Heating elements, like all components subjected to thermal stress and electrical load, do degrade over time. This degradation is influenced by factors such as material composition, operating temperature, environmental conditions, and usage patterns. Over time, heating elements may experience oxidation, embrittlement, or changes in resistance, leading to reduced efficiency or failure. Understanding the mechanisms of degradation and implementing proper maintenance can extend their lifespan. Below, we explore the key reasons for degradation, signs of wear, and strategies to mitigate it.
Key Points Explained:
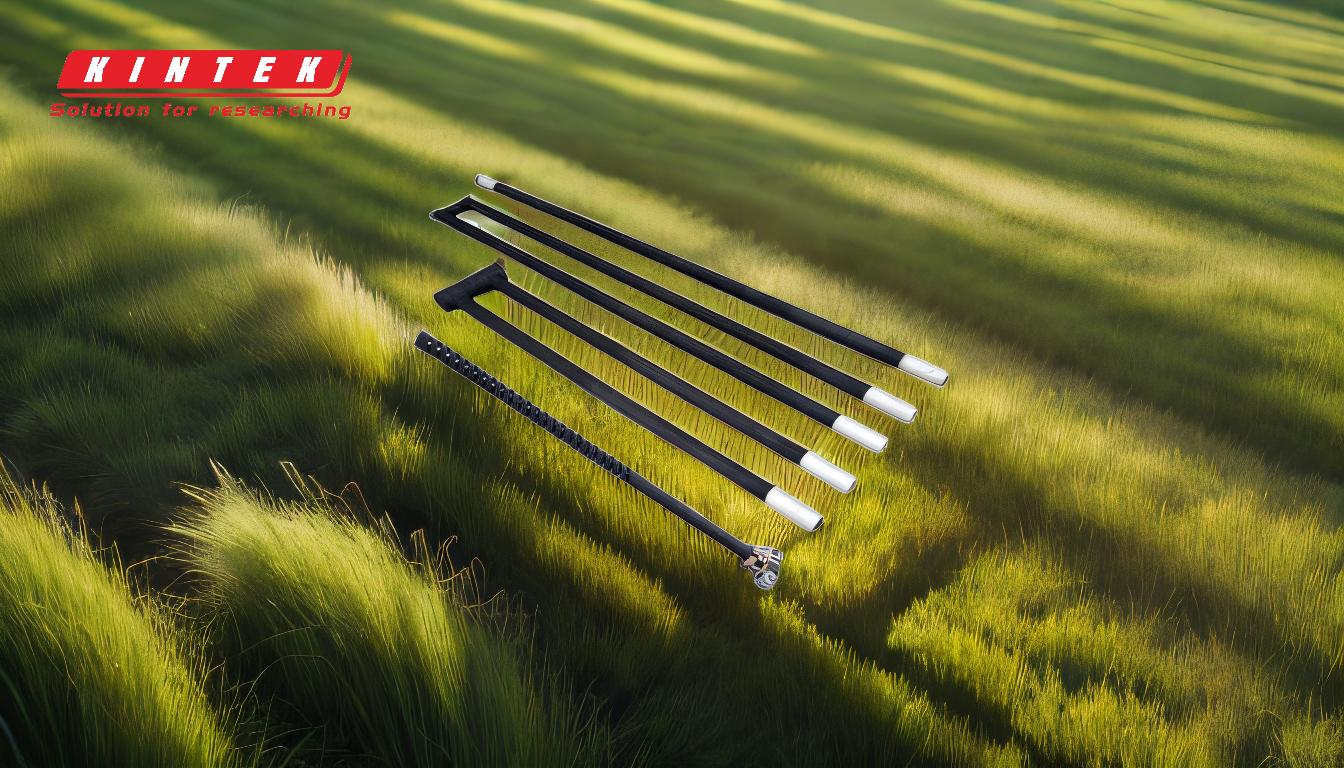
-
Mechanisms of Degradation
Heating elements degrade due to several physical and chemical processes:- Oxidation: At high temperatures, the metal in heating elements reacts with oxygen, forming oxides that can weaken the structure. For example, nickel-chromium alloys oxidize over time, leading to thinning and eventual failure.
- Embrittlement: Repeated heating and cooling cycles cause thermal fatigue, making the material brittle and prone to cracking.
- Resistance Changes: Over time, the electrical resistance of the element may increase due to material changes, reducing its efficiency.
- Contamination: Exposure to corrosive substances or moisture can accelerate degradation.
-
Signs of Degradation
- Reduced Heating Efficiency: If the element takes longer to reach the desired temperature, it may indicate wear.
- Visible Damage: Cracks, discoloration, or warping are clear signs of degradation.
- Inconsistent Performance: Hot spots or uneven heating suggest localized wear.
- Electrical Issues: Frequent tripping of circuit breakers or blown fuses may indicate a failing element.
-
Factors Influencing Degradation
- Material Quality: High-quality materials like nickel-chromium or iron-chromium-aluminum alloys resist degradation better than cheaper alternatives.
- Operating Temperature: Higher temperatures accelerate oxidation and thermal fatigue.
- Usage Frequency: Frequent on-off cycles increase thermal stress.
- Environmental Conditions: Exposure to moisture, chemicals, or abrasive particles can shorten lifespan.
-
Mitigation Strategies
- Proper Sizing: Ensure the heating element is appropriately sized for the application to avoid overloading.
- Regular Maintenance: Clean the element and inspect for signs of wear periodically.
- Temperature Control: Avoid exceeding the recommended operating temperature.
- Protective Coatings: Use coatings or shields to protect against corrosive environments.
- Quality Components: Invest in high-quality heating elements designed for longevity.
-
Lifespan Expectations
The lifespan of a heating element varies widely depending on usage and conditions. For example:- In household appliances, heating elements may last 5-10 years with moderate use.
- Industrial heating elements, subjected to harsher conditions, may require replacement every 1-3 years.
-
Replacement Considerations
- Cost vs. Benefit: Weigh the cost of replacement against the potential savings from improved efficiency.
- Compatibility: Ensure the replacement element matches the specifications of the original.
- Energy Efficiency: Modern heating elements may offer better energy efficiency, reducing long-term operating costs.
By understanding the causes and signs of degradation, users can take proactive steps to maintain their heating elements and maximize their lifespan. Regular inspection, proper usage, and timely replacement are key to ensuring reliable performance.
Summary Table:
Key Aspect | Details |
---|---|
Mechanisms of Degradation | Oxidation, embrittlement, resistance changes, contamination |
Signs of Degradation | Reduced efficiency, visible damage, inconsistent performance, electrical issues |
Factors Influencing Degradation | Material quality, operating temperature, usage frequency, environmental conditions |
Mitigation Strategies | Proper sizing, regular maintenance, temperature control, protective coatings, quality components |
Lifespan Expectations | Household: 5-10 years; Industrial: 1-3 years |
Replacement Considerations | Cost vs. benefit, compatibility, energy efficiency |
Maximize the lifespan of your heating elements—contact our experts today for tailored solutions!