Stainless steel can indeed be annealed, and the process is often tailored to meet specific performance requirements, particularly when it comes to the microstructure and properties of the material after annealing. Bright annealing, a specialized form of annealing, is commonly used for stainless steel tubes to achieve a clean, oxide-free surface while improving mechanical properties. The process involves heating the stainless steel to a specific temperature, holding it for a period, and then cooling it in a controlled environment, often using inert gases like nitrogen or hydrogen to prevent oxidation. The exact parameters of the annealing process, such as temperature, holding time, and cooling rate, vary depending on the type of stainless steel and the desired microstructure. For instance, austenitic stainless steels are typically annealed at higher temperatures to dissolve carbides and ensure a uniform microstructure, while martensitic stainless steels may require lower temperatures to achieve the desired hardness and strength. The choice of annealing process is critical to achieving the desired mechanical properties, corrosion resistance, and surface finish.
Key Points Explained:
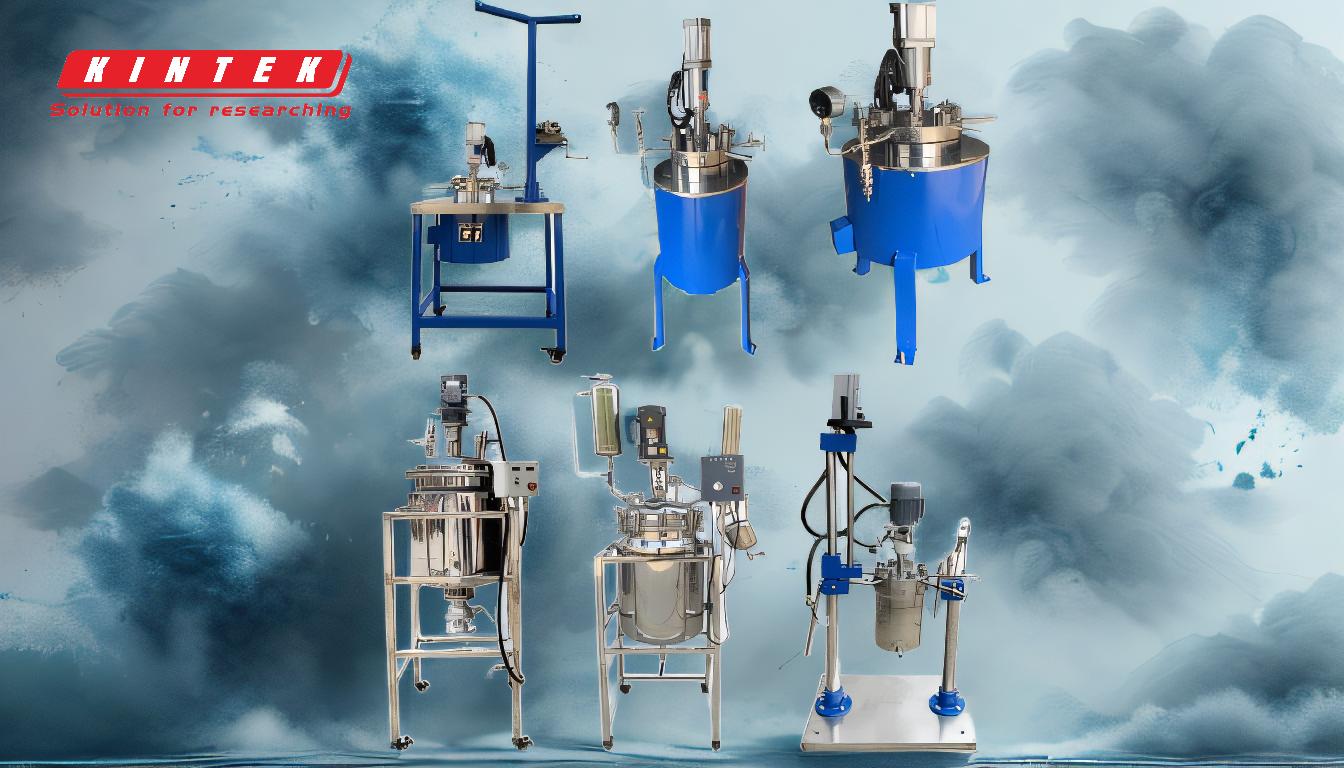
-
What is Annealing?
- Annealing is a heat treatment process that involves heating a material to a specific temperature, holding it at that temperature for a certain period, and then cooling it slowly. This process relieves internal stresses, softens the material, and improves its ductility and machinability. For stainless steel, annealing is essential to achieve the desired mechanical properties and microstructure.
-
Bright Annealing for Stainless Steel
- Bright annealing is a specialized form of annealing used for stainless steel, particularly for tubes and other components where a clean, oxide-free surface is required. The process involves heating the stainless steel in a controlled atmosphere, typically using inert gases like nitrogen or hydrogen, to prevent oxidation. This results in a bright, shiny surface finish while also improving the material's mechanical properties.
-
Importance of Microstructure in Annealing
- The microstructure of stainless steel after annealing is critical to its performance. Different types of stainless steel, such as austenitic, ferritic, and martensitic, have different microstructural requirements. For example, austenitic stainless steels are annealed at higher temperatures to dissolve carbides and achieve a uniform microstructure, while martensitic stainless steels may require lower temperatures to achieve the desired hardness and strength.
-
Variations in Bright Heat Treatment Process
- The bright heat treatment process can vary depending on the specific requirements of the stainless steel tube. Factors such as the type of stainless steel, the desired mechanical properties, and the required surface finish all influence the annealing parameters. For instance, the temperature, holding time, and cooling rate may be adjusted to achieve the desired microstructure and properties.
-
Controlled Atmosphere in Bright Annealing
- The use of a controlled atmosphere, such as nitrogen or hydrogen, is essential in bright annealing to prevent oxidation and achieve a clean, oxide-free surface. The choice of atmosphere depends on the type of stainless steel and the desired surface finish. For example, hydrogen is often used for its reducing properties, which help to remove any existing oxides and prevent the formation of new ones.
-
Applications of Annealed Stainless Steel
- Annealed stainless steel is used in a wide range of applications where high corrosion resistance, strength, and a clean surface finish are required. Common applications include medical devices, food processing equipment, and automotive components. The annealing process ensures that the stainless steel meets the necessary performance requirements for these applications.
-
Challenges in Annealing Stainless Steel
- One of the challenges in annealing stainless steel is achieving the desired microstructure and properties while maintaining a clean surface finish. The process requires precise control of temperature, holding time, and cooling rate, as well as the use of a controlled atmosphere to prevent oxidation. Any deviation from the optimal parameters can result in a suboptimal microstructure or surface finish.
In conclusion, stainless steel can be annealed, and the process is often tailored to meet specific performance requirements, particularly when it comes to the microstructure and properties of the material after annealing. Bright annealing, in particular, is a specialized process used to achieve a clean, oxide-free surface while improving mechanical properties. The choice of annealing process and parameters is critical to achieving the desired performance characteristics for various applications.
Summary Table:
Key Aspect | Details |
---|---|
What is Annealing? | Heat treatment to relieve stress, soften, and improve ductility. |
Bright Annealing | Uses inert gases for a clean, oxide-free surface and enhanced properties. |
Microstructure Importance | Tailored for austenitic, ferritic, and martensitic stainless steels. |
Controlled Atmosphere | Nitrogen or hydrogen prevents oxidation during bright annealing. |
Applications | Medical devices, food processing, automotive components, and more. |
Challenges | Precise control of temperature, time, and cooling rate is critical. |
Unlock the potential of stainless steel annealing for your applications—contact our experts today!