Sintering is a critical process in materials science, where particles are fused together to form a solid structure. The presence of a liquid phase during sintering, known as liquid-phase sintering, significantly enhances the process by promoting particle rearrangement, improving densification, and facilitating the removal of impurities. This method is particularly advantageous for materials with complex compositions, as the liquid phase acts as a medium for faster material transport and better bonding. The efficiency of liquid-phase sintering depends on factors such as temperature, pressure, particle size, and the amount of liquid phase, which must be carefully controlled to achieve optimal results.
Key Points Explained:
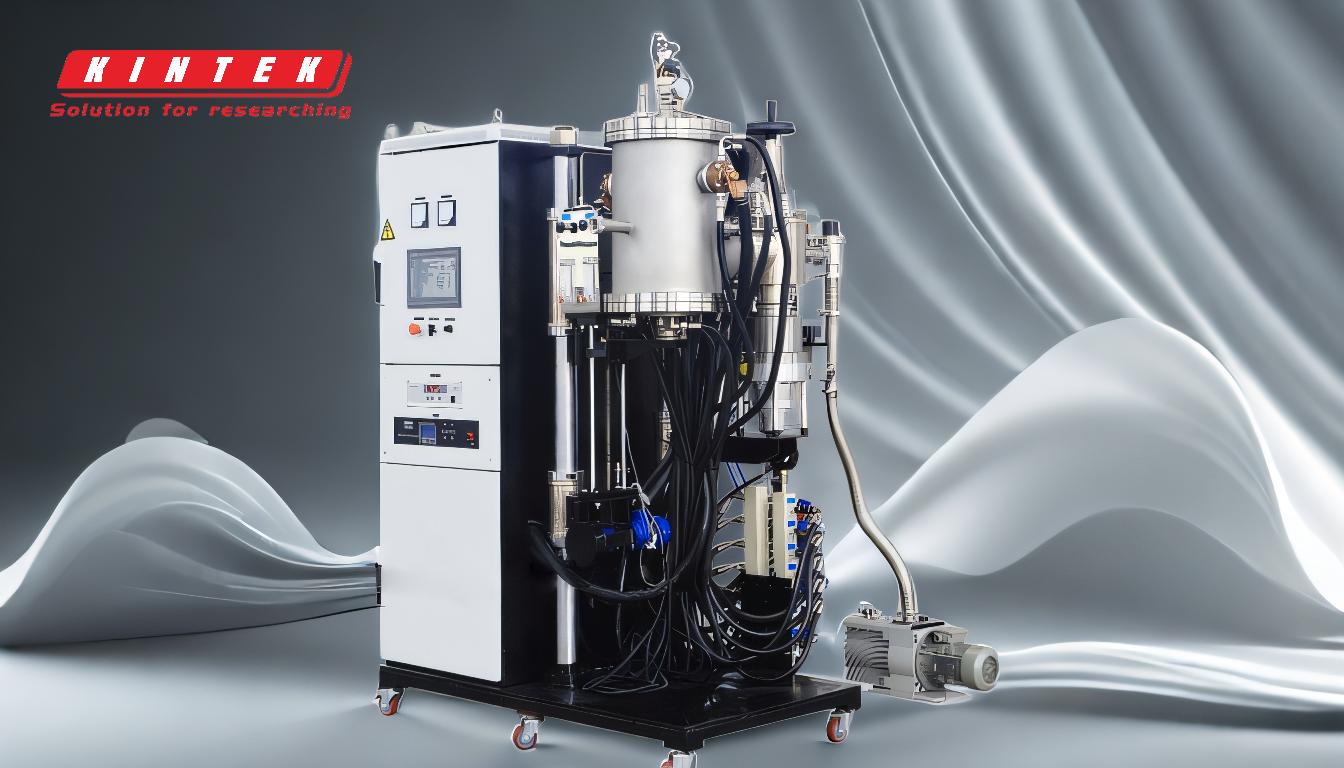
-
Particle Rearrangement and Neck Formation:
- The liquid phase spreads between solid particles, reducing friction and allowing particles to move more freely. This rearrangement leads to better packing and closer contact between particles.
- The liquid phase also enhances the formation of "necks" between particles, which are critical for bonding and densification. This occurs because the liquid phase provides a medium for faster diffusion of atoms, promoting the growth of these necks.
-
Enhanced Densification:
- The liquid phase accelerates the densification process by filling pores and gaps between particles. This reduces porosity and increases the overall density of the sintered material.
- Capillary forces exerted by the liquid phase pull particles together, further aiding in densification.
-
Removal of Impurities:
- The liquid phase can dissolve impurities or carry them away from the particle surfaces, leading to a cleaner and more homogeneous final product. This is particularly important for materials that require high purity.
-
Facilitation of Complex Compositions:
- Liquid-phase sintering is especially beneficial for materials with complex compositions or multi-component systems. The liquid phase acts as a solvent, enabling the uniform distribution of different components and ensuring consistent properties throughout the material.
-
Control of Sintering Parameters:
- Temperature: Higher temperatures increase the mobility of atoms and the fluidity of the liquid phase, enhancing sintering. However, excessive temperatures can lead to unwanted phase changes or excessive liquid formation.
- Pressure: Applied pressure can further enhance particle rearrangement and eliminate porosity, especially in systems where the liquid phase alone may not achieve full densification.
- Particle Size: Smaller particles have a higher surface area-to-volume ratio, which promotes faster sintering. The liquid phase aids in bridging these small particles, leading to better densification.
- Amount of Liquid Phase: The volume of the liquid phase must be carefully controlled. Too little liquid may not provide sufficient benefits, while too much can lead to deformation or loss of structural integrity.
-
Advantages Over Solid-State Sintering:
- Liquid-phase sintering is generally faster than solid-state sintering due to the increased atomic mobility provided by the liquid phase.
- It allows for the sintering of materials that would otherwise be difficult to densify using solid-state methods, such as ceramics or composites with high melting points.
-
Applications and Limitations:
- Liquid-phase sintering is widely used in the production of cemented carbides, ceramics, and certain metal alloys. It is particularly useful for creating materials with high strength, wear resistance, and thermal stability.
- The main limitation is the need for precise control over the liquid phase volume and composition to avoid defects such as warping, cracking, or inhomogeneous properties.
In conclusion, liquid-phase sintering offers significant advantages over traditional solid-state sintering by improving particle rearrangement, densification, and impurity removal. However, achieving optimal results requires careful control of process parameters such as temperature, pressure, and the amount of liquid phase. This method is particularly valuable for producing high-performance materials with complex compositions and tailored properties.
Summary Table:
Key Aspect | Description |
---|---|
Particle Rearrangement | Liquid phase reduces friction, enabling better particle packing and neck formation. |
Enhanced Densification | Fills pores and gaps, increasing material density through capillary forces. |
Impurity Removal | Dissolves or carries away impurities, ensuring a cleaner final product. |
Complex Compositions | Acts as a solvent for uniform distribution of multi-component systems. |
Control Parameters | Temperature, pressure, particle size, and liquid phase volume must be optimized. |
Advantages Over Solid-State | Faster sintering, suitable for high-melting-point materials like ceramics. |
Applications | Used in cemented carbides, ceramics, and metal alloys for strength and durability. |
Limitations | Requires precise control to avoid defects like warping or inhomogeneous properties. |
Interested in optimizing your sintering process? Contact our experts today for tailored solutions!