Yes, vacuum gauges can be calibrated, and it is a critical process to ensure accurate pressure measurements in various applications. Calibration involves comparing the gauge's readings to a known standard or reference and adjusting it to minimize discrepancies. This process is essential because vacuum gauges, like all measuring instruments, can drift over time due to wear, environmental factors, or mechanical stress. Proper calibration ensures reliable performance, maintains system efficiency, and prevents issues such as leaks or insufficient vacuum levels.
Key Points Explained:
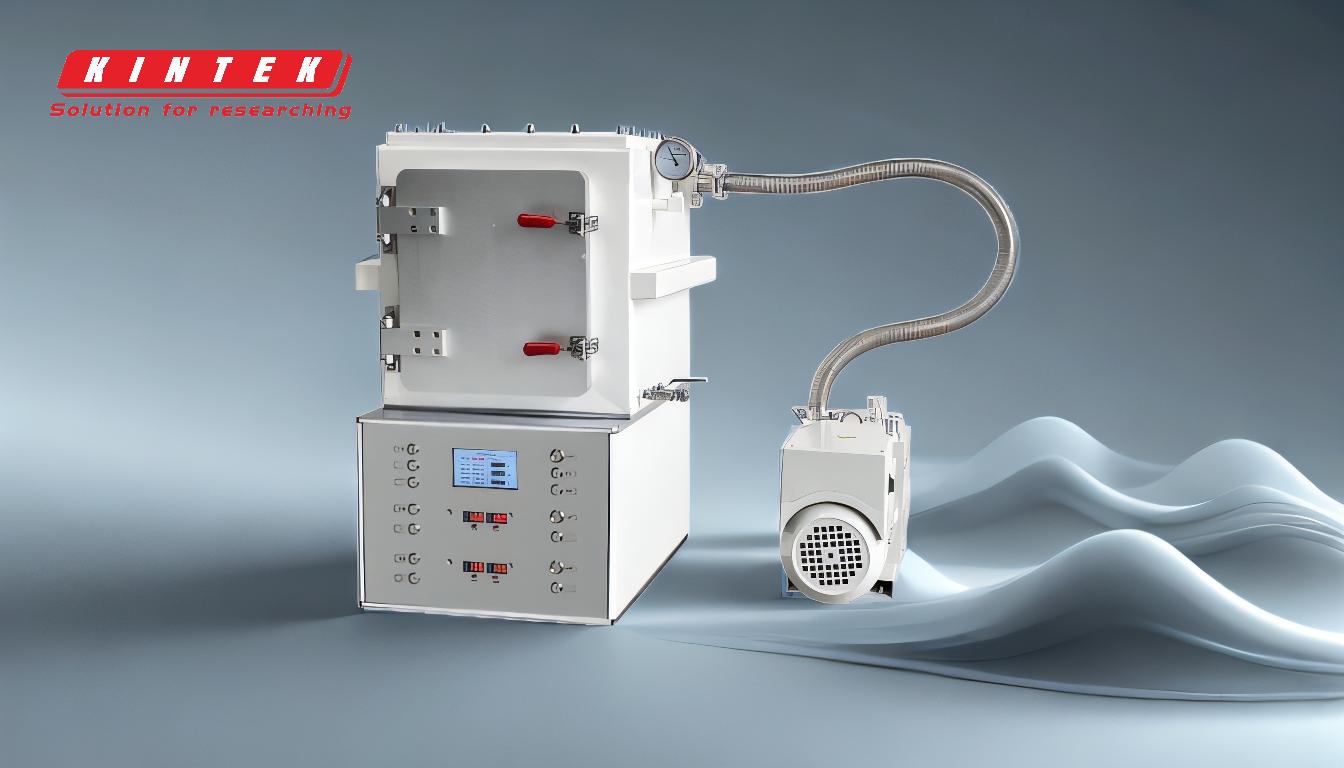
-
Importance of Calibrating a Vacuum Gauge
- Vacuum gauges are used to measure pressure levels in systems where a vacuum is required, such as in laboratories, manufacturing, or HVAC systems.
- Over time, the accuracy of a vacuum gauge can degrade due to factors like mechanical wear, temperature fluctuations, or contamination.
- Calibration ensures the gauge provides accurate readings, which is critical for maintaining system performance, safety, and efficiency.
-
How Vacuum Gauge Calibration Works
- Calibration involves comparing the gauge's readings to a known standard, such as a primary or secondary reference gauge.
- The process typically includes:
- Placing the gauge in a controlled environment with a stable vacuum level.
- Measuring the pressure using the reference standard.
- Adjusting the gauge to match the reference readings or documenting the deviation for correction in data analysis.
- Calibration can be performed manually or using automated systems, depending on the gauge type and application.
-
Types of Vacuum Gauges and Their Calibration Methods
- Different types of vacuum gauges require specific calibration techniques:
- Mechanical Gauges (e.g., Bourdon Tube Gauges): These are calibrated using pressure comparators or deadweight testers.
- Thermocouple and Pirani Gauges: These measure pressure based on thermal conductivity and require calibration using a known gas and reference pressure.
- Ionization Gauges: These are calibrated using high-vacuum standards and often require specialized equipment.
- The calibration method depends on the gauge's operating principle and the pressure range it measures.
- Different types of vacuum gauges require specific calibration techniques:
-
When to Calibrate a Vacuum Gauge
- Regular calibration is recommended to maintain accuracy. The frequency depends on:
- The gauge's usage intensity and operating conditions.
- Manufacturer recommendations (typically annually or biannually).
- Industry standards or regulatory requirements.
- Immediate calibration is necessary if the gauge shows signs of inaccuracy, such as inconsistent readings or after exposure to extreme conditions.
- Regular calibration is recommended to maintain accuracy. The frequency depends on:
-
Benefits of Calibrating a Vacuum Gauge
- Improved Accuracy: Ensures the gauge provides reliable pressure measurements, which is critical for process control and quality assurance.
- Prevention of System Failures: Accurate readings help detect issues like leaks or pump inefficiencies early, preventing costly downtime.
- Compliance with Standards: Many industries, such as pharmaceuticals or aerospace, require regular calibration to meet regulatory standards.
- Extended Equipment Lifespan: Proper calibration reduces wear and tear on the gauge and associated systems.
-
Challenges in Vacuum Gauge Calibration
- Environmental Factors: Temperature, humidity, and vibrations can affect calibration accuracy.
- Complexity of High-Vacuum Systems: Calibrating gauges for high-vacuum applications often requires specialized equipment and expertise.
- Cost and Downtime: Regular calibration can be time-consuming and may require system shutdowns, impacting productivity.
-
Best Practices for Vacuum Gauge Calibration
- Use certified reference standards and calibration equipment.
- Follow manufacturer guidelines for calibration procedures and intervals.
- Document calibration results and maintain a calibration log for traceability.
- Train personnel on proper calibration techniques to ensure consistency and accuracy.
By adhering to these practices, users can ensure their vacuum gauges remain accurate and reliable, supporting optimal system performance and compliance with industry standards.
Summary Table:
Key Aspect | Details |
---|---|
Importance | Ensures accurate pressure measurements, system safety, and efficiency. |
Calibration Process | Compares gauge readings to a known standard and adjusts for accuracy. |
Types of Gauges | Mechanical, Thermocouple, Pirani, Ionization—each requires specific methods. |
When to Calibrate | Annually, biannually, or after exposure to extreme conditions. |
Benefits | Improved accuracy, system reliability, compliance, and extended lifespan. |
Challenges | Environmental factors, high-vacuum complexity, cost, and downtime. |
Best Practices | Use certified standards, follow guidelines, document results, and train staff. |
Ensure your vacuum gauges are accurate and reliable—contact our experts today for calibration solutions!