Introduction to Isostatic Graphite
Definition and Properties
Isostatic graphite is meticulously crafted through a process known as isostatic pressing, which imparts it with a uniform structure, high density, and remarkable isotropy. This uniformity is a hallmark of its superior performance in various industrial applications. The classification of isostatic graphite into ultrafine, fine, and coarse categories is primarily based on the diameter of its particles, each type offering distinct advantages depending on the specific requirements of the application.
Particle Diameter | Characteristics | Applications |
---|---|---|
Ultrafine | Extremely small particle size, high purity | Precision components, semiconductor industry |
Fine | Small particle size, high density | High-performance heating elements, crucibles |
Coarse | Larger particle size, high strength | Structural components, heavy-duty applications |
This classification not only highlights the versatility of isostatic graphite but also underscores its adaptability to a wide range of industrial needs, making it an indispensable material in sectors such as the photovoltaic industry.
Characteristics
Isostatic graphite is renowned for its exceptional physical and chemical properties, making it a preferred material in various high-tech industries. Its high strength ensures durability and resistance to mechanical stress, while its high density contributes to superior thermal and electrical conductivity. The material's high purity minimizes impurities that could affect its performance, enhancing its overall reliability.
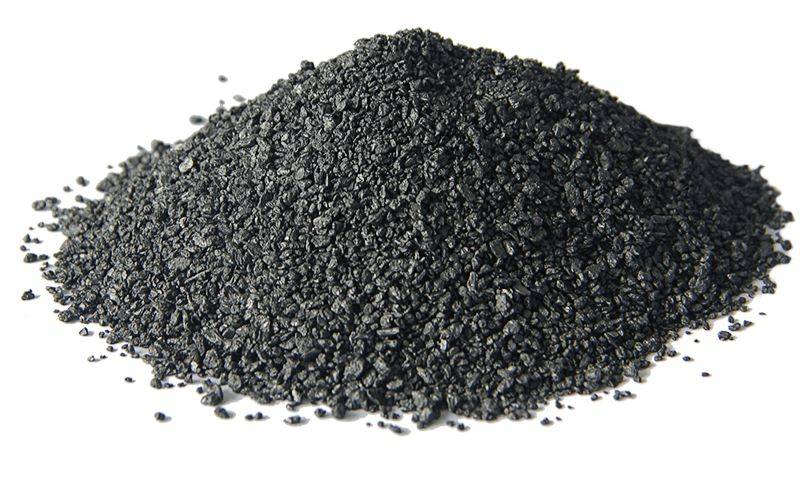
In terms of chemical stability, isostatic graphite remains inert under a wide range of chemical environments, making it ideal for applications where resistance to corrosive substances is crucial. Its thermal and electrical conductivity are also noteworthy, enabling efficient heat transfer and electrical conduction, which are essential in high-temperature and high-energy applications.
Moreover, isostatic graphite exhibits remarkable temperature and radiation resistance, allowing it to maintain its structural integrity and performance under extreme conditions. Its lubricity reduces friction in moving parts, extending the lifespan of components. Lastly, the material's ease of processing ensures that it can be shaped and machined to meet precise specifications, facilitating its integration into complex systems.
Applications in the Photovoltaic Industry
Polysilicon Material Production
Isostatic graphite plays a crucial role in the production of polysilicon, a key material in the photovoltaic industry. It is utilized in various critical components such as HCL synthesis devices, valves, gas distributors, heating elements, and insulation barrels. These components are essential for the efficient and controlled synthesis of polysilicon, which involves the thermal decomposition of silane gas.
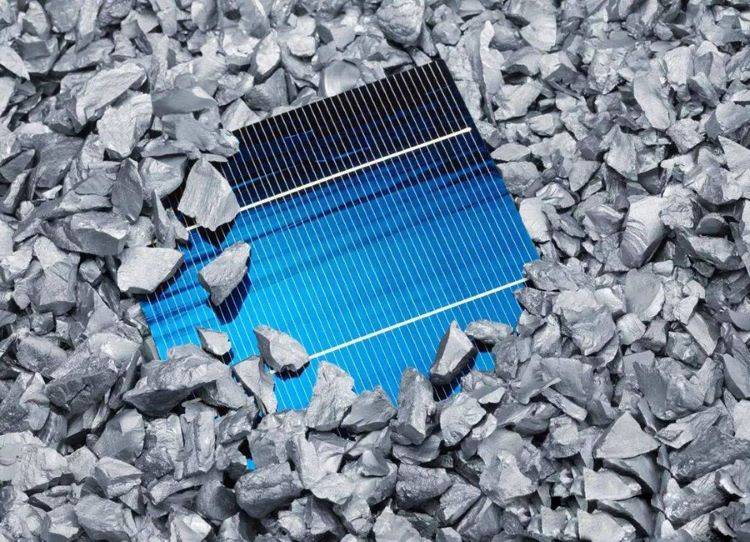
The resistivity of polysilicon is notably higher than that of single crystal silicon, even at the same doping level. This discrepancy arises because dopants tend to segregate along grain boundaries, leaving fewer dopant atoms within the grains. Additionally, defects at these boundaries reduce carrier mobility and create dangling bonds that can trap free carriers.
The deposition process of polysilicon involves pyrolysis, or thermal decomposition, of silane gas. This process yields solid silicon on the surface and hydrogen as an exhaust gas. Process engineers often employ a batch process in a hot-wall LPCVD furnace, using approximate values to control the reaction. To optimize the process, engineers may dilute the silane with a hydrogen carrier gas, which suppresses gas phase decomposition of silane. This is crucial because gas phase decomposition can result in silicon particles raining down on the growing film, causing surface roughening. Consequently, engineers modify the deposition conditions, often adapting those used for amorphous silicon deposition, to achieve a slower and more controlled reaction.
By leveraging isostatic graphite in these critical applications, the polysilicon production process is enhanced, leading to higher quality and more efficient solar-grade silicon.
Single Crystal Growth Thermal Field
In the intricate process of single crystal growth, the precise control of thermal fields is paramount. This control is facilitated by the use of specialized components, each meticulously crafted from isostatic graphite. The components integral to this process include crucibles, heaters, insulation barrels, and guide tubes.
Crucibles, often the vessel of choice for melting and crystallizing materials, demand materials that can withstand extreme temperatures and maintain structural integrity. Isostatic graphite, renowned for its high density and uniform structure, meets these stringent requirements. Similarly, heaters, which are crucial for maintaining the desired temperature gradients, benefit from the superior thermal conductivity and stability of isostatic graphite.
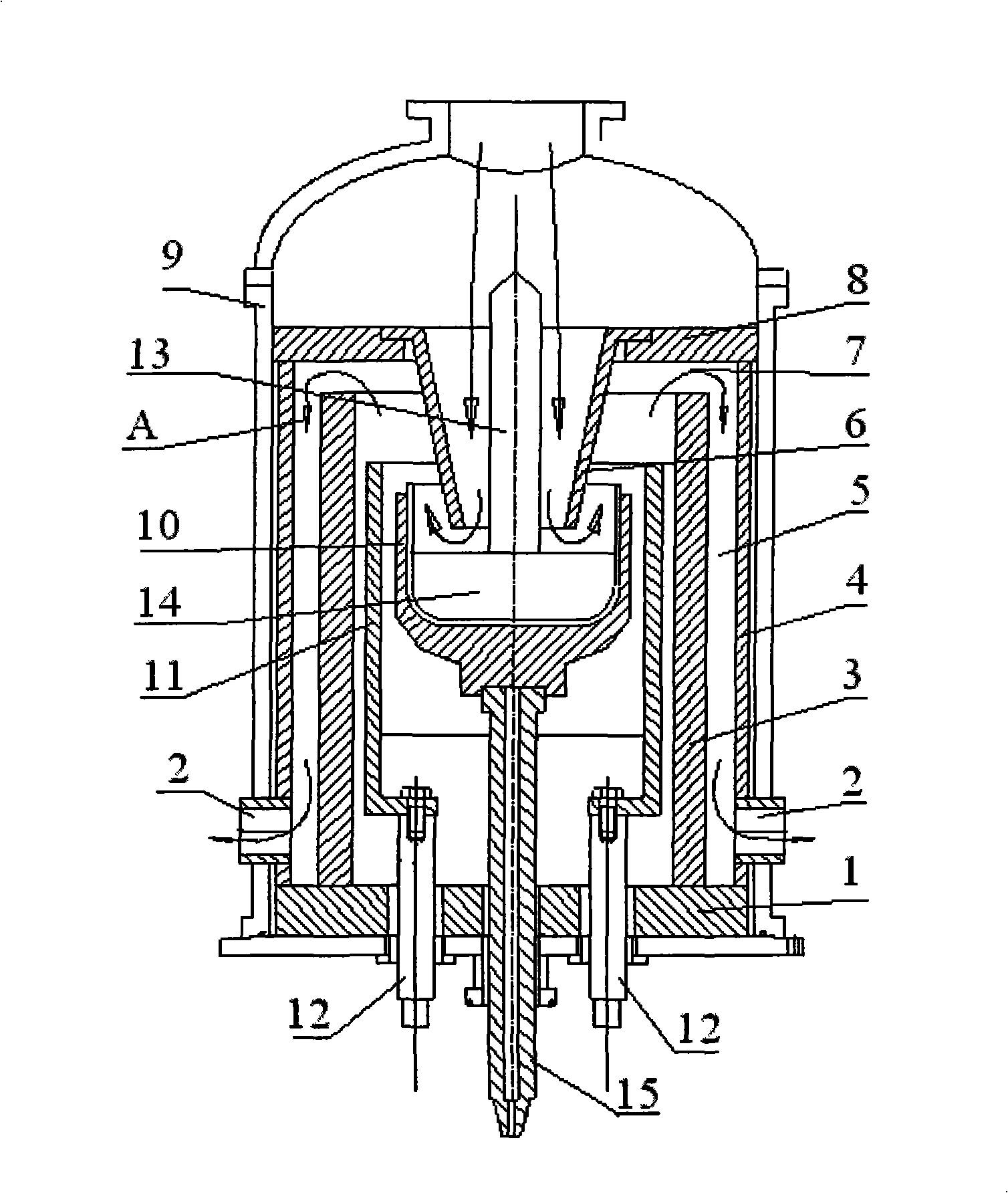
Insulation barrels play a pivotal role in ensuring that the thermal energy is directed precisely where it is needed, minimizing heat loss and optimizing the growth environment. Here, the low thermal expansion and excellent thermal shock resistance of isostatic graphite are invaluable. Lastly, guide tubes, which assist in the precise alignment of the growing crystal, require materials that are not only strong but also resistant to the corrosive environments often present in these processes. Isostatic graphite, with its high purity and chemical stability, is the material of choice in these applications.
In summary, the components involved in single crystal growth, from the crucibles to the guide tubes, collectively rely on the unique properties of isostatic graphite to achieve the high standards of quality and efficiency demanded by the industry.
Polycrystalline Ingot Thermal Field
In the production of polycrystalline ingots, the thermal field is meticulously managed to ensure the uniform distribution of heat, which is crucial for the quality and consistency of the final product. This process heavily relies on the use of isostatic graphite, a material known for its superior thermal conductivity and structural integrity.
Isostatic graphite is employed in several key components within the thermal field, including heaters, directional blocks, and side/bottom plates. These components are essential for maintaining the precise temperature gradients required during the crystallization process. The heaters, for instance, are designed to deliver uniform heat across the entire surface of the ingot, while the directional blocks guide the flow of heat to ensure that the crystal growth is aligned correctly. The side and bottom plates, made from isostatic graphite, provide additional insulation and support to the ingot, preventing thermal losses and ensuring that the heat is retained within the critical zones.
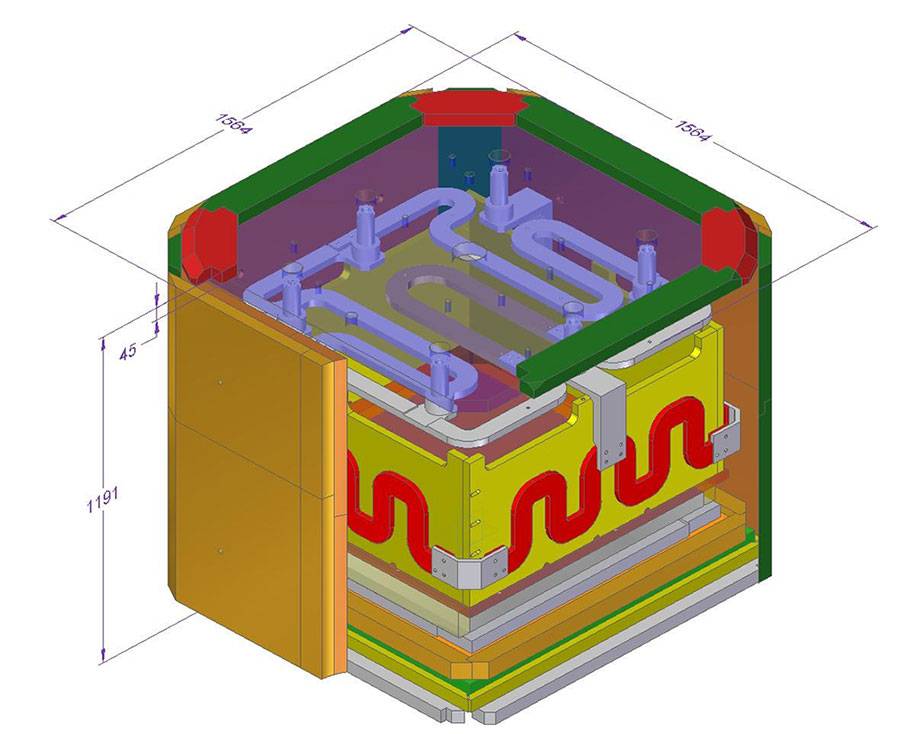
The use of isostatic graphite in these applications is not merely a matter of convenience but a necessity dictated by the stringent requirements of polycrystalline ingot production. The material's high density and uniform structure ensure that it can withstand the extreme temperatures and mechanical stresses associated with this process. Moreover, its chemical stability and resistance to thermal shock make it an ideal choice for components that are exposed to harsh environments.
In summary, the integration of isostatic graphite into the thermal field of polycrystalline ingot production is a testament to its unparalleled performance and reliability in high-temperature applications. This material not only enhances the efficiency and precision of the thermal management process but also contributes to the overall quality and yield of the polycrystalline ingots.
PEVCD Coating for Cell Production
In the realm of plasma-enhanced chemical vapor deposition (PEVCD) coating processes, the reliability and efficiency of graphite boats and wafer carriers are paramount. These components are meticulously crafted from isostatic graphite, a material renowned for its uniform structure and exceptional properties.
Isostatic graphite, produced through a process of isostatic pressing, offers a high degree of isotropy and density. This uniformity ensures that the temperature distribution across the substrate is consistent, which is crucial in maintaining the integrity of the semiconductor wafers. The use of isostatic graphite in these applications not only reduces the risk of damage due to radiation and ion bombardment but also ensures that the process temperatures remain within the optimal range of 200 to 500°C. This temperature reduction is facilitated by the plasma assistance, which supports the chemical reactions necessary for the deposition of the final films.
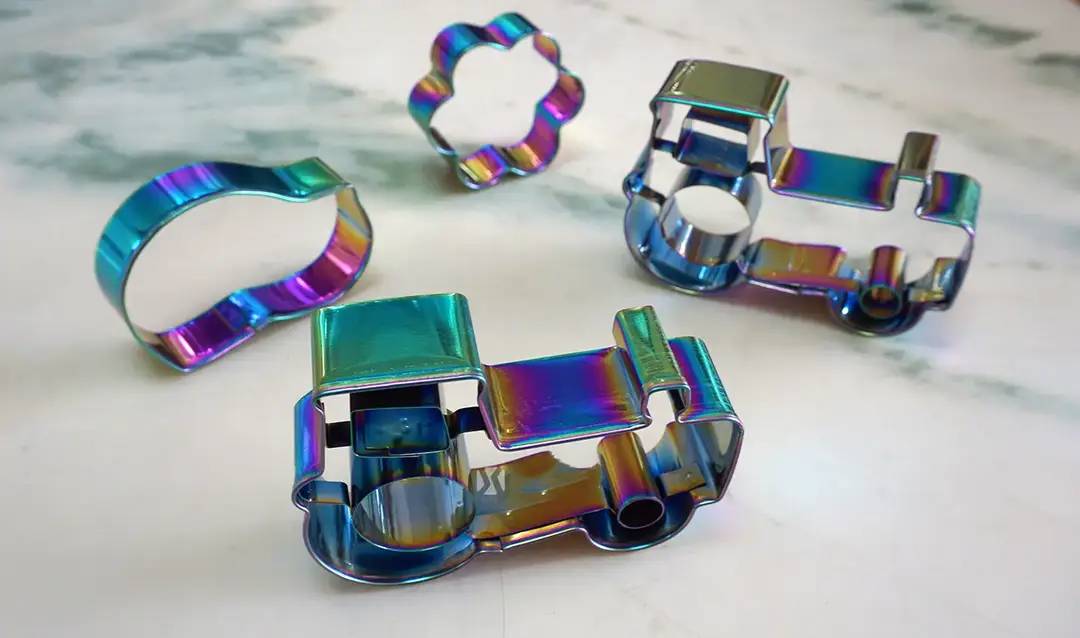
Moreover, the thermal and electrical conductivity of isostatic graphite further enhances its suitability for PEVCD processes. These properties ensure that heat is evenly distributed, preventing hotspots that could compromise the quality of the deposited films. The chemical stability of isostatic graphite also plays a significant role, as it resists degradation under the high-temperature and reactive conditions typical of PEVCD applications.
In summary, the integration of isostatic graphite in PEVCD coating processes for cell production underscores the material's critical role in ensuring the precision, efficiency, and reliability of these advanced manufacturing techniques.
Technical Specifications and Market Demand
Specifications of Isostatic Graphite
Isostatic graphite is available in various sizes to cater to different heater applications, with mainstream dimensions including 1100x1100mm and 960x870mm. These sizes are meticulously chosen to ensure optimal performance in high-temperature environments, where traditional graphite materials may fall short.
Size (mm) | Application |
---|---|
1100x1100 | High-capacity heater components |
960x870 | Precision heater elements |
Beyond size, isostatic graphite is categorized into three distinct levels based on critical properties such as density, bending resistance, and ash content. This categorization allows for tailored applications, ensuring that each level of graphite meets the specific demands of advanced equipment production.
- Level 1: High density and bending resistance, low ash content. Ideal for applications requiring maximum durability and thermal stability.
- Level 2: Moderate density and bending resistance, slightly higher ash content. Suitable for general-purpose high-temperature applications.
- Level 3: Lower density and bending resistance, higher ash content. Used in less demanding thermal environments where cost-effectiveness is a priority.
These classifications ensure that isostatic graphite can be precisely matched to the exacting requirements of various industrial processes, from polysilicon production to single crystal growth, thereby enhancing overall efficiency and performance.
Market Demand and Growth
The photovoltaic industry has witnessed a significant surge in demand for special graphite, with a staggering 51.80% increase in 2022. This trend is projected to continue, with demand expected to grow by 24.69% to 46.91% in 2023. This growth is driven by the expanding number of operating furnaces in the photovoltaic market, which currently consume approximately RMB 4.5 to 5 billion worth of isostatic graphite.
The burgeoning demand for isostatic graphite is closely tied to its indispensable role in various stages of photovoltaic production. From the synthesis of HCL in polysilicon material production to the thermal fields of single crystal growth and polycrystalline ingot production, isostatic graphite is integral to maintaining the high standards of efficiency and quality required in these processes.
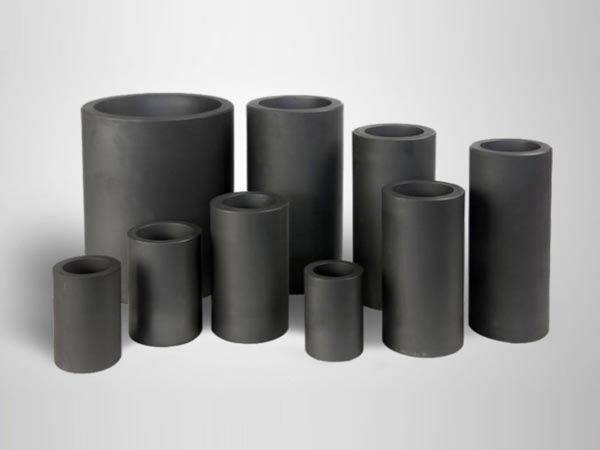
Moreover, the technical specifications of isostatic graphite, including its high density, strength, and thermal conductivity, make it the material of choice for applications ranging from crucibles and heaters to insulation barrels and graphite boats. The industry's reliance on isostatic graphite is further underscored by the fact that mainstream sizes, such as 1100x1100mm and 960x870mm, are tailored to meet the specific needs of different heater applications.
In summary, the photovoltaic industry's insatiable demand for isostatic graphite is a testament to its critical role in enhancing production efficiency and ensuring the quality of photovoltaic products. As the industry continues to expand, the demand for this specialized material is expected to follow suit, driving further growth and innovation in the market.
CONTACT US FOR A FREE CONSULTATION
KINTEK LAB SOLUTION's products and services have been recognized by customers around the world. Our staff will be happy to assist with any inquiry you might have. Contact us for a free consultation and talk to a product specialist to find the most suitable solution for your application needs!