RF power is used in the sputtering process primarily to enable the deposition of non-conductive or low-conductivity materials, which cannot be effectively sputtered using DC power. The alternating nature of RF power prevents charge buildup on insulating targets, reduces arcing, and ensures a stable and uniform deposition process. RF sputtering operates at lower pressures, improving deposition efficiency and minimizing collisions. It also eliminates issues like "Race Track Erosion" and the disappearing anode effect, leading to better film quality, extended target life, and the ability to deposit a wide range of materials, including insulators, metals, alloys, and composites.
Key Points Explained:
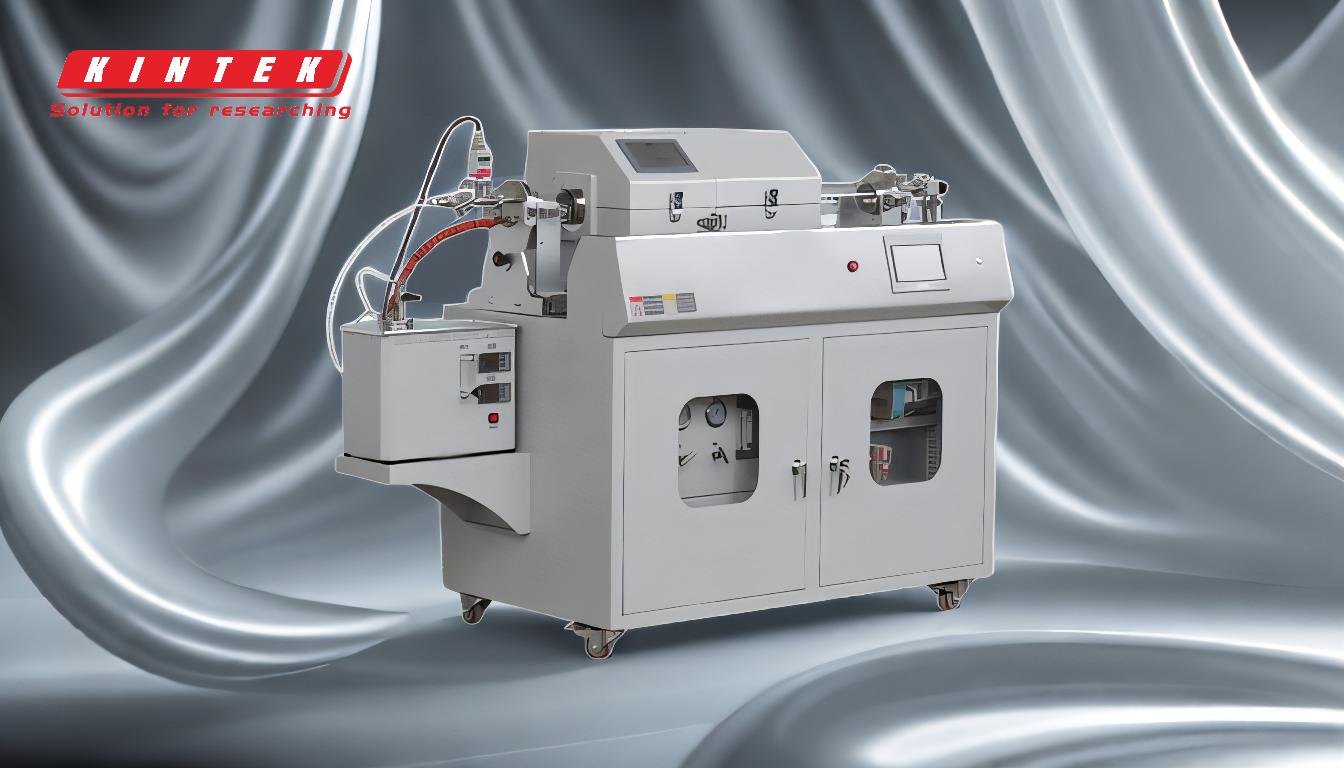
-
Ability to Sputter Non-Conductive Materials:
- RF power is essential for sputtering non-conductive or low-conductivity materials, such as insulators, which cannot be effectively processed using DC power.
- The alternating nature of RF power (typically at 13.56 MHz) prevents charge buildup on the target surface, which is a common issue with DC sputtering for insulating materials.
- This allows for the deposition of a wide variety of materials, including insulators, metals, alloys, and composites.
-
Prevention of Charge Buildup and Arcing:
- RF sputtering uses an alternating electrical field, which changes polarity with the driving RF frequency. This prevents the accumulation of charges on the target surface, a phenomenon that can lead to arcing and plasma instability.
- By avoiding constant negative voltage on the cathode, RF sputtering ensures a more stable process with fewer interruptions and improved film quality.
-
Operation at Lower Pressures:
- RF sputtering can sustain a plasma at lower pressures (1-15 mTorr), reducing ionized gas collisions and increasing the mean free path of target atoms.
- This results in higher deposition efficiency and better control over the sputtering process, as fewer collisions occur between particles in the plasma.
-
Improved Film Uniformity and Quality:
- The RF sputtering process involves both positive and negative cycles, which help maintain a balanced ion bombardment and prevent ion buildup on the target.
- This leads to more uniform film deposition, better step coverage, and higher-quality layers compared to DC sputtering.
-
Reduction of "Race Track Erosion":
- RF sputtering minimizes the "Race Track Erosion" effect, where a specific area of the target is eroded more rapidly due to localized sputtering.
- By involving a larger surface area of the target in the sputtering process, RF sputtering extends the target's lifetime and ensures more consistent material removal.
-
Elimination of Disappearing Anode Effect:
- Unlike DC sputtering, RF sputtering does not suffer from the disappearing anode effect, where the anode becomes coated and ineffective over time.
- This ensures a more stable and continuous sputtering process without the need for frequent maintenance or adjustments.
-
Advantages of RF Diode Sputtering:
- Modern RF diode sputtering technology offers additional benefits, such as improved coating uniformity, flat target erosion, and reduced arcing.
- It does not require magnetic confinement, making it simpler and more efficient for certain applications.
-
Versatility in Material Deposition:
- RF sputtering is capable of depositing a wide range of materials, including insulators, metals, alloys, and composites, making it a versatile technique for various industrial and research applications.
-
Enhanced Process Stability:
- The use of RF power reduces arcing, charge buildup, and other instabilities, leading to a more reliable and repeatable sputtering process.
- This is particularly important for applications requiring high precision and consistency, such as semiconductor manufacturing or optical coatings.
-
Higher Efficiency and Lower Operating Costs:
- RF sputtering operates more efficiently at lower pressures, reducing the energy required to sustain the plasma and minimizing material waste.
- The extended target life and reduced maintenance needs further contribute to lower operating costs over time.
In summary, RF power is a critical component in sputtering processes, especially for non-conductive materials. Its ability to prevent charge buildup, operate at lower pressures, and improve film quality makes it a superior choice over DC sputtering for many applications. The advancements in RF diode sputtering technology further enhance its performance, making it a versatile and efficient method for material deposition.
Summary Table:
Key Feature | Description |
---|---|
Sputters Non-Conductive Materials | Enables deposition of insulators, metals, alloys, and composites. |
Prevents Charge Buildup & Arcing | Alternating RF field avoids charge accumulation, ensuring stable deposition. |
Operates at Lower Pressures | Reduces collisions, improves deposition efficiency, and enhances control. |
Improves Film Uniformity | Balanced ion bombardment leads to higher-quality, uniform layers. |
Reduces Race Track Erosion | Extends target life by minimizing localized sputtering. |
Eliminates Disappearing Anode | Ensures continuous sputtering without frequent maintenance. |
Versatile Material Deposition | Suitable for insulators, metals, alloys, and composites. |
Enhanced Process Stability | Reduces arcing and instabilities, ideal for precision applications. |
Higher Efficiency & Lower Costs | Operates efficiently at lower pressures, reducing energy and maintenance costs. |
Ready to enhance your sputtering process? Contact our experts today to learn more about RF power solutions!