When comparing brazed joints and welded joints, the strength of the joint depends on several factors, including the materials being joined, the application, and the specific requirements of the joint. Brazing involves joining materials using a filler metal with a lower melting point than the base materials, while welding involves melting the base materials to create a fusion bond. Generally, welded joints are considered stronger due to the metallurgical bond formed between the base materials. However, brazed joints can offer advantages in specific scenarios, such as joining dissimilar materials or when heat distortion must be minimized. The choice between brazing and welding depends on the application's mechanical, thermal, and aesthetic requirements.
Key Points Explained:
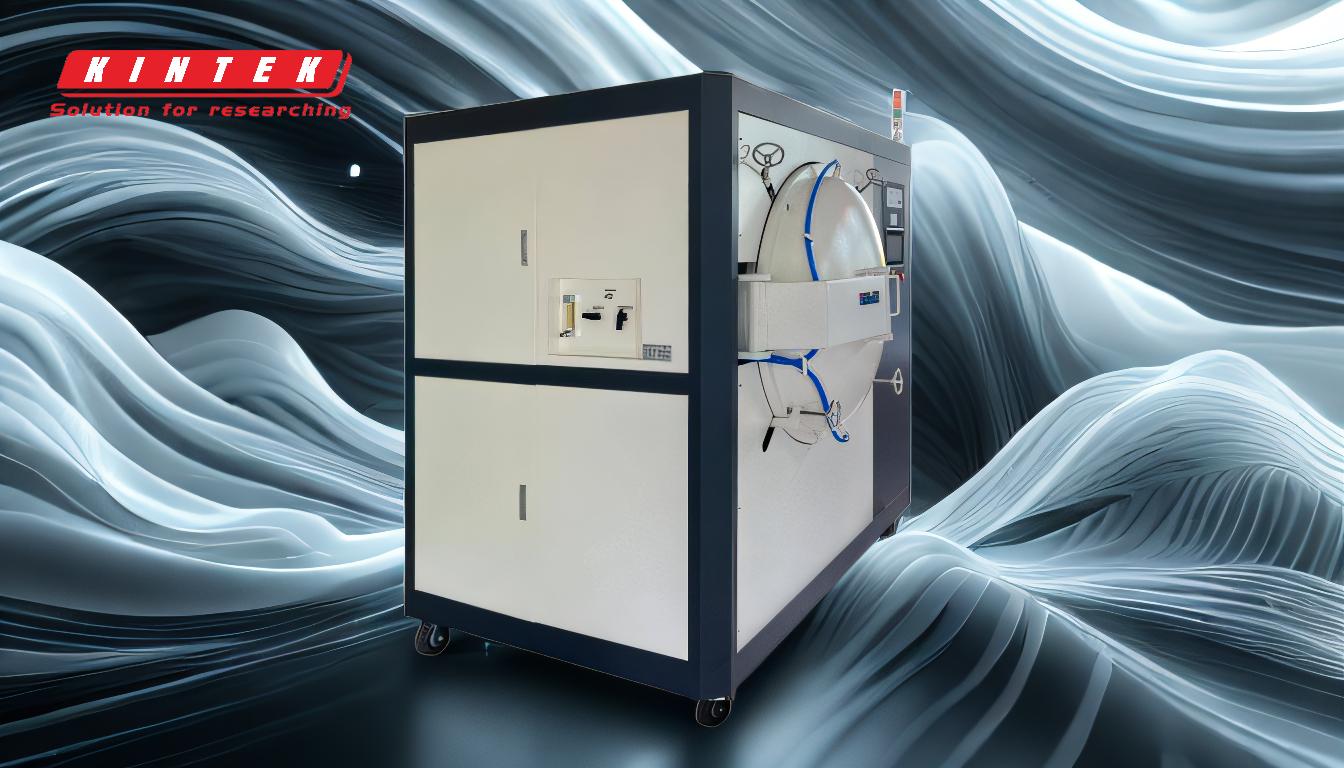
-
Definition and Process of Brazing and Welding:
- Brazing: A joining process that uses a filler metal with a melting point above 450°C (842°F) but below the melting point of the base materials. The filler metal flows into the joint by capillary action, creating a bond without melting the base materials.
- Welding: A process that involves melting the base materials to form a fusion bond. The molten materials solidify to create a joint that is often stronger than the base materials themselves.
-
Strength Comparison:
- Welded Joints: Typically stronger than brazed joints because the base materials are fused together, creating a metallurgical bond. This results in a joint with mechanical properties similar to or better than the base materials.
- Brazed Joints: Generally not as strong as welded joints because the bond relies on the adhesion of the filler metal to the base materials. However, brazed joints can still be strong enough for many applications, especially when designed correctly.
-
Advantages of Brazed Joints:
- Joining Dissimilar Materials: Brazing is ideal for joining materials with different melting points or thermal properties, such as metals and ceramics.
- Minimized Heat Distortion: Since brazing does not melt the base materials, it produces less heat distortion, making it suitable for precision components.
- Aesthetic Quality: Brazed joints often have a cleaner appearance, which is important in applications where aesthetics matter.
-
Advantages of Welded Joints:
- Higher Strength: Welded joints are generally stronger and more durable, making them suitable for high-stress applications.
- Better for Thick Materials: Welding is more effective for joining thick materials, as the fusion bond can penetrate deeper into the joint.
- No Need for Filler Metal: Welding does not require a filler metal, which can simplify the process in some cases.
-
Applications and Suitability:
- Brazing: Commonly used in industries like HVAC, electronics, and automotive for joining components that require precision and minimal heat distortion. It is also preferred for joining dissimilar materials.
- Welding: Widely used in construction, manufacturing, and heavy industries where high-strength joints are critical. It is also the preferred method for joining thick or large components.
-
Factors Influencing the Choice:
- Material Compatibility: The choice between brazing and welding often depends on the materials being joined. For example, brazing is better for joining metals with significantly different melting points.
- Joint Design: The design of the joint, including its geometry and load requirements, plays a significant role in determining the appropriate joining method.
- Thermal Considerations: If minimizing heat input is critical, brazing may be preferred. For applications requiring high thermal resistance, welding is usually the better option.
In conclusion, while welded joints are generally stronger, brazed joints offer unique advantages in specific applications. The choice between the two methods should be based on the materials, joint design, and application requirements. Both processes have their place in modern manufacturing and construction, and understanding their strengths and limitations is key to selecting the right method for a given task.
Summary Table:
Aspect | Brazed Joints | Welded Joints |
---|---|---|
Strength | Generally not as strong as welded joints, but sufficient for many applications. | Typically stronger due to a metallurgical bond between base materials. |
Process | Uses filler metal with a lower melting point; base materials do not melt. | Melts base materials to create a fusion bond. |
Advantages | Joins dissimilar materials, minimizes heat distortion, and offers a clean finish. | Higher strength, better for thick materials, and no filler metal required. |
Applications | HVAC, electronics, automotive, and precision components. | Construction, manufacturing, and heavy industries. |
Key Considerations | Material compatibility, joint design, and thermal requirements. | Material thickness, strength requirements, and thermal resistance. |
Still unsure which joining method is best for your project? Contact our experts today for personalized advice!