactive species to the substrate surface, ensuring uniform deposition.
- In contrast, high pressures can limit mass transfer by reducing the mean free path, leading to non-uniform film growth.
-
Uniform Nucleation and Film Growth:
- Low-pressure conditions promote uniform nucleation of solid particles in the gas phase. This is due to the shorter free path length of reactive radicals, which ensures even distribution and adherence to the substrate.
- High pressures can lead to uneven nucleation, resulting in defects or poor film quality.
-
High Deposition Rates and Stability:
- Low-pressure CVD (LPCVD) and plasma-enhanced CVD (PECVD) processes are known for their high deposition rates, which are critical for industrial applications.
- Films deposited at low pressures tend to be more stable and less prone to delamination or degradation compared to those deposited at higher pressures.
-
Reduced Contamination:
- Low-pressure environments minimize the presence of contaminants, such as dust or unwanted gases, which can interfere with the deposition process or degrade film quality.
- High-pressure environments are more susceptible to contamination, which can lead to unstable or defective films.
-
Thermal Decomposition and Reaction Efficiency:
- CVD relies on the thermal decomposition of precursor gases to form thin films. Low pressures enhance the efficiency of this process by ensuring that the precursor gases decompose uniformly and react effectively with the substrate.
- At higher pressures, thermal decomposition may become less efficient, leading to incomplete reactions or uneven film growth.
-
Compatibility with Advanced Techniques:
- Low-pressure CVD is compatible with advanced deposition techniques, such as plasma-assisted CVD and laser-assisted CVD, which require precise control over pressure and temperature.
- These techniques leverage low-pressure environments to achieve high-quality films with specific properties, such as improved adhesion, density, or conductivity.
-
Application-Specific Advantages:
- In semiconductor manufacturing, low-pressure CVD is essential for depositing thin films with precise thickness and uniformity, which are critical for device performance.
- For coatings and advanced materials, low-pressure CVD ensures the formation of dense, defect-free films with tailored properties, such as hardness, corrosion resistance, or optical transparency.
By performing CVD at low pressures, manufacturers can achieve superior control over the deposition process, resulting in high-quality, uniform, and stable thin films. This approach is particularly advantageous for applications requiring precision, reliability, and performance.
Summary Table:
Key Benefit | Explanation |
---|---|
Enhanced Control Over Reactions | Predictable and controllable reaction kinetics, reducing unwanted side reactions. |
Improved Mass Transfer | Increased mean free path ensures uniform diffusion of reactive species. |
Uniform Nucleation & Film Growth | Shorter free path lengths promote even distribution and adherence to substrates. |
High Deposition Rates & Stability | Low-pressure CVD ensures stable, high-quality films with minimal defects. |
Reduced Contamination | Minimizes contaminants, ensuring cleaner deposition environments. |
Thermal Decomposition Efficiency | Enhances precursor gas decomposition for uniform and complete reactions. |
Compatibility with Advanced Methods | Works seamlessly with plasma-assisted and laser-assisted CVD techniques. |
Application-Specific Advantages | Ideal for semiconductor manufacturing, coatings, and advanced materials. |
Ready to optimize your CVD process? Contact our experts today to learn how low-pressure CVD can benefit your applications!