Yes, gold can be heated by induction. Induction heating is a highly efficient and controlled method for heating conductive materials like gold. It works by inducing eddy currents within the gold, which generate heat due to the material's electrical resistance. This process is widely used in industrial applications, including melting gold for jewelry making, refining, and creating alloys. Induction furnaces are particularly advantageous because they provide a fast, controlled, and energy-efficient heating process, significantly reducing the time required compared to conventional methods.
Key Points Explained:
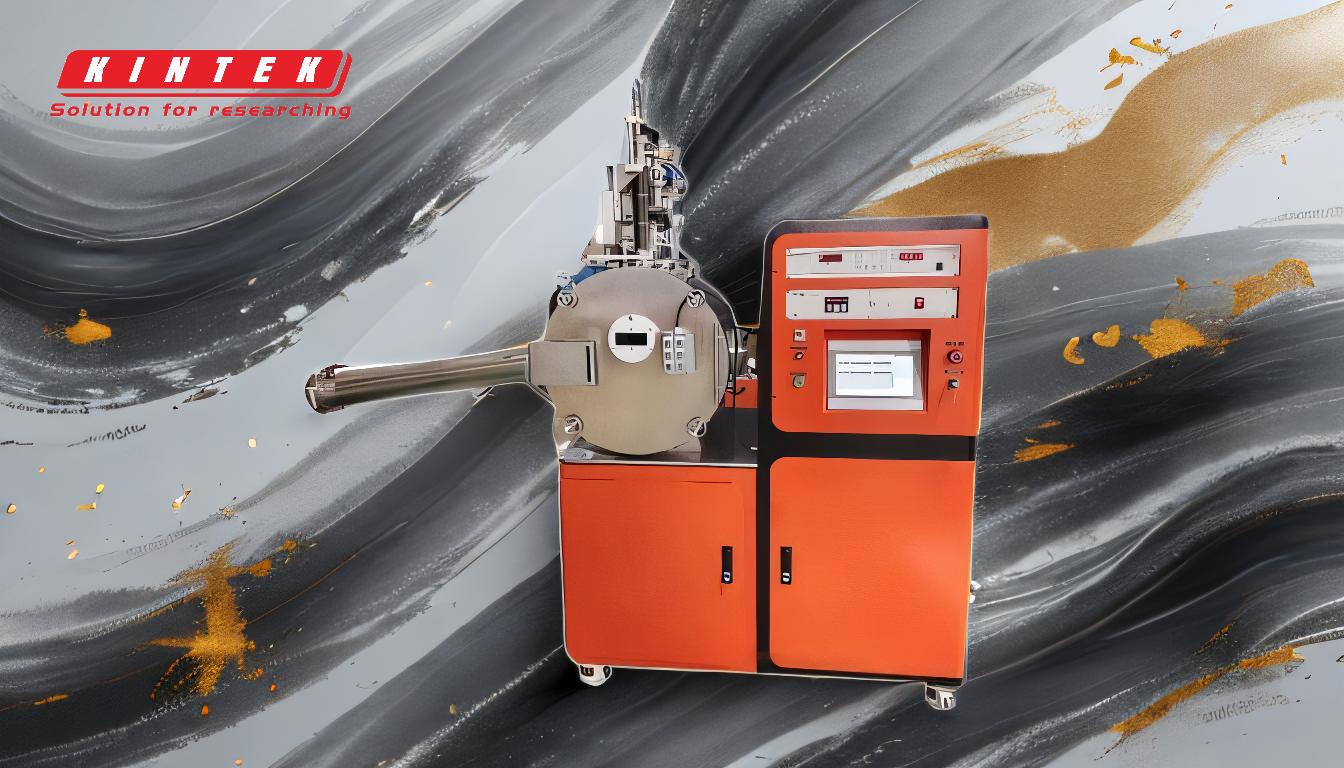
-
How Induction Heating Works:
- Induction heating relies on electromagnetic induction to generate heat in conductive materials.
- A high-frequency alternating current is passed through a coil, creating a rapidly alternating magnetic field.
- When gold (a conductive material) is placed within this magnetic field, eddy currents are induced within the gold.
- These eddy currents encounter electrical resistance, causing the gold to heat up due to Joule heating.
-
Advantages of Induction Heating for Gold:
- Speed: Induction furnaces can melt gold in just a few hours, whereas conventional methods may take a full day or longer.
- Control: The process is highly controllable, allowing precise temperature regulation, which is crucial for applications like jewelry making or alloy creation.
- Energy Efficiency: Induction heating is more energy-efficient than traditional methods because it directly heats the gold without significant heat loss to the surroundings.
- Cleanliness: Since induction heating does not require direct contact with a flame or heating element, it reduces contamination risks, making it ideal for refining high-purity gold.
-
Applications of Induction Heating for Gold:
- Melting and Casting: Induction furnaces are commonly used to melt gold for casting into jewelry, bars, or other forms.
- Refining: The precise temperature control of induction heating makes it suitable for refining gold to remove impurities.
- Alloy Creation: Induction heating is used to create gold alloys by melting and mixing gold with other metals under controlled conditions.
-
Comparison with Conventional Heating Methods:
- Conventional methods, such as gas or electric resistance furnaces, rely on external heat sources to transfer heat to the gold.
- These methods are slower and less efficient because they involve heat transfer through conduction, convection, or radiation, which can result in energy loss.
- Induction heating, on the other hand, directly heats the gold from within, making it faster and more efficient.
-
Practical Considerations:
- Equipment: Induction furnaces are specifically designed for heating conductive materials like gold. They consist of a power supply, an induction coil, and a crucible to hold the gold.
- Frequency Selection: The frequency of the alternating current affects the depth of heating. Higher frequencies are typically used for smaller pieces of gold, while lower frequencies are suitable for larger volumes.
- Safety: Induction heating is generally safer than open-flame methods, as it reduces the risk of burns and fire hazards. However, proper handling of molten gold is still essential.
In summary, induction heating is a highly effective method for heating gold, offering significant advantages in terms of speed, control, and energy efficiency. It is widely used in industries that require precise and efficient heating of gold, such as jewelry making, refining, and alloy production.
Summary Table:
Aspect | Details |
---|---|
How It Works | Electromagnetic induction creates eddy currents, heating gold via resistance. |
Advantages | Fast, precise, energy-efficient, and clean heating process. |
Applications | Melting, refining, and creating gold alloys. |
Comparison to Conventional Methods | Faster and more efficient than gas or electric resistance furnaces. |
Practical Considerations | Requires induction furnace, frequency selection, and safety precautions. |
Discover how induction heating can transform your gold processing—contact our experts today!