The pouring temperature of molten metal is intentionally set higher than its melting temperature to account for heat loss during the transition from melting to pouring. This ensures that the metal remains in a fully molten state, preventing premature solidification and defects in the final casting. The higher temperature compensates for cooling that occurs during handling, transportation, and pouring, ensuring proper flow and filling of the mold. Additionally, it helps avoid the formation of cooling fins or other imperfections that could arise if the metal were to solidify too early. This practice is critical for achieving high-quality castings with minimal defects.
Key Points Explained:
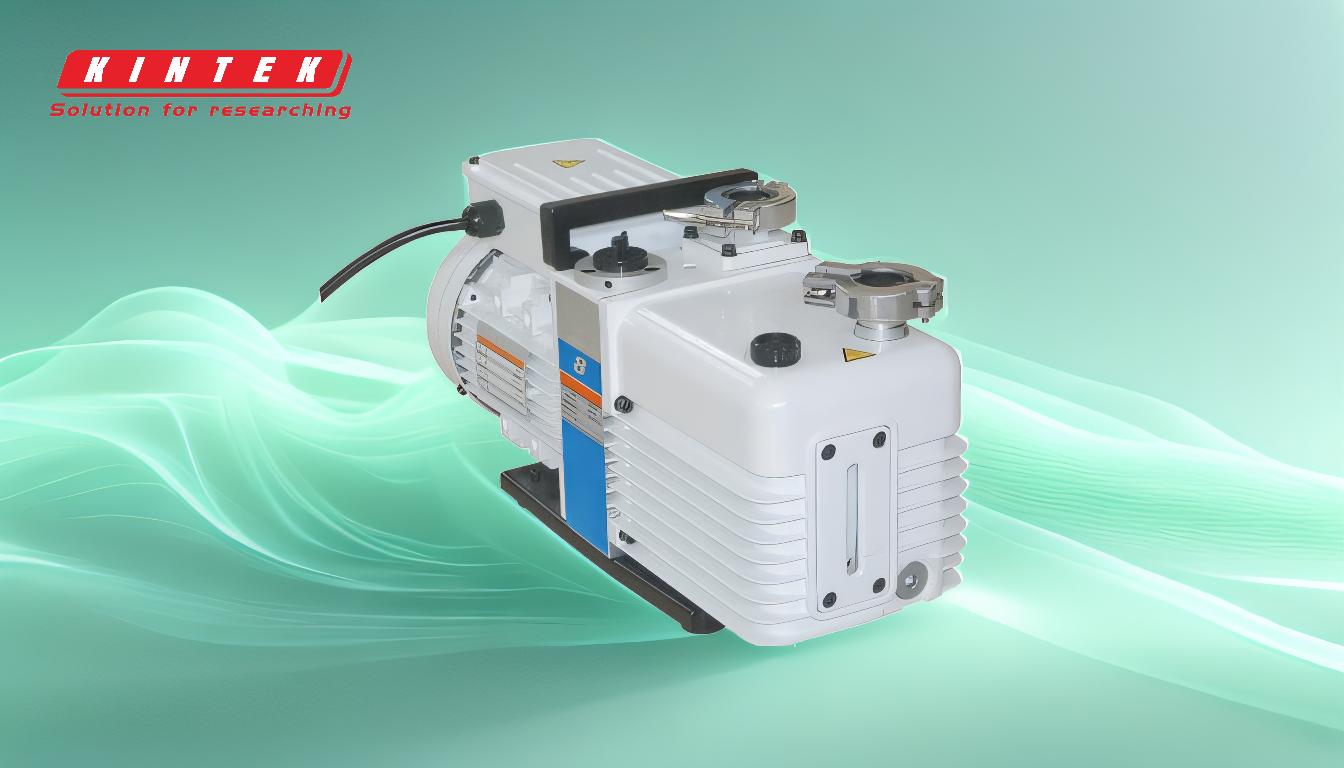
-
Heat Loss During Transition:
- When molten metal is transferred from the melting furnace to the mold, it loses heat due to exposure to the surrounding environment. This heat loss can cause the metal to cool below its melting point, leading to partial solidification.
- To counteract this, the metal is heated to a temperature significantly higher than its melting point before pouring. This ensures that the metal remains fully molten throughout the process.
-
Preventing Premature Solidification:
- If the metal cools too quickly, it may begin to solidify before completely filling the mold. This can result in incomplete castings, surface defects, or internal voids.
- By maintaining a higher pouring temperature, the metal retains its fluidity, allowing it to flow smoothly and fill even intricate mold details.
-
Avoiding Cooling Fins and Defects:
- Cooling fins, as mentioned in the reference, are thin projections of solidified metal that form when the metal cools unevenly or too quickly. These fins require additional post-processing to remove, increasing production time and costs.
- A higher pouring temperature minimizes the risk of such defects by ensuring uniform cooling and solidification within the mold.
-
Compensating for Handling and Pouring Delays:
- The time taken to transport and pour the molten metal can vary depending on the casting process and equipment used. During this time, the metal continues to lose heat.
- The elevated pouring temperature acts as a buffer, providing sufficient thermal energy to maintain the metal's molten state until it is fully poured into the mold.
-
Ensuring Proper Mold Filling:
- A higher pouring temperature improves the metal's ability to flow into all parts of the mold, including thin sections and complex geometries. This is especially important for achieving high-quality castings with precise dimensions and smooth surfaces.
- Without this temperature margin, the metal might solidify prematurely, leading to incomplete filling and defects.
-
Optimizing Casting Quality:
- The practice of pouring at a higher temperature is a key factor in ensuring the overall quality of the casting. It reduces the likelihood of defects such as cold shuts, misruns, and porosity, which can compromise the structural integrity and appearance of the final product.
- By carefully controlling the pouring temperature, manufacturers can produce castings that meet stringent quality standards and perform reliably in their intended applications.
In summary, the higher pouring temperature of molten metal is a deliberate and essential practice in casting processes. It compensates for heat loss, prevents premature solidification, and ensures the metal flows properly into the mold, resulting in high-quality castings with minimal defects.
Summary Table:
Key Reason | Explanation |
---|---|
Heat Loss During Transition | Compensates for heat loss during handling, transportation, and pouring. |
Preventing Premature Solidification | Ensures metal remains fully molten, preventing incomplete castings and defects. |
Avoiding Cooling Fins and Defects | Minimizes imperfections like cooling fins by ensuring uniform cooling. |
Compensating for Delays | Provides a thermal buffer for handling and pouring delays. |
Ensuring Proper Mold Filling | Improves flow into complex mold geometries for precise and smooth castings. |
Optimizing Casting Quality | Reduces defects like cold shuts, misruns, and porosity for reliable performance. |
Need expert advice on achieving high-quality castings? Contact us today to optimize your pouring process!