Introduction to XRF Analysis and Sample Preparation
X-ray fluorescence (XRF) analysis is a non-destructive method used to determine the elemental composition of a sample. Sample preparation is a crucial step in XRF analysis and is essential for obtaining accurate results. The sample must be homogenized, dried, and ground to a fine powder to ensure that the particles are small enough to be analyzed by XRF. Sample preparation methods can vary depending on the type of sample being analyzed. Pressed pellets are a common method used to prepare solid samples for XRF analysis. Pellet preparation involves applying pressure to the sample to form a flat, disk-shaped pellet. The quality of the pellet can significantly affect the accuracy of the XRF analysis. Therefore, it is essential to understand the impact of pressure on the quality of XRF pellets.
Table of Contents
- Introduction to XRF Analysis and Sample Preparation
- Overview of Pressed Pellets for XRF Analysis
- The Importance of Pressure in Pellet Preparation
- Effects of Inadequate Pressure on Pellet Quality
- Optimal Pressure Ranges for High-Quality Pellets
- Importance of Consistency in Pressure Application
- Conclusion: Pressure's Impact on XRF Pellet Quality
Overview of Pressed Pellets for XRF Analysis
X-ray Fluorescence spectroscopy (XRF) is highly sensitive to the preparation of the sample material. Pressed pellets for XRF analysis is one of the most common methods of preparing samples for XRF analysis.
Sample Preparation
Producing pressed pellets requires accuracy and specific measurements, and pelletizing works well when samples are ground to a particle size of <50µm, although <75µm is also acceptable. Working with small particle sizes is important because this impacts how well the sample binds together under pressure, which impacts the analytical results.
The process of making pressed pellets includes grinding the sample to a fine particle size, mixing it with a binder/grinding aid in a grinding or mixing vessel, pouring the mixture into a pressing die, and pressing the sample at a pressure of between 15 and 35T. The resulting pellet or tablet is ready for analysis.
Advantages of Pressed Pellets for XRF Analysis
Pressed pellets deliver better results compared to no prep at all, also greater consistency. An analyst can produce samples very fast in automated systems or slower using manual presses and obtain the same pellet quality. Overall, it is considered a convenient, cost-effective, and reliable sample preparation technique that has become an industry standard.
Factors Affecting XRF Analysis Procedure
When a sample is analyzed using an XRF spectrometer, certain characteristics can impact the signal received. The background scattering and intensity of the emission peaks are all affected by particle size, mineral composition, and particle density. However, the grinding of samples to a very fine particle size and then compressing them into a smooth and flat XRF pellet reduces the background scattering and improves the detection of emissions.
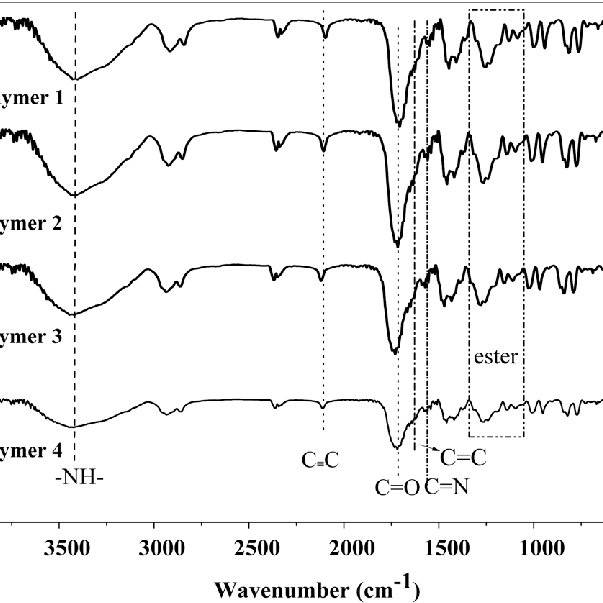
Advantages of Using Pellets for XRF
X-ray fluorescence (XRF) analysis is a widely used technique in elemental analysis that requires the preparation of samples in the form of pellets. The quality of the pellets is crucial for accurate and precise results. Using pressed pellets for XRF analysis has several advantages, including higher signal-to-noise ratio, detection of the lightest elements, and elimination of discrepancies observed between expected values and loose powder samples.
Sample Preparation Techniques
Before preparing pressed pellets, other steps might be necessary, depending on the raw sample particle size and material, to bring down the particle size enough to be used as a powder or pressed in pellets. It is commonly considered acceptable to have a particle diameter of 40 µm or lower.
The most common ways to prepare samples for XRF analysis are, in order of complexity and quality of results, no prep, pressed pellets, and fused beads. Pressed pellets have greater flexibility at a relatively lower cost with excellent results, although fusing beads deliver the best results because it eliminates the two main effects that influence results, the mineralogical effect, and the particle size effect.
Importance of Pellet Dies
Pellet dies are needed to form the pellet; they function as the mold in which the pellet is pressed. They must withstand the load and have the right size for the sample holder the spectrometer uses. Also, dies can be designed to speed up the process and make it easier and safer for the user to prepare the pellets.
The Importance of Pressure in Pellet Preparation
Introduction
X-ray fluorescence (XRF) analysis is a widely used method for determining the elemental composition of materials, and sample preparation is a critical aspect of ensuring accurate and reliable results. Pressed pellets are a popular choice for XRF analysis, and the quality of the pellet is essential for obtaining accurate and reproducible results. In particular, the pressure applied during pellet preparation is a crucial factor that can significantly impact pellet quality.
Insufficient Pressure
Insufficient pressure during pellet preparation can lead to low-density pellets that crumble or disintegrate during analysis, resulting in inaccurate results. This can occur when the pressure applied is not high enough to compress the powders into a solid disc. Therefore, it is necessary to apply the correct pressure to ensure the highest possible pellet quality.
Excessive Pressure
On the other hand, excessive pressure can cause sample deformation, resulting in poor spectral quality. This can occur when the pressure applied is too high, causing the sample to deform and lose its integrity. As a result, the spectral quality is compromised, leading to inaccurate results.
Optimal Pressure
To ensure the highest quality pellets, it is necessary to apply the optimal pressure during pellet preparation. The optimal pressure is dependent on various factors, including the type of sample, the particle size, and the type of binding agent used. Laboratory technicians must be familiar with these factors to ensure consistent and reliable results.
Factors Affecting Optimal Pressure
The optimal pressure for pellet preparation can vary depending on the sample's characteristics, including its particle size, composition, and binding agent. For example, samples with smaller particle sizes require higher pressures to obtain a solid pellet. In contrast, samples with larger particle sizes require lower pressures to prevent sample deformation. The type of binding agent used can also affect the optimal pressure for pellet preparation, as some binding agents require higher pressures to ensure proper binding.
Conclusion
In conclusion, pressure is a critical factor in XRF pellet preparation, and careful attention must be paid to ensure that optimal pressure is applied to produce high-quality pellets. Insufficient pressure can lead to low-density pellets that crumble or disintegrate during analysis, while excessive pressure can cause sample deformation, resulting in poor spectral quality. Therefore, laboratory technicians must consider various factors, including the sample's characteristics and the type of binding agent used, to apply the optimal pressure for pellet preparation to ensure accurate and reliable results.
Effects of Inadequate Pressure on Pellet Quality
X-ray fluorescence (XRF) analysis is a widely used technique in the field of material characterization. XRF pellets are a common sample preparation technique used in XRF analysis. The quality of XRF pellets is critical to obtaining accurate and reliable analytical results. One of the key factors that impact pellet quality is the pressure applied during the pelletizing process. Inadequate pressure can lead to poor pellet quality, which can affect the accuracy and precision of analytical results.
Poor Pellet Homogeneity
Inadequate pressure can result in poor pellet homogeneity, which means that the sample is not evenly distributed throughout the pellet. The uneven distribution of the sample can cause a variation in the intensity of the X-ray signal received by the detector, leading to inaccurate results. Poor pellet homogeneity can also cause an increase in spectral background noise, which can further reduce the sensitivity of the analysis.
Low Pellet Density
The density of the pellet is directly related to the amount of pressure applied during the pelletizing process. Inadequate pressure can lead to low pellet density, which can result in decreased XRF signal intensity. The low pellet density can also cause problems during the analysis, such as the pellet crumbling or breaking into pieces.
Increased Porosity
Inadequate pressure can cause increased porosity in the pellet, which can lead to decreased sensitivity and accuracy of the analysis. The presence of void spaces in the pellet can cause the X-ray signal to scatter, leading to a reduction in intensity. The increased porosity can also cause sample loss or contamination.
Cracks or Voids
In some cases, inadequate pressure can even result in the formation of cracks or voids in the pellet. The presence of cracks or voids can cause the X-ray signal to scatter, leading to reduced sensitivity and accuracy of the analysis. Cracks or voids can also cause sample loss or contamination, thereby affecting the quality of the analytical results.
To avoid these issues, it is essential to optimize the pelletizing conditions, including the applied pressure, to ensure high-quality pellets that can provide accurate and precise analytical results in XRF analysis. The pressure applied to the sample should be sufficient to compress the sample completely and recrystallize the binder. It is important to experiment with your samples using increasing pressure until the intensity for the light elements reaches a maximum and stabilizes. Most samples will reach this maximum at 25-35T of pressure applied for 1-2 minutes. It's also important to release the pressure applied to a sample slowly to prevent cracking of the sample surface.
In conclusion, inadequate pressure during the pelletizing process can have a significant impact on the quality of the XRF pellet, which can affect the accuracy and precision of the analytical results. To ensure high-quality pellets and reliable analytical results, it is essential to optimize the pelletizing conditions, such as the applied pressure, to ensure that the sample is fully compressed and free from void spaces, cracks, or other structural defects.
Optimal Pressure Ranges for High-Quality Pellets
X-ray fluorescence (XRF) is a widely used analytical technique in laboratories to determine the elemental composition of a material. XRF pellet preparation is a crucial step in the process, as it directly affects the accuracy and precision of the analysis. One important factor that impacts the quality of XRF pellets is the pressure used during the preparation process.
Recommended Pressure Ranges for High-Quality Pellets
Optimal pressure ranges for high-quality pellets vary depending on the type of sample and equipment used. Generally, a pressure range of 15-25 tons is recommended for most samples, while more complex materials may require higher pressures up to 40 tons. However, exceeding these pressure ranges can cause damage to the sample, resulting in inaccurate or inconsistent results.
Factors Affecting Optimal Pressure Ranges
The optimal pressure range for a particular sample depends on several factors such as sample type, particle size, and binder type. Samples with larger particle sizes require higher pressures to ensure proper compaction, while smaller particles require lower pressures. Additionally, the type of binder used can impact the optimal pressure range, with some binders requiring higher pressures for proper compaction.
Importance of Using Optimal Pressure Ranges
It is important to note that the preparation of high-quality pellets not only improves the accuracy and precision of XRF analysis but also reduces the time and cost of sample preparation. Therefore, understanding the impact of pressure on XRF pellet quality and using the optimal pressure range is crucial in achieving reliable and reproducible results in elemental analysis.
The Role of XRF Pellet Die and Load
The XRF pellet die and load also play a significant role in determining the optimal pressure range for high-quality pellets. A high-quality stainless steel XRF pellet die with a perfectly flat and smooth pressing face is essential to ensure consistency and repeatability between samples. Additionally, the load needed for XRF pellet pressing varies depending on the sample type, with food samples requiring low loads of 2-4 tons and mineral ores requiring up to 40 tons.
Conclusion
In conclusion, the optimal pressure range for high-quality XRF pellets varies depending on several factors, including sample type, particle size, and binder type. It is essential to use the appropriate XRF pellet die and load to achieve the optimal pressure range and ensure consistency and repeatability between samples. By understanding the impact of pressure on XRF pellet quality and using the optimal pressure range, laboratories can achieve reliable and accurate results in elemental analysis.
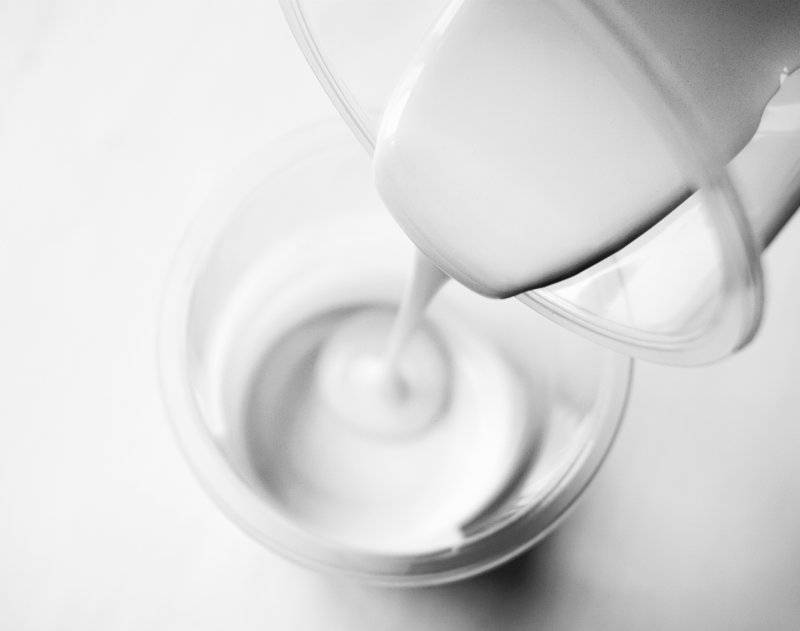
Importance of Consistency in Pressure Application
In XRF analysis, the quality of the sample pellet is paramount in achieving accurate and reliable results. One crucial factor that affects the quality of the pellet is the pressure applied during preparation. The consistency of the pressure application is vital in ensuring that the pellet's density is uniform, which is necessary for homogeneity in the sample and accuracy in the analysis. Inconsistency in pressure application can result in variations in pellet density, leading to differences in the sample's homogeneity and accuracy in the analysis.
Pressure Impact on Pellet Quality
The impact of pressure on pellet quality can be significant, particularly when dealing with heterogeneous samples. Different regions of the sample may respond differently to pressure changes, leading to non-uniform pellet density. Such variations in pellet density can have a significant impact on the accuracy and reproducibility of the analysis. Therefore, it is essential to maintain consistency in pressure application to ensure reliable and reproducible results in XRF analysis.
Achieving Consistency in Pressure Application
Consistency in pressure application can be achieved either by using automated pellet presses or by carefully controlling the pressure applied manually. Automated pellet presses offer a more reliable and consistent method of pressure application, while manual methods require careful attention to detail to achieve consistency. Regardless of the method used, it is essential to use high-quality equipment and materials to minimize sources of variability.
Effects of Inconsistent Pressure Application
Inconsistent pressure application can lead to several errors in XRF analysis. For instance, low-pressure application leads to the formation of loosely packed pellets, which can result in variations in the pellet's density. Such variations can lead to non-uniformity in the sample, resulting in inaccurate and unreliable analytical results. Conversely, high-pressure application can lead to the formation of overly dense pellets, which can cause cracking and breakage during analysis.
Conclusion
The importance of consistency in pressure application cannot be overstated in XRF analysis. It is critical to ensure that the pressure applied during pellet preparation is uniform to achieve accurate and reliable results. Inconsistent pressure application can lead to variations in pellet density, which can result in non-uniformity in the sample and inaccurate analysis. The use of high-quality equipment and materials, together with careful attention to detail, can help achieve consistency in pressure application and minimize sources of variability.
Conclusion: Pressure's Impact on XRF Pellet Quality
In summary, the pressure applied during the preparation of XRF pellets plays a crucial role in determining the quality of the final product. Inadequate pressure can result in poor pellet quality, leading to inaccurate and unreliable analytical results. Optimal pressure ranges are required to produce high-quality pellets consistently. Hence, it is crucial to ensure that the pressure applied during pellet preparation is consistent and within the recommended range. Only then can reliable and accurate analytical results be obtained, making pressure control a critical factor in XRF analysis.
CONTACT US FOR A FREE CONSULTATION
KINTEK LAB SOLUTION's products and services have been recognized by customers around the world. Our staff will be happy to assist with any inquiry you might have. Contact us for a free consultation and talk to a product specialist to find the most suitable solution for your application needs!