Sintering is a critical process used to process ceramic materials because it transforms powdered ceramic materials into dense, strong, and durable polycrystalline structures without melting them. This process involves heating the ceramic powder at high temperatures below its melting point, which facilitates particle bonding, reduces porosity, and enhances material density. Sintering is essential for achieving the desired mechanical, thermal, and electrical properties of ceramics, making it indispensable in industries requiring advanced ceramic materials with specific performance characteristics. The process is cost-effective, versatile, and allows for precise control over the final product's microstructure and properties.
Key Points Explained:
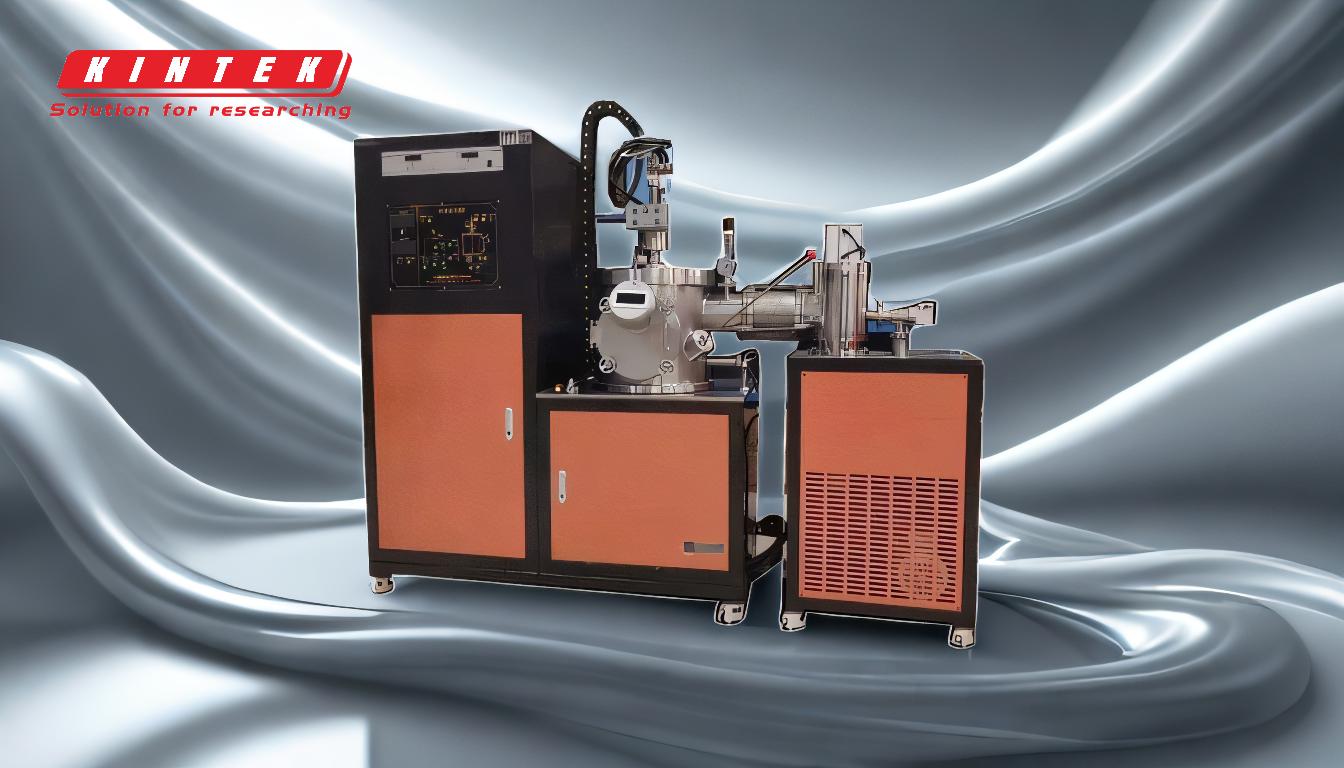
-
Densification and Strength Enhancement:
- Sintering transforms loose ceramic powder into a dense, cohesive structure by bonding particles together at high temperatures.
- The process reduces porosity and increases density, resulting in a material with improved mechanical strength and durability.
- This is crucial for applications where ceramics must withstand high stress, wear, or thermal loads.
-
Microstructure Control:
- Sintering allows for the formation of a uniform polycrystalline microstructure, which is essential for achieving consistent material properties.
- By controlling sintering parameters like temperature, time, and atmosphere, manufacturers can tailor the grain size, density, and porosity to meet specific application requirements.
-
Cost-Effectiveness and Efficiency:
- Sintering is a cost-effective method because it does not require melting the material, which saves energy and reduces production costs.
- The process is highly efficient and scalable, making it suitable for mass production of ceramic components.
-
Versatility Across Industries:
- Sintered ceramics are used in a wide range of industries, including electronics, aerospace, automotive, and medical devices, due to their excellent thermal, electrical, and mechanical properties.
- Examples include ceramic insulators, cutting tools, bearings, and biomedical implants.
-
Improved Functional Properties:
- Sintering enhances the functional properties of ceramics, such as thermal conductivity, electrical insulation, and chemical resistance.
- These properties make sintered ceramics ideal for high-performance applications in harsh environments.
-
Shrinkage and Dimensional Accuracy:
- During sintering, the material undergoes controlled shrinkage, which is accounted for during the design and compaction stages.
- This ensures that the final product has precise dimensions and meets tight tolerances required for advanced applications.
-
Controlled Atmosphere and Cooling Rates:
- Sintering is performed in controlled atmospheres to prevent oxidation or contamination, ensuring the purity and integrity of the ceramic material.
- Adjusting the cooling rate allows for fine-tuning of material properties, such as hardness and toughness.
-
Transformation of Powder to Solid Body:
- Sintering converts powdered ceramic materials into a solid, dense body with specific properties, making it a fundamental step in ceramic manufacturing.
- This transformation is achieved through diffusion and mass transfer mechanisms, which eliminate pores and create a strong, cohesive structure.
In summary, sintering is indispensable for processing ceramic materials because it provides a cost-effective, efficient, and versatile method to produce dense, strong, and high-performance ceramics with tailored properties. Its ability to control microstructure, enhance functional properties, and ensure dimensional accuracy makes it a cornerstone of advanced ceramic manufacturing.
Summary Table:
Key Aspect | Details |
---|---|
Densification & Strength | Bonds particles, reduces porosity, and enhances mechanical strength. |
Microstructure Control | Tailors grain size, density, and porosity for consistent properties. |
Cost-Effectiveness | Energy-efficient and scalable for mass production. |
Versatility | Used in electronics, aerospace, automotive, and medical industries. |
Functional Properties | Improves thermal conductivity, electrical insulation, and chemical resistance. |
Dimensional Accuracy | Ensures precise dimensions and tight tolerances. |
Controlled Atmosphere | Prevents oxidation and contamination for material integrity. |
Powder to Solid Body | Transforms powdered ceramics into dense, cohesive structures. |
Ready to enhance your ceramic manufacturing process? Contact us today for expert solutions!