The Advantages of Isostatic Compaction over Cold Pressing
Table of Contents
- The Advantages of Isostatic Compaction over Cold Pressing
- Uniform pressure application
- Absence of die-wall friction
- Higher and more uniform densities
- Elimination of die-wall lubricants
- Air evacuation from loose powder
- Increased density at given compaction pressure
- Freedom from compact defects with brittle or fine powders
- No limitation of cross section-to-height ratio of the part
- Ability to compact complex shapes
- Comparison of Isostatic Pressing with Die Compaction in High Densities
- Isostatic Pressure Distribution in Cold Pressed Compact
Uniform pressure application
Isostatic pressing, also known as cold isostatic pressing, is a process that involves compacting a dry or semi-dry powder in an elastomeric mold submerged in a pressurized liquid. One of the key advantages of isostatic compaction over cold pressing is the uniform pressure application. Unlike in cold pressing, where pressure is applied unidirectionally, isostatic compaction applies pressure uniformly over the entire surface of the mold. This results in more uniform density distribution throughout the compacted part, leading to greater homogeneity and more precise control of the finished product dimensions.
Absence of die-wall friction
Die-wall friction is a major factor that influences the density distribution of cold-pressed parts. In isostatic compaction, die-wall friction is absent, allowing for much more uniform densities to be obtained. This absence of friction also eliminates problems associated with lubricant removal prior to or during final sintering. As a result, isostatic compaction permits higher pressed densities and provides increased and more uniform density at a given compaction pressure.
Higher and more uniform densities
Due to the absence of die-wall friction and the uniform pressure application, isostatic compaction can achieve higher and more uniform densities compared to cold pressing. The elimination of die-wall lubricants further contributes to the ability to obtain higher pressed densities. This is particularly advantageous when working with brittle or fine powders, as isostatic compaction offers relative freedom from compact defects.
Elimination of die-wall lubricants
Another advantage of isostatic compaction is the elimination of die-wall lubricants. This allows for higher pressed densities and eliminates the need for lubricant removal prior to or during final sintering. The absence of die-wall lubricants also simplifies the compaction process and reduces the associated challenges and potential issues.
Air evacuation from loose powder
Isostatic compaction offers the ability to evacuate air from loose powder before compaction, if necessary. This helps to ensure a more uniform compaction and density distribution within the compacted part. By removing air from the powder, isostatic compaction helps to reduce the risk of porosity and other defects in the final product.
Increased density at given compaction pressure
Compared to cold pressing, isostatic compaction provides increased and more uniform density at a given compaction pressure. This is due to the uniform pressure application and the absence of die-wall friction. The ability to achieve higher densities at lower pressures can lead to cost savings and improved efficiency in the manufacturing process.
Freedom from compact defects with brittle or fine powders
Isostatic compaction offers relative freedom from compact defects when working with brittle or fine powders. The uniform pressure application and the absence of die-wall friction help to minimize the risk of cracks, voids, and other defects in the compacted part. This is particularly beneficial when working with materials that are prone to brittleness or have fine particle sizes.
No limitation of cross section-to-height ratio of the part
Unlike cold pressing, where the cross section-to-height ratio of the part can be a limiting factor, isostatic compaction does not have this limitation. The uniform pressure application allows for the compaction of parts with complex shapes and varying cross section-to-height ratios. This versatility in shape and size makes isostatic compaction suitable for a wide range of applications and allows for greater design flexibility.
Ability to compact complex shapes
One of the key advantages of isostatic compaction is the ability to compact more complex shapes compared to uniaxial pressing. The uniform pressure application and the absence of die-wall friction enable the compaction of parts with internal shapes, including threads, splines, serrations, and tapers. This makes isostatic compaction a versatile process for producing parts with intricate designs and features.

Isostatic compaction offers a range of advantages over cold pressing, including uniform pressure application, absence of die-wall friction, higher and more uniform densities, elimination of die-wall lubricants, air evacuation from loose powder, increased density at a given compaction pressure, freedom from compact defects with brittle or fine powders, no limitation of cross section-to-height ratio of the part, and the ability to compact complex shapes. These advantages make isostatic compaction a preferred choice for many applications in various industries.
Comparison of Isostatic Pressing with Die Compaction in High Densities
Similar green densities with iron and aluminum powders
Both die compaction and isostatic pressing can produce similar green densities with iron and aluminum powders when compacted to high densities. This means that both methods are effective in achieving the desired density for these materials.
Equal radial and axial pressure with aluminum
For materials like aluminum that have constant shear stress, the radial pressure becomes approximately equal to the axial pressure during isostatic pressing. This means that the pressure distribution becomes more uniform, approaching an isostatic pressure distribution. This is advantageous for achieving consistent density throughout the compact.
Less radial than axial pressure with copper
On the other hand, for materials like copper where the yield stress is a function of the normal stress on the shear plane, the radial pressure remains less than the axial pressure during isostatic pressing. This means that there may be some variation in density between the radial and axial directions in the compact.
Isostatic pressing offers several advantages over die compaction, especially for materials that require high densities. The elimination of die-wall lubricants allows for higher pressed densities and eliminates problems associated with lubricant removal prior to or during final sintering. Isostatic compaction also provides increased and more uniform density at a given compaction pressure, resulting in relative freedom from compact defects when applied to brittle or fine powders. Additionally, isostatic compaction can be used to compact more complex shapes than possible with uniaxial pressing.
Compared with cold pressing, isostatic compaction applies pressure uniformly over the entire surface of the mold, resulting in more uniform densities. The elimination of die-wall friction and lubricants further contributes to the achievement of higher pressed densities. Air can also be evacuated from the loose powder before compaction, ensuring a more uniform and dense final product. These factors make isostatic compaction a preferred method for achieving high densities and uniformity in the resulting compact.
In conclusion, while both die compaction and isostatic pressing can achieve similar green densities with iron and aluminum powders, isostatic pressing offers the advantage of more uniform density distribution. For materials like copper, where the yield stress is influenced by the normal stress on the shear plane, there may be some variation in density between the radial and axial directions during isostatic pressing. Overall, isostatic pressing provides increased and more uniform density at a given compaction pressure, making it a preferred method for achieving high densities and uniformity in compacted materials.
Isostatic Pressure Distribution in Cold Pressed Compact
Possibility of isostatic pressure distribution within a cold pressed compact
Cold pressing is a common method used to compact powders into a desired shape. However, one of the limitations of cold pressing is the uneven distribution of pressure, which can result in uneven density distribution within the compacted part. This is due to the presence of die-wall friction, which exerts a major influence on the density distribution of cold-pressed parts.
In contrast, isostatic compaction applies pressure uniformly over the entire surface of the mold. This uniform pressure distribution eliminates die-wall friction and allows for much more uniform densities to be obtained. The elimination of die-wall lubricants also enables higher pressed densities and eliminates problems associated with lubricant removal prior to or during final sintering.
Furthermore, isostatic compaction offers the advantage of evacuating air from the loose powder before compaction, resulting in increased and more uniform density at a given compaction pressure. This is particularly beneficial when working with brittle or fine powders, as it helps to minimize compact defects.
Another advantage of isostatic compaction is that it is not limited by the cross section-to-height ratio of the part, unlike uniaxial pressing. This means that more complex shapes can be compacted using the cold isostatic pressing method.
Uniform density distribution as a requirement for identical pressure vs. density relationship with isostatic compacting
While the pressure distribution within a cold pressed compact may become isostatic, it is important to note that the pressure vs. density relationship should be identical to that of isostatic compacting only if the density distribution is equally uniform. In other words, in order to achieve the desired pressure vs. density relationship, it is crucial to ensure a uniform density distribution throughout the compacted part.
In the cold isostatic pressing process, a mold or vacuumed sample is placed into a chamber that is filled with a working fluid, usually water with a corrosion inhibitor. The chamber is then pressurized by an external pump, allowing for the uniform application of pressure throughout the entire surface of the mold.
It is worth mentioning that cold isostatic pressing has been found to be advantageous for most materials, except for aluminum and iron compacted to high densities. At high densities, both die and isostatic compaction produce similar green densities with iron and aluminum powders. However, for materials like copper, where the yield stress is a function of the normal stress on the shear plane, the radial pressure remains less than the axial pressure.
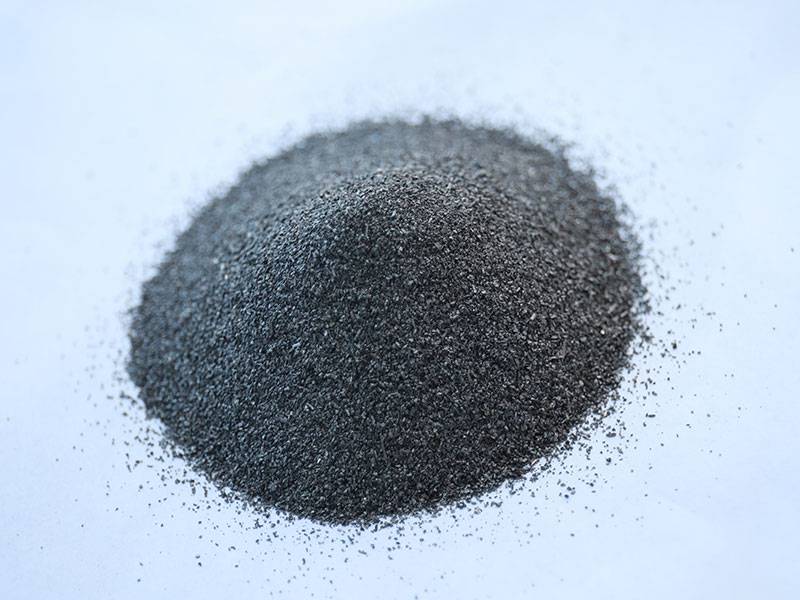
Overall, cold isostatic pressing offers several benefits over cold pressing, including uniform density distribution, the ability to compact complex shapes, and increased density at a given compaction pressure. It is an effective method for achieving isostatic pressure distribution within a cold pressed compact, provided that the density distribution is equally uniform.
If you are interested in this product you can browse our company website: https://kindle-tech.com/product-categories/isostatic-press, we always insist on the principle of quality first. During the production process, we strictly control every step of the process, using high quality materials and advanced production technology to ensure the stability and durability of our products. to ensure that their performance meets the highest standards. We believe that only by providing customers with excellent quality can we win their trust and long-term cooperation.
CONTACT US FOR A FREE CONSULTATION
KINTEK LAB SOLUTION's products and services have been recognized by customers around the world. Our staff will be happy to assist with any inquiry you might have. Contact us for a free consultation and talk to a product specialist to find the most suitable solution for your application needs!