Yes, you can melt copper in an induction furnace. Induction furnaces are highly efficient for melting metals like copper due to their ability to generate high temperatures quickly and maintain precise control over the melting process. The furnace's design, which includes a power supply, induction ring, and refractory crucible, ensures that the copper is heated uniformly and efficiently. Additionally, the use of an IGBT induction furnace enhances the process by providing better energy efficiency and control. Proper maintenance and adherence to safety protocols, such as ensuring a clean environment and secure electrical connections, are crucial for optimal performance and safety.
Key Points Explained:
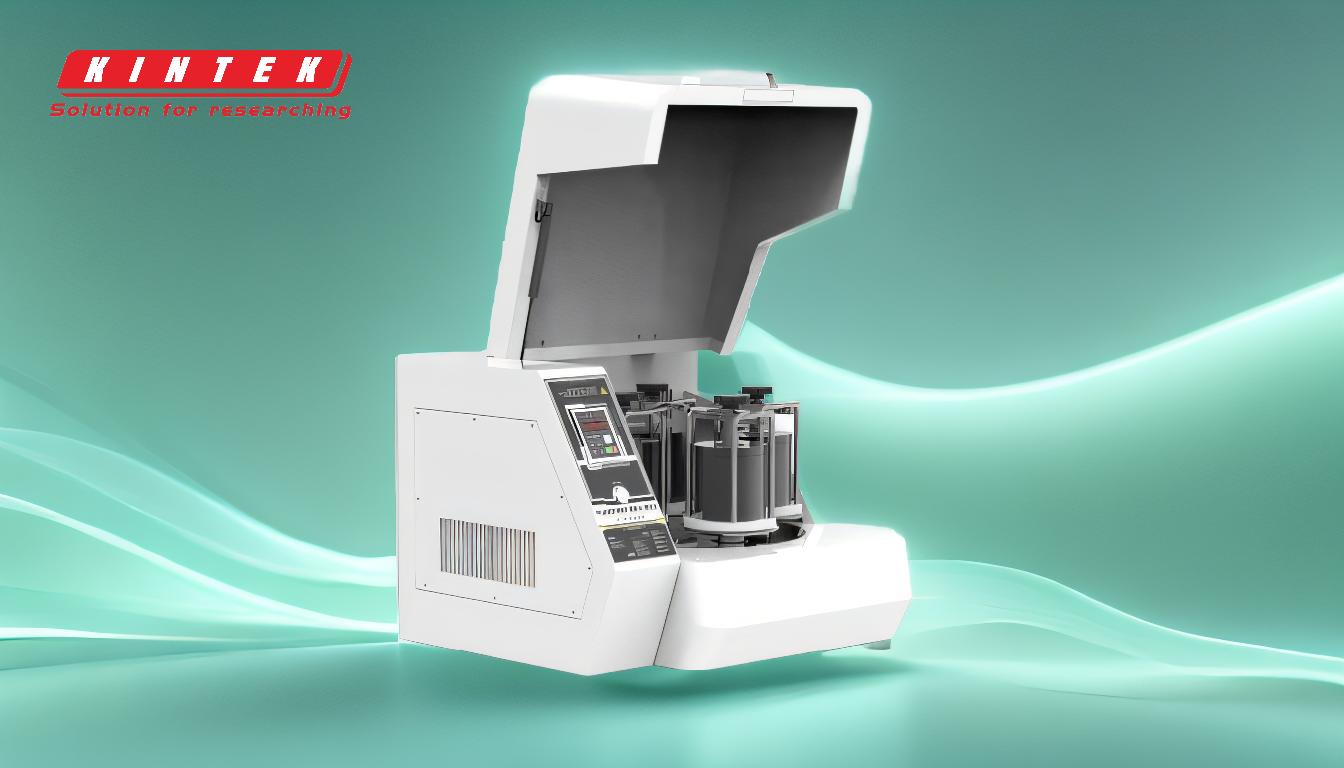
-
Induction Furnace Components:
- Power Supply: Provides the necessary electrical energy to generate the magnetic field.
- Induction Ring: Creates the alternating magnetic field that induces eddy currents in the metal.
- Crucible: Made of refractory materials, it holds the metal charge and withstands high temperatures.
-
Melting Process:
- Temperature Control: Induction furnaces can reach and maintain the high temperatures required to melt copper (approximately 1085°C).
- Uniform Heating: The induced eddy currents ensure that the copper is heated uniformly, preventing hot spots and ensuring consistent melting.
-
Safety and Maintenance:
- Clean Environment: Keeping the furnace room clean and free from flammable materials is essential to prevent accidents.
- Electrical Safety: Ensuring secure electrical connections and avoiding contact with live parts when the machine is powered on is critical.
- Crucible Maintenance: Promptly repairing any damage to the crucible and preventing the incorporation of iron filings and iron oxide helps maintain the crucible's integrity and performance.
-
Advantages of Using an IGBT Induction Furnace:
- Energy Efficiency: IGBT technology provides better energy efficiency, reducing operational costs.
- Precise Control: Enhanced control over the melting process allows for better quality and consistency in the melted copper.
- Durability: IGBT induction furnaces are known for their durability and reliability, making them suitable for continuous industrial use.
-
Factors Influencing the Melting Process:
- Temperature: High and consistent temperatures are necessary for efficient melting.
- Pressure: Atmospheric pressure can affect the melting point and process.
- Impurities: The presence of impurities can alter the melting characteristics and quality of the copper.
- Slags and Oxidants: These can affect the purity and properties of the melted copper, necessitating careful management during the melting process.
By understanding these key points, you can effectively use an induction furnace to melt copper, ensuring high-quality results while maintaining safety and efficiency.
Summary Table:
Key Aspect | Details |
---|---|
Components | Power supply, induction ring, refractory crucible |
Melting Process | High temperatures (~1085°C), uniform heating, no hot spots |
Safety & Maintenance | Clean environment, secure electrical connections, crucible maintenance |
IGBT Induction Furnace | Energy efficiency, precise control, durability |
Influencing Factors | Temperature, pressure, impurities, slags, and oxidants |
Ready to melt copper efficiently? Contact us today to learn more about induction furnaces!