PVD (Physical Vapor Deposition) coatings are highly durable and resistant to wear, corrosion, and high temperatures, making them ideal for demanding applications. However, due to their thinness (0.5–5 microns) and strong adhesion to the substrate, repairing a damaged PVD coating is challenging. In most cases, the coating cannot be repaired in situ; instead, the damaged coating must be stripped, and the substrate re-coated. The process involves specialized equipment and expertise, making it more practical to replace or re-coat the component entirely. While PVD coatings are not easily repairable, their durability often minimizes the need for frequent maintenance or repairs.
Key Points Explained:
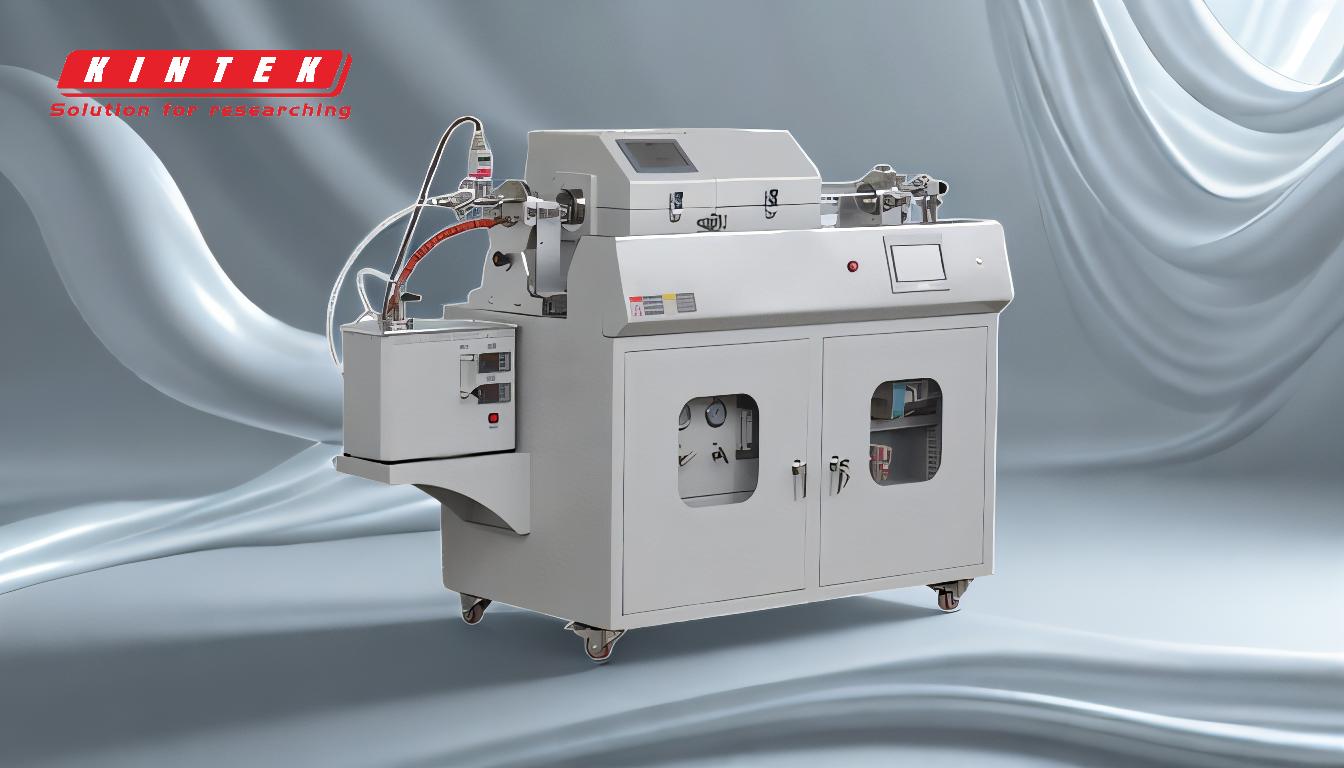
-
PVD Coating Durability and Challenges in Repair
- PVD coatings are known for their high hardness, wear resistance, and strong adhesion to the substrate.
- Their thinness (0.5–5 microns) and uniform application make them difficult to repair locally.
- Damaged areas often require complete stripping and re-coating rather than spot repairs.
-
Repair Process for PVD Coatings
- Stripping the Coating: The damaged PVD coating must be removed entirely using chemical or mechanical methods. This process requires specialized equipment and expertise to avoid damaging the substrate.
- Surface Preparation: After stripping, the substrate must be thoroughly cleaned and prepared to ensure proper adhesion of the new coating.
- Re-coating: The component is then re-coated using the PVD process, which involves high-vacuum conditions and precise control of temperature and deposition parameters.
-
Practical Considerations for Repair
- Cost and Time: The repair process can be costly and time-consuming, often making it more practical to replace the component entirely.
- Equipment and Expertise: Stripping and re-coating require specialized facilities and skilled technicians, which may not be readily available.
- Component Suitability: Not all components are suitable for re-coating, especially if the substrate has been compromised during use or the stripping process.
-
Alternatives to Repair
- Replacement: In many cases, replacing the damaged component is more cost-effective than attempting to repair the PVD coating.
- Preventive Maintenance: Regular inspection and maintenance can help extend the life of PVD-coated components, reducing the need for repairs.
-
Applications Where Repair is Rarely Needed
- PVD coatings are often used in applications where their durability minimizes the need for repairs, such as in automotive, aerospace, and medical industries.
- The high wear and corrosion resistance of PVD coatings ensure long service life, even in harsh environments.
In summary, while PVD coatings are not easily repairable due to their thinness and strong adhesion, their inherent durability often reduces the need for frequent repairs. When repair is necessary, it typically involves stripping and re-coating the entire component, a process that requires specialized equipment and expertise. For many applications, replacement or preventive maintenance may be more practical solutions.
Summary Table:
Key Aspect | Details |
---|---|
PVD Coating Durability | High hardness, wear resistance, and strong adhesion to substrates. |
Repair Challenges | Thinness (0.5–5 microns) and strong adhesion make local repairs difficult. |
Repair Process | Stripping, surface preparation, and re-coating with specialized equipment. |
Practical Considerations | Costly, time-consuming, and requires expertise; replacement may be better. |
Alternatives to Repair | Replacement or preventive maintenance to extend component life. |
Applications | Automotive, aerospace, and medical industries with minimal repair needs. |
Need help with PVD coatings or repairs? Contact our experts today for tailored solutions!