High-frequency induction heating is essential for efficient and effective heating of conductive materials due to its ability to generate localized heat quickly and precisely. The high frequency of the alternating current in the induction coil creates a strong magnetic field, which induces eddy currents in the material. These eddy currents generate heat through Joule heating, with the depth of heating penetration inversely proportional to the frequency. Higher frequencies result in shallower penetration, making them ideal for surface heating or heating thin materials. This method is fast, energy-efficient, and compact, making it suitable for applications requiring precision and speed, such as in manufacturing, metallurgy, and electronics.
Key Points Explained:
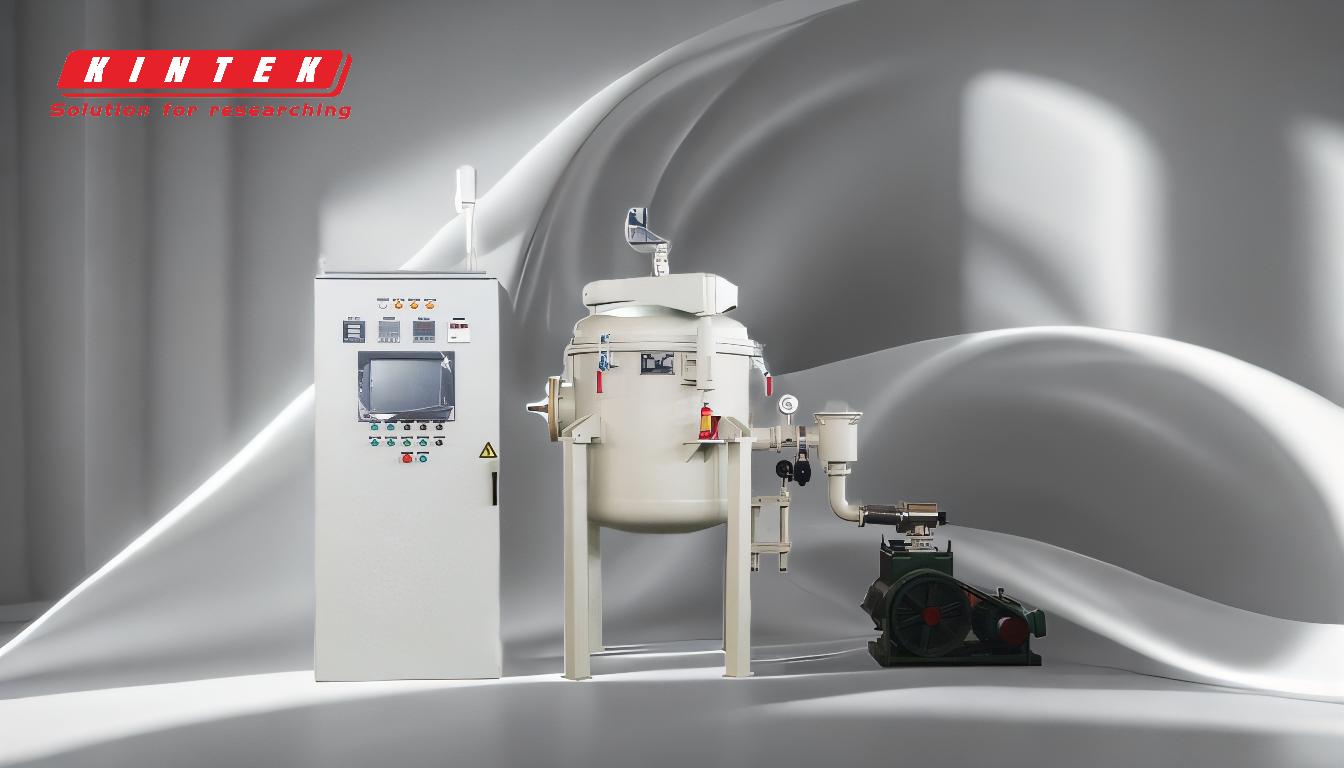
-
Electromagnetic Induction and Eddy Currents:
- Induction heating relies on the principle of electromagnetic induction. When an alternating current flows through a coil, it generates a transient magnetic field. This magnetic field induces eddy currents in nearby conductive materials.
- Eddy currents are circular electric currents that flow within the material, opposing the change in the magnetic field. The resistance of the material to these currents generates heat through Joule heating.
-
Joule Heating and Heat Generation:
- Joule heating, also known as resistive heating, occurs when electric currents pass through a conductor. The resistance of the material converts electrical energy into thermal energy, producing heat.
- In induction heating, the eddy currents generated by the alternating magnetic field flow against the material's resistivity, creating heat. This process is highly efficient as it directly heats the material without requiring physical contact.
-
Frequency and Penetration Depth:
- The frequency of the alternating current determines the depth of heat penetration into the material. Higher frequencies result in shallower penetration, while lower frequencies allow deeper heating.
- The penetration depth (δ) is inversely proportional to the square root of the frequency (f), as described by the formula: δ ∝ 1/√f. This means that high-frequency induction heating is ideal for applications requiring surface heating or heating of thin materials.
-
Advantages of High-Frequency Induction Heating:
- Speed: High-frequency induction heating can rapidly generate heat, making it suitable for processes requiring quick heating cycles.
- Precision: The ability to control the frequency allows for precise control over the heating depth, ensuring that only the desired areas are heated.
- Energy Efficiency: Induction heating is highly efficient as it directly heats the material, minimizing energy loss.
- Compactness: High-frequency induction heating systems are typically smaller and require less space compared to traditional heating methods.
-
Applications of High-Frequency Induction Heating:
- Manufacturing: Used for processes such as hardening, annealing, and brazing, where precise and localized heating is required.
- Metallurgy: Ideal for melting and heat-treating metals, especially in vacuum or controlled atmosphere environments.
- Electronics: Used in the production of electronic components, where high precision and minimal thermal distortion are critical.
-
Transformer Principle in Induction Heating:
- Induction heating operates on the same principle as a transformer. The induction coil acts as the primary winding, and the material to be heated acts as the secondary winding.
- When an alternating current is applied to the primary coil, it generates an alternating magnetic field, which induces an electric current in the secondary (the material). This induced current generates heat through Joule heating.
-
Cooling and System Design:
- The primary coils in induction heating systems are typically cooled by circulating water to prevent overheating and maintain system efficiency.
- The design of the induction heating system, including the coil geometry and frequency selection, is crucial for achieving the desired heating effect.
In summary, high-frequency induction heating is a versatile and efficient method for heating conductive materials. Its ability to generate localized heat quickly and precisely makes it ideal for a wide range of industrial applications. The control over frequency allows for tailored heating depths, ensuring that the process meets specific requirements for speed, precision, and energy efficiency.
Summary Table:
Key Aspect | Details |
---|---|
Principle | Electromagnetic induction and eddy currents generate heat via Joule heating. |
Frequency & Penetration Depth | Higher frequencies = shallower heating; lower frequencies = deeper heating. |
Advantages | Fast, precise, energy-efficient, and compact. |
Applications | Manufacturing, metallurgy, electronics, and more. |
Cooling & Design | Water-cooled coils and tailored system design ensure efficiency. |
Discover how high-frequency induction heating can revolutionize your processes—contact us today for expert guidance!