Debinding is a critical step in manufacturing processes such as powder metallurgy, technical ceramics, and 3D printing. It involves the removal of binding materials or carrier substances used during the initial shaping or compaction of parts. These binders, while essential for forming the part, become contaminants during sintering or final processing. If not removed, they can lead to defects like blistering, porosity, warping, or cracking in the final product. Debinding ensures the part's structural integrity, prevents furnace contamination, and optimizes the efficiency of subsequent manufacturing stages. The process can be performed chemically or thermally, with factors like part geometry and material properties influencing the duration and method.
Key Points Explained:
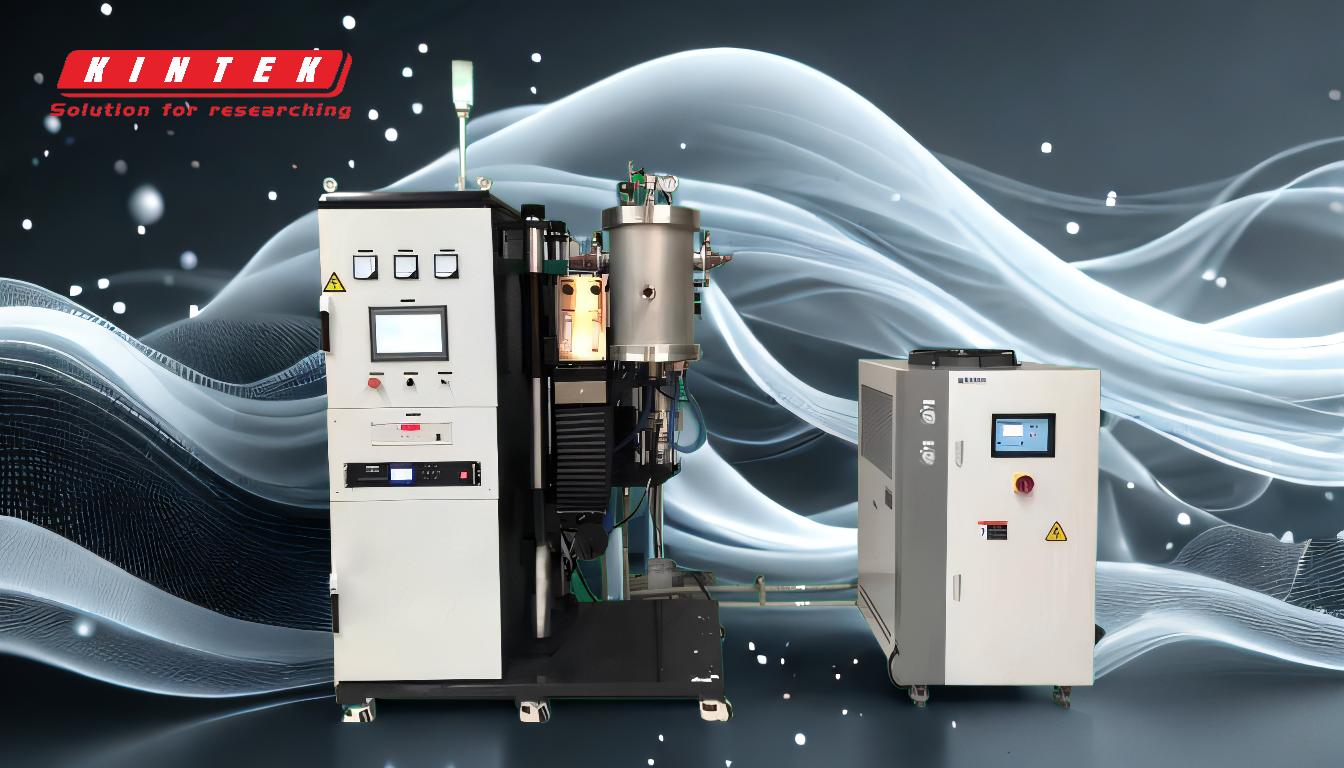
-
Purpose of Debinding
- Removal of Unnecessary Materials: Binders are used during the initial stages of manufacturing (e.g., shaping, compaction, or 3D printing) to hold the material together. However, they serve no purpose in the final product and must be removed to avoid contamination.
- Preparation for Sintering: Debinding prepares the part for sintering by ensuring that no residual binders interfere with the high-temperature process. This is crucial for achieving the desired material properties and structural integrity.
-
Consequences of Inadequate Debinding
- Furnace Contamination: Residual binders can vaporize or decompose during sintering, contaminating the furnace and reducing its efficiency.
- Defects in the Final Product: Incomplete debinding can lead to defects such as blistering, pores, warps, or cracks, which compromise the part's strength and functionality.
- Reduced Process Efficiency: Excess binders can slow down the sintering process and increase energy consumption, making the manufacturing process less efficient.
-
Methods of Debinding
- Thermal Debinding: This involves heating the part in a furnace to decompose or evaporate the binders. The temperature profile, gas atmosphere, and heating rate must be carefully controlled to avoid defects.
- Chemical Debinding: This method uses solvents or chemical baths to dissolve the binders. It is often faster but requires proper handling of chemicals and waste.
- Combination of Methods: Some processes use a combination of thermal and chemical debinding to ensure complete removal of binders, especially for complex geometries.
-
Factors Influencing Debinding
- Part Geometry: Complex shapes or thick sections may require longer debinding times to ensure complete binder removal.
- Binder Composition: The type and amount of binder used affect the debinding method and duration.
- Material Properties: The material being processed (e.g., metal, ceramic, or polymer) determines the appropriate debinding temperature and atmosphere.
-
Importance in Specific Applications
- Powder Metallurgy: Debinding ensures that the part is free of binders before sintering, which is critical for achieving high-density, defect-free components.
- Technical Ceramics: In ceramic manufacturing, debinding removes organic binders and moisture, preventing defects like warping or cracking during sintering.
- 3D Printing: For 3D-printed parts, debinding removes the carrier material, ensuring the part is ready for sintering and achieves the desired mechanical properties.
-
Process Optimization
- Temperature Control: Precise control of the temperature profile is essential to avoid thermal shock or incomplete binder removal.
- Atmosphere Management: The use of inert or reducing atmospheres during thermal debinding prevents oxidation or other unwanted reactions.
- Time Efficiency: Optimizing debinding time ensures thorough binder removal without unnecessarily prolonging the manufacturing process.
-
Economic and Environmental Considerations
- Cost Efficiency: Efficient debinding reduces energy consumption and minimizes waste, lowering production costs.
- Environmental Impact: Proper handling of chemical debinding agents and waste management is essential to minimize environmental harm.
In summary, debinding is a vital step in manufacturing processes that ensures the removal of unnecessary binders, prevents defects, and optimizes the efficiency of subsequent stages. By carefully controlling the debinding process, manufacturers can produce high-quality, defect-free components while minimizing costs and environmental impact.
Summary Table:
Aspect | Details |
---|---|
Purpose | Removes binders to prevent contamination and prepare parts for sintering. |
Consequences of Failure | Defects like blistering, warping, or cracking; furnace contamination. |
Methods | Thermal (heating) or chemical (solvents) debinding, or a combination. |
Key Factors | Part geometry, binder composition, material properties. |
Applications | Powder metallurgy, technical ceramics, 3D printing. |
Optimization | Precise temperature control, atmosphere management, time efficiency. |
Economic & Environmental | Reduces costs, energy use, and environmental impact. |
Need help optimizing your debinding process? Contact our experts today!