Thin-film deposition is typically performed in a vacuum to ensure high-quality, pure, and adherent films. A vacuum environment reduces the presence of unwanted substances like oxygen, nitrogen, and moisture, which can contaminate the film, weaken its adhesion, or disrupt the deposition process. Additionally, a vacuum lengthens the mean free path of particles, allowing film particles to travel unimpeded from the source to the substrate, resulting in smoother and more uniform films. The controlled environment also enables precise control over gas composition, mass flow, and plasma conditions, which are critical for repeatable and high-performance thin-film deposition processes.
Key Points Explained:
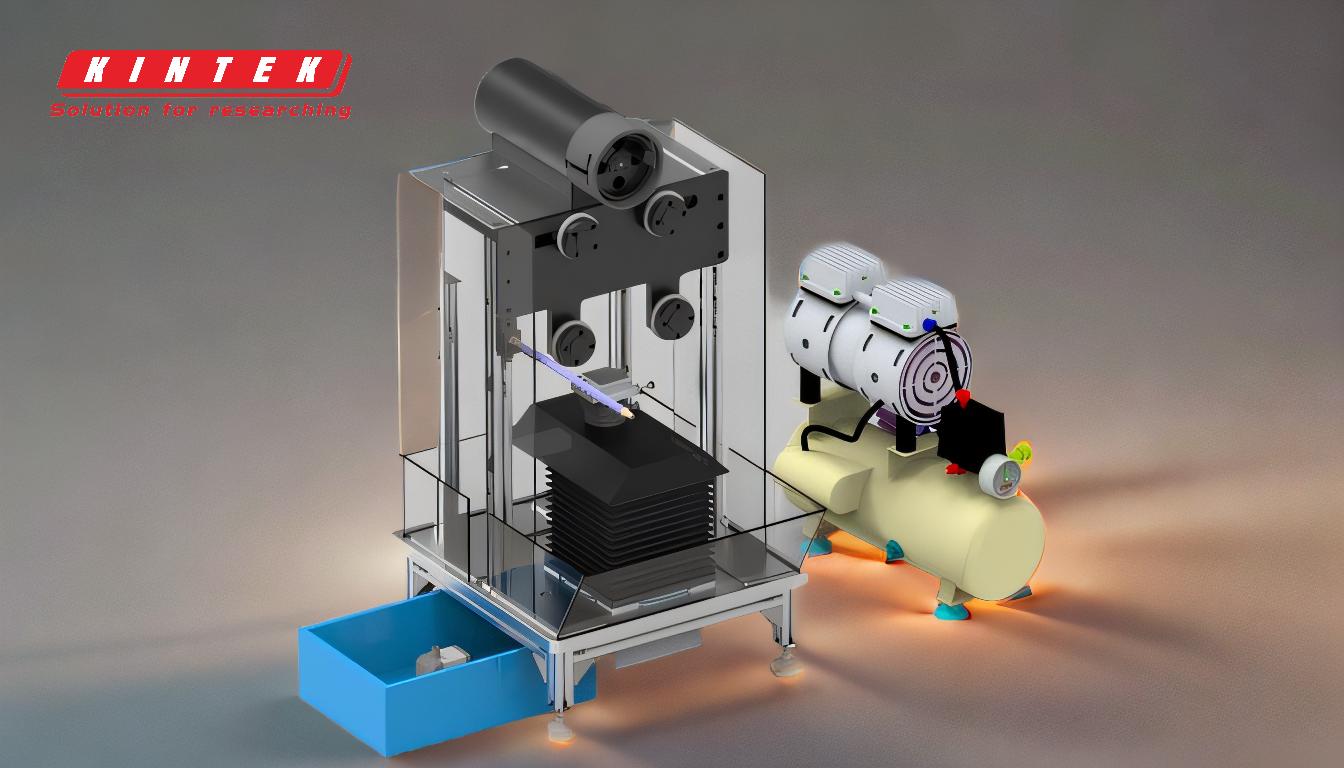
-
Reduction of Contaminants:
- Thin-film deposition in a vacuum minimizes the presence of unwanted gases and molecules, such as oxygen, nitrogen, and moisture, which can contaminate the film.
- Contaminants can react with the film material, leading to impurities or defects that degrade the film's quality and performance.
- For example, in organic light-emitting devices (OLEDs) or organic photovoltaics, even trace amounts of oxygen or moisture can quench the functional species responsible for light emission or absorption, significantly reducing device efficiency.
-
Improved Adhesion:
- A vacuum ensures that film particles reach the substrate with higher energy, enhancing their ability to bond firmly with the substrate.
- In processes like physical vapor deposition (PVD), the absence of air or other fluids prevents the slowing down of particles, allowing them to deposit with greater force and adhesion.
- Strong adhesion is critical for the durability and performance of the thin film in applications such as coatings, electronics, and optics.
-
Longer Mean Free Path:
- In a vacuum, the mean free path of particles (the average distance a particle travels before colliding with another) is significantly increased.
- This allows sputtered atoms or evaporated materials to travel directly from the source (e.g., sputtering target or evaporation material) to the substrate without interference, resulting in a more uniform and smoother deposition.
- For instance, in DC sputtering, a longer mean free path ensures that atoms deposit evenly across the substrate, reducing defects and improving film quality.
-
Controlled and Repeatable Processes:
- A vacuum environment provides precise control over gas composition, pressure, and mass flow, which are essential for repeatable and high-quality deposition processes.
- This control is particularly important in applications requiring consistent film properties, such as semiconductor manufacturing or optical coatings.
- The ability to maintain a low-pressure plasma environment further enhances the precision and reliability of the deposition process.
-
Enhanced Film Purity:
- High vacuum environments reduce the partial pressure of background gases, such as oxygen and moisture, to extremely low levels (e.g., below 10^-6 Torr).
- This significantly enhances the purity of the deposited film, which is critical for applications like microelectronics, where even minor impurities can affect device performance.
- High-purity films are also essential for advanced technologies like quantum computing and high-efficiency solar cells.
-
Optimized Plasma Environment:
- A vacuum enables the creation of a low-pressure plasma environment, which is essential for many deposition techniques, such as sputtering and plasma-enhanced chemical vapor deposition (PECVD).
- The plasma environment facilitates the ionization of gases and the activation of deposition processes, improving the efficiency and quality of the film formation.
- This is particularly beneficial for depositing complex materials or multilayer structures with precise control over thickness and composition.
-
Material Quality Considerations:
- The quality of the thin film is also influenced by the purity, grain size, and surface condition of the sputtering targets or evaporation materials used.
- High-purity materials with small grain sizes and smooth surfaces are preferred to minimize defects and ensure uniform deposition.
- For example, in semiconductor manufacturing, the use of high-quality targets is critical to achieving the desired electrical and optical properties of the thin film.
By performing thin-film deposition in a vacuum, manufacturers can achieve films with high purity, strong adhesion, uniform thickness, and consistent properties, making it an essential requirement for a wide range of advanced applications.
Summary Table:
Key Benefit | Explanation |
---|---|
Reduction of Contaminants | Minimizes unwanted gases like oxygen and moisture, preventing film contamination. |
Improved Adhesion | Ensures particles bond firmly with the substrate, enhancing durability. |
Longer Mean Free Path | Allows particles to travel unimpeded, resulting in smoother, uniform films. |
Controlled Processes | Enables precise control over gas composition, pressure, and plasma conditions. |
Enhanced Film Purity | Reduces impurities, critical for microelectronics and advanced technologies. |
Optimized Plasma Environment | Facilitates efficient deposition techniques like sputtering and PECVD. |
Material Quality | High-purity targets ensure uniform deposition and superior film properties. |
Achieve superior thin-film deposition results—contact our experts today for tailored solutions!