Yes, PVD (Physical Vapor Deposition) can be done on aluminium. PVD is a versatile coating process that can be applied to a wide range of materials, including metals, ceramics, and polymers. Aluminium, being a lightweight and corrosion-resistant metal, is a suitable candidate for PVD coatings. The process enhances the surface properties of aluminium, making it more durable, scratch-resistant, and corrosion-resistant. PVD coatings on aluminium are particularly beneficial in applications where the material is exposed to harsh environments, such as coastal areas or industrial settings.
Key Points Explained:
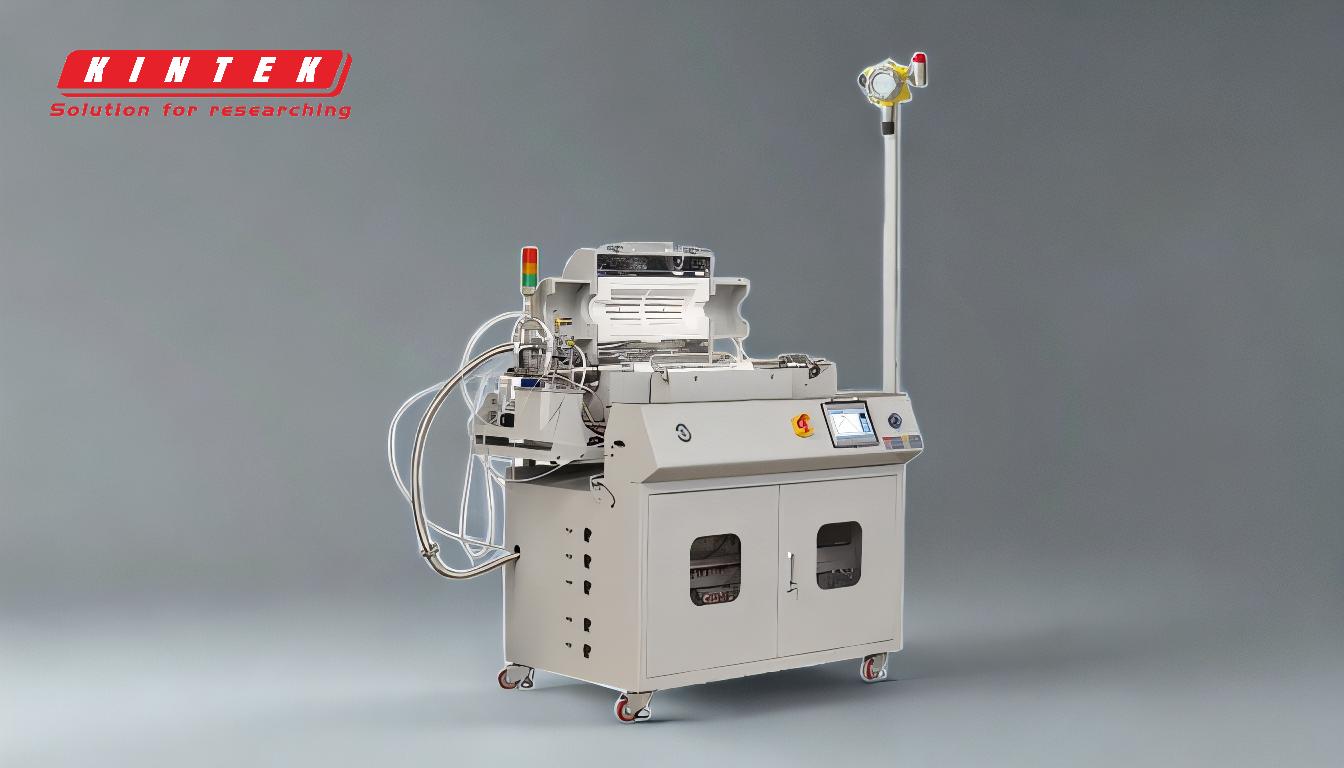
-
Compatibility of PVD with Aluminium:
- PVD is compatible with a wide range of materials, including aluminium. The process involves depositing a thin layer of metal or ceramic onto the surface of the substrate, which in this case is aluminium. This thin layer enhances the surface properties of the aluminium, making it more durable and resistant to wear and tear.
-
Enhanced Durability:
- PVD coatings are known for their hardness, often being four times harder than chrome. When applied to aluminium, this hardness significantly increases the material's resistance to scratches and abrasions. This makes PVD-coated aluminium ideal for applications where the material is subjected to mechanical stress or harsh environmental conditions.
-
Corrosion Resistance:
- Aluminium is already known for its natural corrosion resistance, but PVD coatings can further enhance this property. The thin layer of PVD coating acts as a barrier, protecting the aluminium from corrosive elements such as saltwater, acids, and other chemicals. This is particularly beneficial for applications in coastal areas or industries where exposure to corrosive substances is common.
-
Aesthetic Value:
- PVD coatings can replicate the original finish of materials with minimal effort. This means that aluminium can be coated with PVD to achieve a variety of finishes, including metallic, matte, or even colored finishes, without compromising the material's inherent properties. This makes PVD-coated aluminium suitable for both functional and decorative applications.
-
Environmental Friendliness:
- PVD is an environmentally friendly process. Unlike traditional electroplating, which often involves the use of harmful chemicals, PVD is a cleaner process that does not produce hazardous waste. This makes PVD-coated aluminium a more sustainable option for industries looking to reduce their environmental impact.
-
Uniform Coating:
- One of the key advantages of PVD is its ability to provide a uniform coating. This ensures that the entire surface of the aluminium is evenly coated, which is crucial for maintaining consistent performance and appearance. Uniformity is particularly important in applications where the material is exposed to varying environmental conditions.
-
Low Maintenance:
- PVD-coated aluminium requires minimal maintenance. The durability and corrosion resistance of the coating mean that the material is less likely to degrade over time, reducing the need for frequent repairs or replacements. This makes PVD-coated aluminium a cost-effective solution in the long run.
-
Application in Harsh Environments:
- Given its enhanced durability and corrosion resistance, PVD-coated aluminium is well-suited for use in harsh environments. Whether it's in marine applications, automotive components, or industrial machinery, PVD-coated aluminium can withstand the rigors of these environments better than untreated aluminium.
-
Increased Lifespan:
- PVD coatings can significantly increase the lifespan of aluminium components. By creating a hard, durable layer that bonds to the surface of the aluminium, PVD coatings protect the material from wear and tear, extending its useful life by up to ten times in some cases.
-
Customizable Properties:
- The properties of PVD coatings can be tailored to meet specific requirements. For example, coatings can be designed to increase hardness, improve fatigue resistance, or enhance thermal stability. This flexibility allows for the customization of PVD-coated aluminium to suit a wide range of applications.
In summary, PVD can be effectively applied to aluminium to enhance its surface properties, making it more durable, corrosion-resistant, and aesthetically versatile. The process is environmentally friendly, provides a uniform coating, and requires low maintenance, making it an ideal choice for a variety of industrial and decorative applications.
Summary Table:
Key Benefits of PVD on Aluminium | Details |
---|---|
Compatibility | PVD is compatible with aluminium, enhancing its surface properties. |
Durability | Increases resistance to scratches and abrasions. |
Corrosion Resistance | Protects against saltwater, acids, and chemicals. |
Aesthetic Value | Offers metallic, matte, or colored finishes. |
Environmental Friendliness | Cleaner process with no hazardous waste. |
Uniform Coating | Ensures consistent performance and appearance. |
Low Maintenance | Reduces need for frequent repairs or replacements. |
Harsh Environment Suitability | Ideal for marine, automotive, and industrial use. |
Increased Lifespan | Extends material lifespan up to ten times. |
Customizable Properties | Tailored coatings for specific application needs. |
Upgrade your aluminium components with PVD coatings—contact us today to learn more!