Vacuum environments are essential in thin-film deposition processes to ensure high-quality, contamination-free films. The absence of air and other gases in a vacuum prevents oxidation, contamination, and unwanted chemical reactions, which are critical for achieving precise film properties. Additionally, vacuum conditions enable better control over deposition parameters, such as temperature and pressure, leading to uniform and defect-free thin films. The use of a vacuum cleaning furnace further enhances the process by maintaining a clean and controlled environment, ensuring the integrity of the deposited materials.
Key Points Explained:
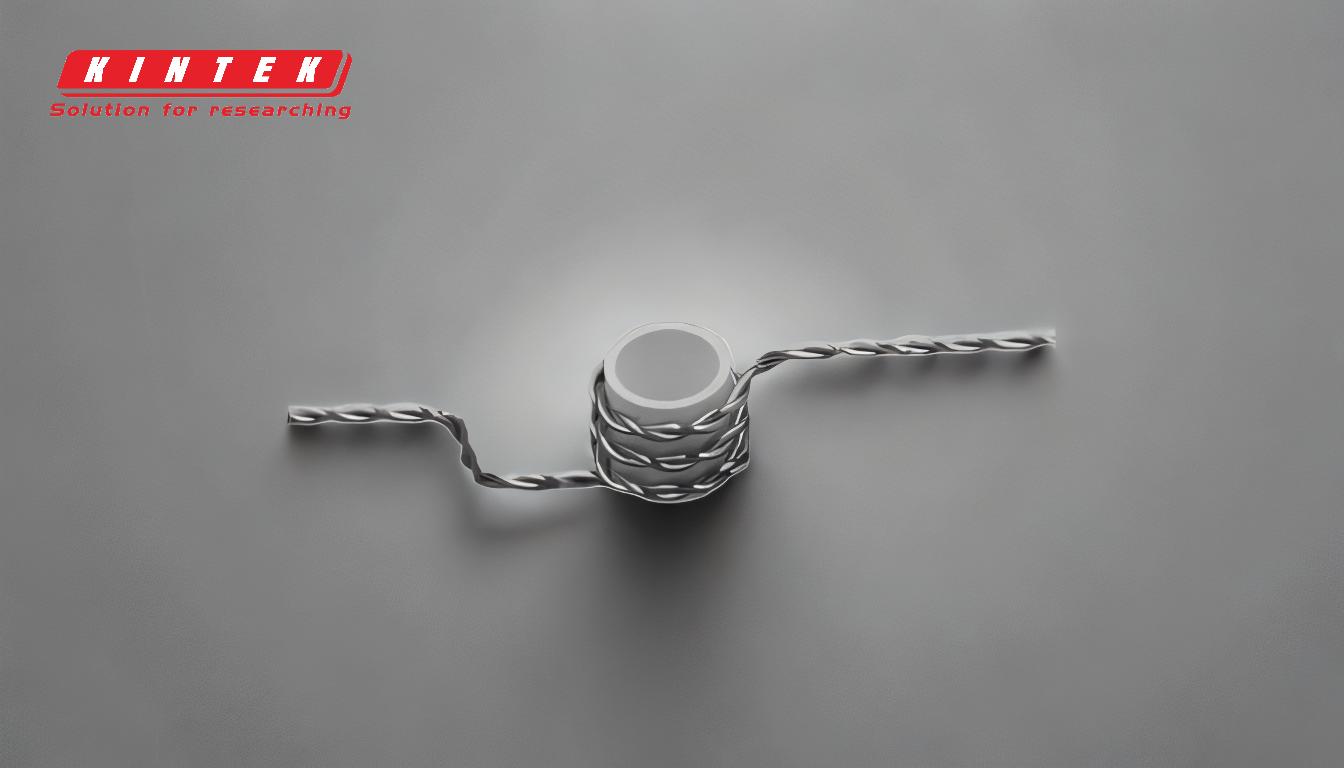
-
Prevention of Oxidation and Contamination:
- In a vacuum environment, the absence of air and other gases eliminates the risk of oxidation and contamination. This is crucial for materials that are highly reactive with oxygen or other atmospheric gases.
- For example, metals like aluminum or titanium can easily oxidize in the presence of air, leading to degraded film quality. A vacuum ensures these materials remain pure and unaltered during deposition.
-
Control Over Deposition Parameters:
- Vacuum conditions allow for precise control over temperature and pressure, which are critical for achieving uniform thin films.
- In a vacuum, the mean free path of particles increases, allowing for more controlled and directed deposition. This results in films with fewer defects and better adhesion to the substrate.
-
Enhanced Material Integrity:
- A vacuum furnace prevents material degradation by maintaining a low-pressure or vacuum environment. This is particularly important for processes like sintering, annealing, and heat treatment, where material integrity is paramount.
- For instance, in the case of semiconductor manufacturing, even minor contamination can lead to device failure. A vacuum ensures that the materials remain uncontaminated and maintain their desired properties.
-
Environmental Benefits:
- Vacuum furnaces, including vacuum cleaning furnaces, operate without emitting waste gases or water, making them environmentally friendly.
- This not only helps in maintaining a good atmospheric environment but also reduces the need for treating three wastes (waste gas, waste water, and solid waste), thereby lowering the pressure on air pollution treatment.
-
Alignment with Modern Environmental Standards:
- The use of vacuum technology in thin-film deposition aligns with modern social industrialization's environmental standards.
- By reducing emissions and waste, vacuum furnaces contribute to sustainable manufacturing practices, which are increasingly important in today's environmentally conscious world.
In summary, the requirement for a vacuum in thin-film deposition is driven by the need to prevent contamination, control deposition parameters, maintain material integrity, and align with environmental standards. The use of a vacuum cleaning furnace further enhances these benefits by ensuring a clean and controlled environment, making it an indispensable tool in modern thin-film deposition processes.
Summary Table:
Key Benefits of Vacuum in Thin-Film Deposition |
---|
Prevents Oxidation and Contamination |
- Eliminates air and gases to avoid material degradation. |
Precise Control Over Deposition Parameters |
- Enables uniform temperature and pressure for defect-free films. |
Maintains Material Integrity |
- Ensures uncontaminated materials for processes like sintering and annealing. |
Environmental Benefits |
- No waste gases or water emissions, aligning with sustainability standards. |
Aligns with Modern Environmental Standards |
- Reduces emissions and waste, supporting eco-friendly manufacturing. |
Optimize your thin-film deposition process with a vacuum cleaning furnace—contact us today to learn more!