Steam is added to a pyrolysis furnace to enhance the thermal decomposition process, improve the quality of the output gases, and ensure efficient operation. It serves multiple purposes, including acting as a heat transfer medium, preventing coke formation, and facilitating the breakdown of complex hydrocarbons. By introducing steam, the pyrolysis process becomes more controlled and effective, leading to better yields of valuable gases and reduced operational issues.
Key Points Explained:
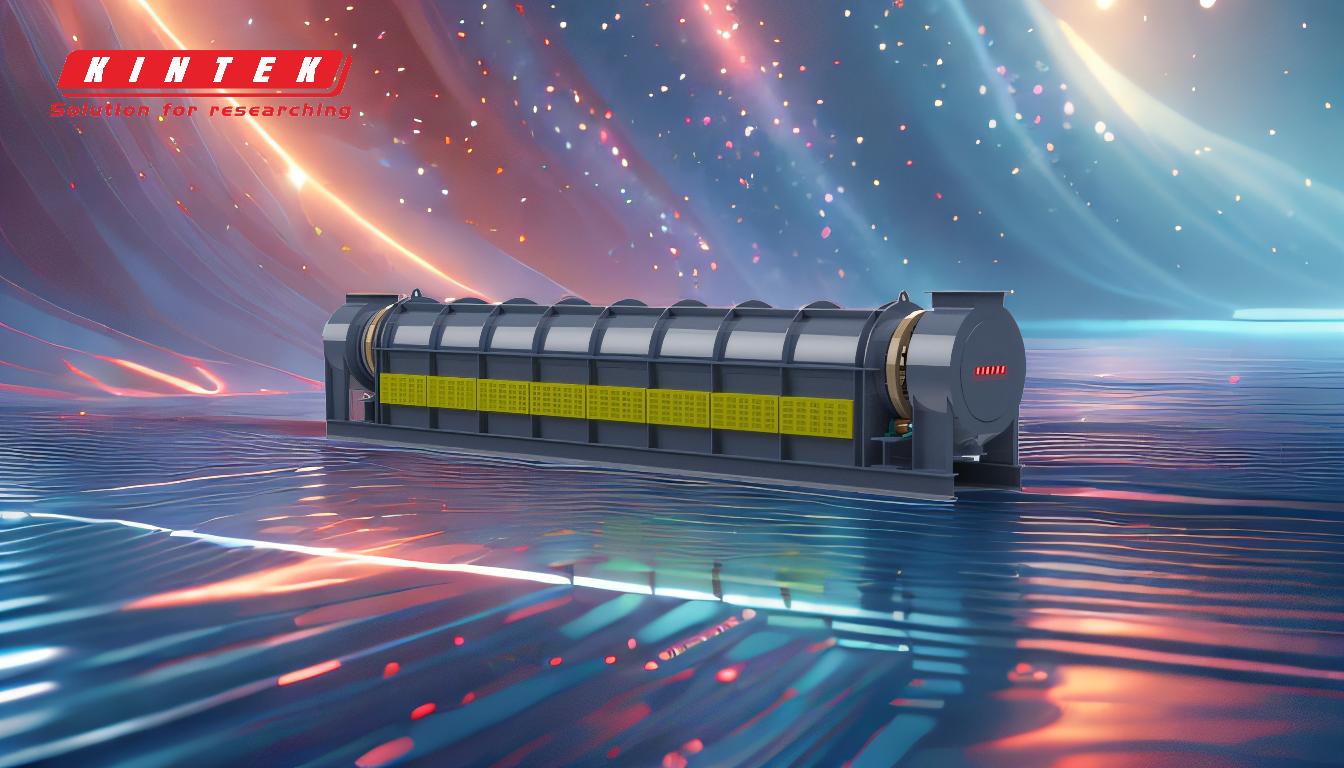
-
Enhanced Heat Transfer:
- Steam acts as an excellent heat transfer medium due to its high thermal conductivity and specific heat capacity. When introduced into the pyrolysis furnace, it helps distribute heat more evenly across the feedstock, ensuring uniform thermal decomposition. This is particularly important in a pyrolysis plant, where consistent temperatures are crucial for optimal performance.
-
Prevention of Coke Formation:
- One of the challenges in pyrolysis is the formation of coke, a carbon-rich residue that can clog the furnace and reduce efficiency. Steam reacts with carbon deposits, converting them into carbon monoxide and hydrogen through a process called steam reforming. This reaction not only prevents coke buildup but also produces syngas, a valuable byproduct.
-
Improved Gas Quality:
- The addition of steam promotes the breakdown of complex hydrocarbons into simpler molecules, such as methane, hydrogen, and carbon monoxide. This results in a higher-quality gas mixture, which is more suitable for further processing or use as a fuel. The presence of steam also helps reduce the formation of tar, which can be problematic in downstream applications.
-
Control of Reaction Kinetics:
- Steam influences the reaction kinetics within the pyrolysis furnace. By adjusting the steam-to-feedstock ratio, operators can control the rate of decomposition and the composition of the resulting gases. This flexibility allows for optimization of the process based on the specific feedstock and desired output.
-
Environmental Benefits:
- Using steam in the pyrolysis process can reduce the emission of harmful pollutants. For instance, steam helps convert sulfur compounds into hydrogen sulfide, which can be more easily removed from the gas stream. Additionally, the production of syngas (a mixture of hydrogen and carbon monoxide) can be used in cleaner energy applications, contributing to a reduction in greenhouse gas emissions.
-
Operational Efficiency:
- The introduction of steam can improve the overall efficiency of the pyrolysis furnace. By maintaining a stable temperature and reducing the risk of coke formation, the furnace can operate continuously with minimal downtime. This leads to higher throughput and lower operational costs.
In summary, steam plays a critical role in the pyrolysis process by enhancing heat transfer, preventing coke formation, improving gas quality, controlling reaction kinetics, providing environmental benefits, and boosting operational efficiency. Its inclusion is essential for the effective and sustainable operation of a pyrolysis plant.
Summary Table:
Purpose | Benefits |
---|---|
Enhanced Heat Transfer | Ensures uniform thermal decomposition and consistent temperatures. |
Prevention of Coke Formation | Converts carbon deposits into syngas, reducing clogging and improving efficiency. |
Improved Gas Quality | Breaks down complex hydrocarbons into simpler, high-quality gases. |
Control of Reaction Kinetics | Adjusts steam-to-feedstock ratio for optimized decomposition and gas output. |
Environmental Benefits | Reduces harmful pollutants and supports cleaner energy applications. |
Operational Efficiency | Maintains stable temperatures, reduces downtime, and lowers operational costs. |
Want to optimize your pyrolysis process with steam? Contact our experts today for tailored solutions!