Yes, aluminum can be brazed, and there are several methods available to achieve this, each with its own advantages and considerations. Brazing aluminum involves joining two or more aluminum parts using a filler metal with a lower melting point than the base material. The process requires careful control of temperature and environment to ensure proper bonding and to prevent oxidation. Methods such as vacuum brazing, flame brazing, and furnace brazing are commonly used, with vacuum brazing being particularly advantageous due to its ability to prevent oxidation without the need for flux. Additionally, the type of aluminum alloy plays a significant role in determining the feasibility of brazing, as some alloys are more suitable than others.
Key Points Explained:
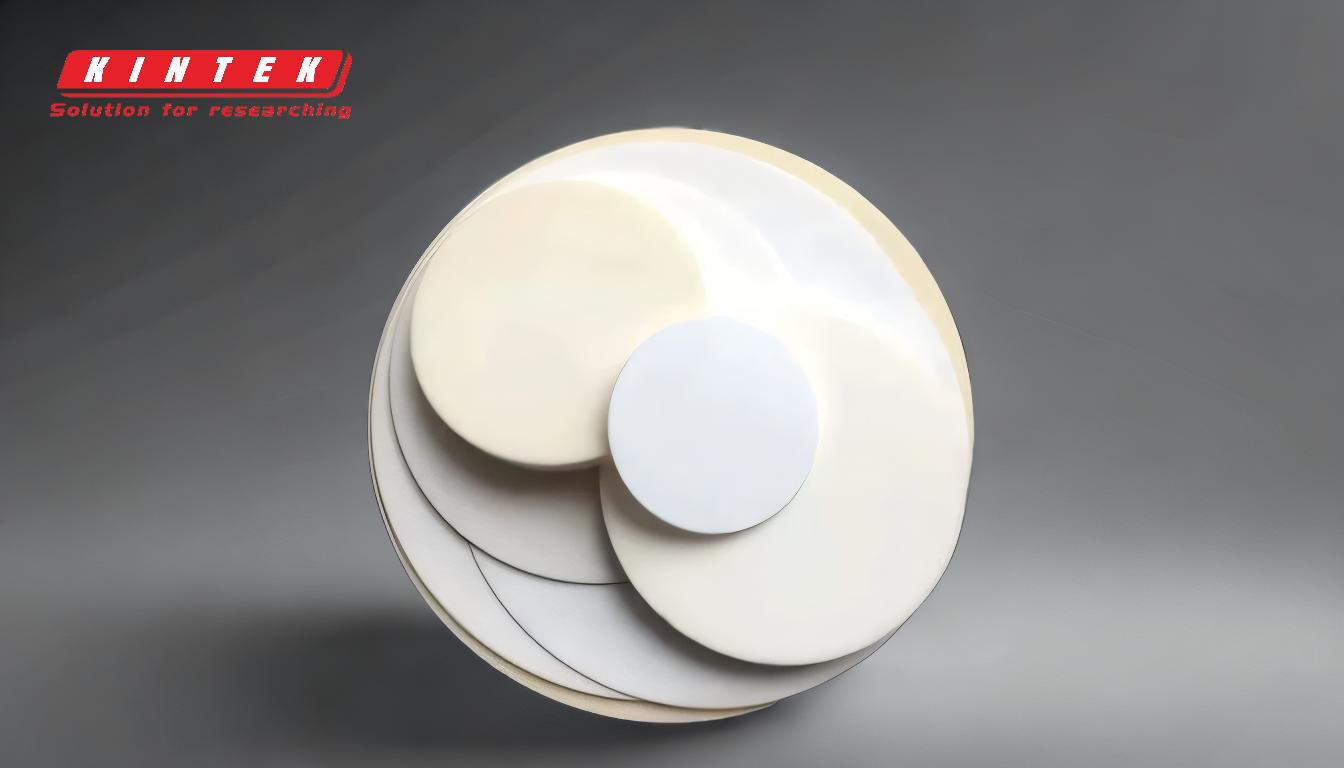
-
Brazing Methods for Aluminum:
- Vacuum Brazing: This method is highly effective for brazing aluminum because it prevents oxidation by maintaining a vacuum environment. The process relies on the difference in thermal expansion between aluminum and its oxide layer, causing the oxide layer to crack and allowing the filler metal to bond with the base material. Vacuum brazing does not require flux, which simplifies the process and avoids issues related to flux residue.
- Flame Brazing: This is a more traditional method where a flame is used to heat the aluminum parts and the filler metal. It is suitable for small-scale or manual operations but requires careful control to avoid overheating and oxidation.
- Furnace Brazing: This method is used for larger or more complex assemblies. It provides uniform heating and is suitable for joining a wide range of metals, including aluminum. Furnace brazing can be done in air, inert gas, or vacuum environments, depending on the requirements.
-
Advantages of Vacuum Brazing:
- No Flux Required: Vacuum brazing eliminates the need for flux, which simplifies the cleaning process before and after brazing. This also avoids issues such as slagging and residual flux, which can affect the corrosion resistance of the structure.
- High Productivity: The process is efficient and can be automated, making it suitable for high-volume production.
- Environmental Benefits: Since no flux is used, vacuum brazing aligns with environmental protection concepts by reducing the use of chemicals and minimizing waste.
-
Aluminum Alloys and Brazing Feasibility:
- Brazable Alloys: Non-hardenable alloys such as Series 1xxx, 3xxx, and 5xxx (with low magnesium content) and hardenable alloys like Series 6xxx are generally suitable for brazing. These alloys have melting points that are compatible with the brazing process.
- Non-Brazable Alloys: Series 2xxx and 7xxx alloys are typically not suitable for brazing due to their low melting points, which can lead to issues during the brazing process. However, under specific conditions, these alloys may still be brazed.
-
Challenges in Aluminum Brazing:
- Oxide Layer: Aluminum naturally forms an oxide layer that can interfere with the brazing process. In vacuum brazing, this layer is mechanically detached due to thermal expansion differences, but in other methods, flux or other techniques may be required to remove or penetrate the oxide layer.
- Temperature Control: Precise temperature control is essential to avoid melting the base material while ensuring the filler metal flows properly. Overheating can lead to distortion or weakening of the aluminum parts.
-
Applications of Aluminum Brazing:
- Automotive Industry: Aluminum brazing is widely used in the automotive industry for components such as heat exchangers, radiators, and air conditioning systems.
- Aerospace: The aerospace industry utilizes aluminum brazing for lightweight and high-strength components.
- Electronics: In electronics, aluminum brazing is used for heat sinks and other thermal management components.
In summary, aluminum can be successfully brazed using various methods, with vacuum brazing being particularly advantageous due to its ability to prevent oxidation and eliminate the need for flux. The choice of brazing method and the suitability of the aluminum alloy are critical factors in achieving a strong and durable joint.
Summary Table:
Aspect | Details |
---|---|
Brazing Methods | Vacuum, Flame, Furnace |
Advantages of Vacuum | No flux required, high productivity, environmental benefits |
Brazable Alloys | Series 1xxx, 3xxx, 5xxx (low Mg), 6xxx |
Non-Brazable Alloys | Series 2xxx, 7xxx (under specific conditions) |
Challenges | Oxide layer, precise temperature control |
Applications | Automotive, aerospace, electronics |
Need expert advice on aluminum brazing? Contact us today for tailored solutions!