Sintering is a versatile and widely used manufacturing process that offers numerous advantages, particularly for materials with high melting points or complex compositions. It involves heating powdered materials to a temperature below their melting point, causing the particles to bond and form a solid structure. This process is essential in various industries, including ceramics, metals, and plastics, due to its ability to produce dense, strong, and complex-shaped components. Sintering is particularly beneficial for materials like refractory metals (e.g., tungsten and molybdenum) and advanced ceramics, which are difficult to process through traditional melting and casting methods. Additionally, modern techniques like 3D printing and isostatic pressing have expanded the applications of sintering, making it a cost-effective and efficient manufacturing solution.
Key Points Explained:
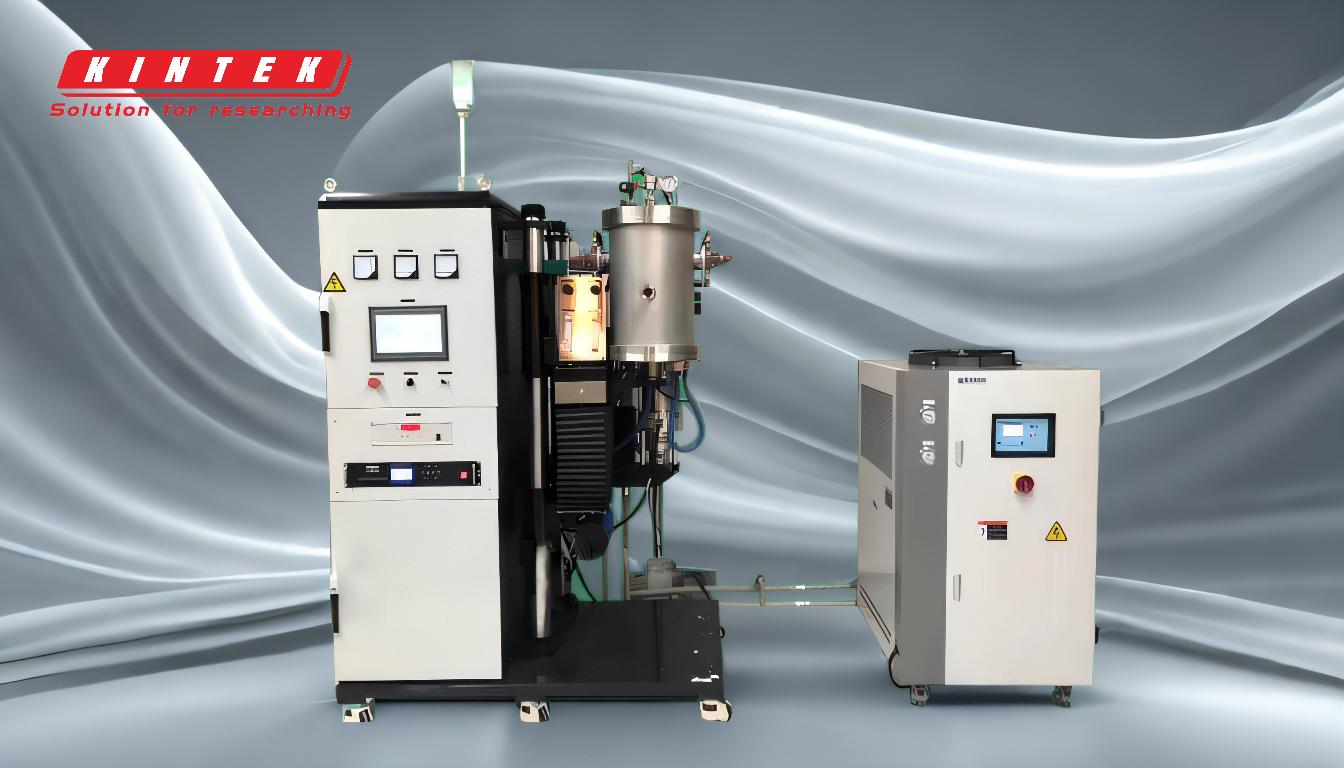
-
Production of Dense and Strong Materials:
- Sintering enables the creation of dense and strong materials from powdered forms. This is particularly useful for materials with high melting points, such as refractory metals (tungsten, molybdenum) and advanced ceramics, which are challenging to process using traditional melting and casting methods.
- The process involves heating the powder to a temperature below its melting point, allowing particles to bond and form a solid structure. This results in materials with improved mechanical properties, such as higher strength and durability.
-
Versatility in Material Selection:
- Sintering is highly versatile and can be applied to a wide range of materials, including metals, ceramics, plastics, and composites. This flexibility makes it suitable for various industries, from aerospace to biomedical applications.
- The ability to tailor material compositions during the sintering process allows for the creation of custom materials with specific properties, such as enhanced thermal or electrical conductivity.
-
Creation of Complex Shapes and Designs:
- One of the key advantages of sintering is its ability to produce components with complex shapes and intricate designs. This reduces the need for additional machining, saving time and costs.
- Modern methods like 3D printing, isostatic pressing, and tapecasting are often used to form "green bodies" (pre-sintered shapes) that are then sintered to achieve the final product.
-
Cost-Effectiveness and Efficiency:
- Sintering is a cost-effective manufacturing process, as it minimizes material waste and reduces the need for extensive post-processing. The ability to produce near-net-shape components further enhances its efficiency.
- The process also allows for faster startups and fewer interruptions, leading to increased productivity and lower operational costs.
-
Applications in Additive Manufacturing:
- Sintering plays a crucial role in additive manufacturing, particularly with 3D metal printers. It enables the creation of custom metal forms and complex geometries that would be difficult or impossible to achieve with traditional methods.
- The relatively low sintering temperature compared to melting makes it suitable for combining metals with high melting points, such as tungsten and molybdenum.
-
Role of Sintering Furnaces:
- A sintering furnace is a critical component in the sintering process. It provides the controlled environment needed to achieve the desired material properties.
- For example, a hot press sintering furnace uses high temperature and pressure in a vacuum environment to fuse ceramic powders into solid materials. This process involves loading the powder, evacuating the furnace, heating, applying pressure, and cooling, ensuring the production of high-quality sintered products.
-
Improved Mechanical and Functional Properties:
- Sintered materials often exhibit enhanced mechanical properties, such as increased hardness, wear resistance, and thermal stability. These improvements make sintered components ideal for demanding applications in industries like automotive, aerospace, and energy.
- The process also allows for the creation of porous materials, which are useful in applications like filters and catalysts.
In summary, sintering is a vital manufacturing process due to its ability to produce high-quality, complex-shaped components from a wide range of materials. Its cost-effectiveness, versatility, and compatibility with modern manufacturing techniques make it an indispensable tool in various industries. The use of specialized equipment like sintering furnaces further enhances the precision and efficiency of the process, ensuring consistent and reliable results.
Summary Table:
Key Benefits of Sintering | Details |
---|---|
Dense and Strong Materials | Creates durable materials from powders, ideal for high-melting-point metals. |
Versatility in Materials | Applicable to metals, ceramics, plastics, and composites. |
Complex Shapes and Designs | Reduces machining needs, saving time and costs. |
Cost-Effectiveness | Minimizes waste and post-processing, enhancing efficiency. |
Additive Manufacturing | Enables custom metal forms and complex geometries via 3D printing. |
Improved Mechanical Properties | Enhances hardness, wear resistance, and thermal stability. |
Learn how sintering can optimize your manufacturing process—contact us today!