Yes, ceramics can be sintered, and zirconia is a prime example of a ceramic material that undergoes sintering to achieve its final properties. Sintering is a critical process in ceramic manufacturing, where powder particles are consolidated by heating them to high temperatures below their melting point. This process reduces porosity, increases density, and enhances mechanical strength, resulting in a durable and high-performance material. Zirconia, in particular, is widely used in applications requiring high strength and toughness, such as dental prosthetics and industrial components. The sintering process for zirconia involves precise temperature control and specific phases—heating, sintering, and cooling—to ensure optimal results.
Key Points Explained:
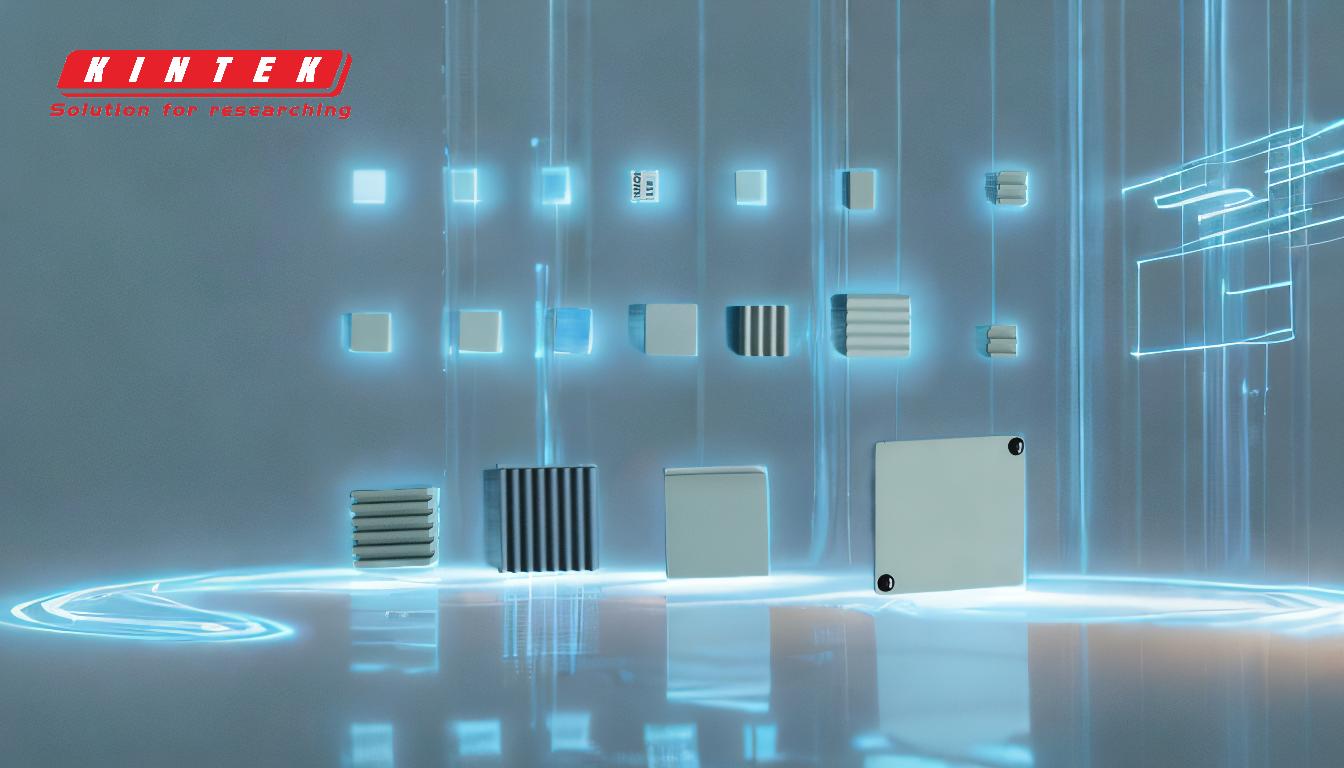
-
What is Sintering?
- Sintering is a manufacturing process used to consolidate ceramic powder particles by heating them to high temperatures below their melting point. This process involves material migration and grain boundary movement, leading to densification and the formation of a solid, durable mass. It is a key step in ceramic manufacturing, including zirconia production.
-
Why is Sintering Important for Ceramics?
- Sintering reduces porosity and increases the density of ceramic materials, enhancing their mechanical properties such as hardness, strength, and durability. For zirconia, sintering is essential to achieve its final hardness and structural integrity, making it suitable for demanding applications like dental crowns and industrial tools.
-
The Sintering Process for Zirconia:
- The sintering process for zirconia typically involves three phases:
- Heating Phase: The material is gradually heated to the sintering temperature.
- Sintering Phase: The material is held at a high temperature to allow particle diffusion and densification.
- Cooling Phase: The material is slowly cooled to room temperature to prevent cracking and ensure stability.
- During sintering, zirconia undergoes significant shrinkage, which must be carefully managed to achieve the desired final dimensions.
- The sintering process for zirconia typically involves three phases:
-
Role of a Zirconia Sintering Furnace:
- A zirconia sintering furnace is specifically designed to provide precise temperature control and uniform heating, which are critical for achieving consistent and high-quality results. These furnaces are equipped with advanced features to handle the unique requirements of zirconia sintering, such as controlled atmosphere and programmable temperature profiles.
-
Factors Influencing Sintering Success:
- Temperature Control: Precise temperature management is crucial to avoid defects like warping or cracking.
- Heating and Cooling Rates: Gradual heating and cooling help prevent thermal shock and ensure uniform densification.
- Atmosphere: The sintering environment (e.g., air, vacuum, or inert gas) can affect the final properties of the material.
- Material Quality: High-quality zirconia powder with consistent particle size and composition is essential for optimal sintering results.
-
Applications of Sintered Zirconia:
- Sintered zirconia is widely used in various industries due to its exceptional mechanical properties. Common applications include:
- Dental prosthetics (e.g., crowns, bridges, and implants).
- Industrial components (e.g., cutting tools, bearings, and valves).
- Biomedical devices (e.g., hip replacements and bone screws).
- Sintered zirconia is widely used in various industries due to its exceptional mechanical properties. Common applications include:
-
Best Practices for Sintering Zirconia:
- Always follow the manufacturer’s instructions for sintering zirconia to ensure optimal results.
- Use a high-quality zirconia sintering furnace with precise temperature control and uniform heating capabilities.
- Monitor the sintering process carefully to avoid defects and achieve the desired material properties.
In conclusion, sintering is a vital process for ceramics like zirconia, enabling the production of strong, dense, and durable materials. By understanding the principles of sintering and using specialized equipment like a zirconia sintering furnace, manufacturers can achieve consistent and high-quality results for a wide range of applications.
Summary Table:
Key Aspect | Details |
---|---|
What is Sintering? | Heating ceramic powders below melting point to reduce porosity and increase density. |
Importance for Ceramics | Enhances hardness, strength, and durability; critical for zirconia production. |
Sintering Phases | Heating, sintering (densification), and cooling phases. |
Role of Sintering Furnace | Provides precise temperature control and uniform heating for consistent results. |
Applications of Zirconia | Dental prosthetics, industrial tools, biomedical devices. |
Best Practices | Use high-quality furnaces, follow manufacturer guidelines, monitor process. |
Ready to achieve superior sintering results? Contact our experts today to learn more about zirconia sintering furnaces!