Induction heating coils do get hot during operation, but their temperature is managed through cooling systems to prevent overheating. The coils generate heat due to the alternating magnetic field they produce, which induces eddy currents in the metal being heated. However, the coils themselves are not the primary source of heat; instead, they transfer energy to the workpiece. To maintain efficiency and prevent damage, cooling systems (typically water-based) are used to regulate the coil's temperature. Overheating can occur due to factors like restricted water flow, debris buildup, or improper furnace design, which can compromise the coil's performance and lifespan.
Key Points Explained:
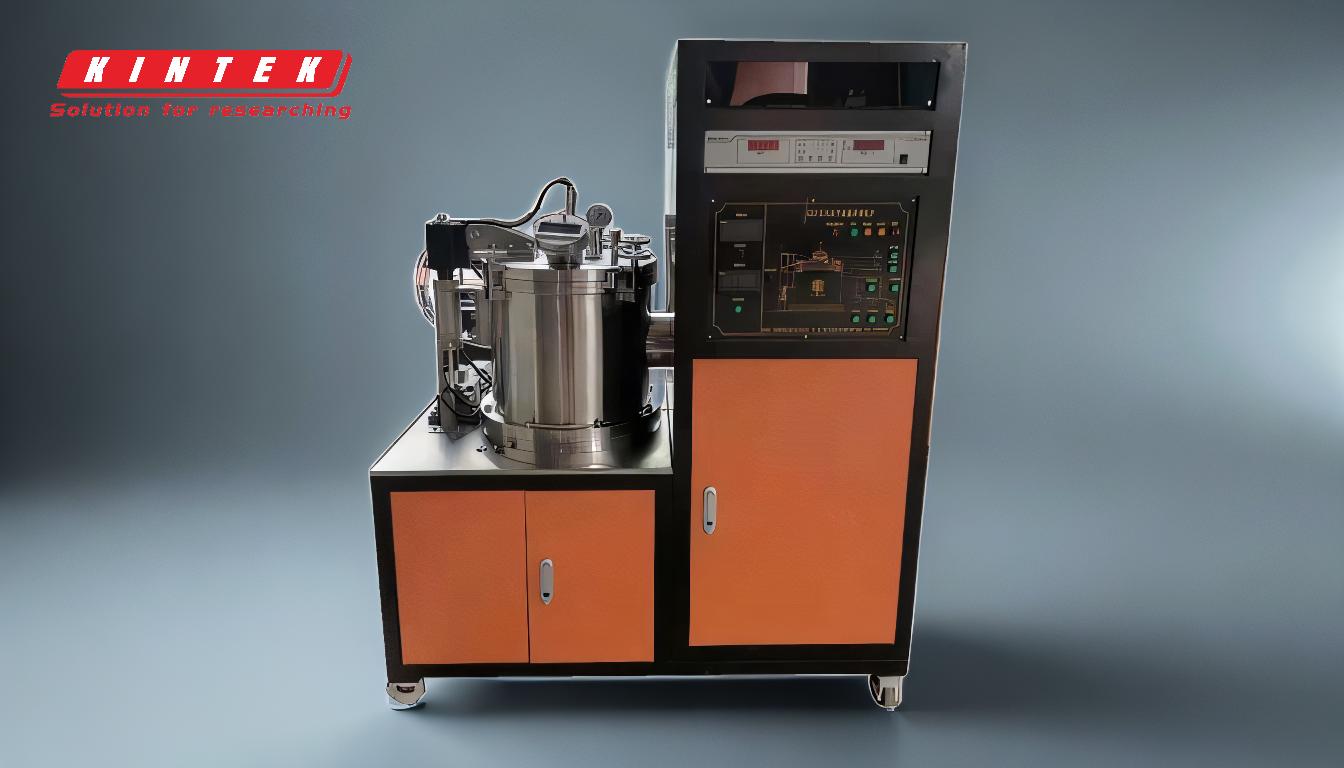
-
Heat Generation in Induction Coils:
- Induction coils generate an alternating magnetic field when connected to an AC power supply. This field induces eddy currents in the metal charge or workpiece, causing it to heat up.
- While the primary heat is generated in the workpiece, the coils themselves also experience some heating due to resistive losses (I²R losses) as current flows through them.
-
Cooling Systems for Induction Coils:
- To prevent overheating, induction coils are equipped with cooling systems, typically using cold water supplied through flexible cables.
- The cooling system ensures that the coils operate within a safe temperature range, maintaining their efficiency and preventing damage.
-
Causes of Coil Overheating:
- Restricted Water Flow: Debris, calcium buildup, or blockages in water lines, heat exchangers, or power cables can restrict cooling water flow, leading to overheating.
- Internal Damage: Damaged water-cooled power cables or improper furnace modifications can disrupt the cooling process.
- Design Issues: Improper furnace lining dimensions or insufficient refractory material can cause heat to concentrate on the coil, leading to overheating.
-
Importance of Simultaneous Operation:
- Both the induction furnace and its cooling system (e.g., air conditioner or water cooling unit) must operate simultaneously to ensure the coils are adequately cooled during operation.
- Failure to maintain this balance can result in coil overheating and potential system failure.
-
Impact of Overheating:
- Overheating can degrade the coil's performance, reduce its lifespan, and even cause permanent damage.
- It can also affect the quality of the heating process, leading to inconsistent results or failure to achieve the desired temperature in the workpiece.
-
Preventive Measures:
- Regular maintenance of the cooling system, including checking for blockages and ensuring proper water flow, is essential.
- Monitoring the furnace design and ensuring proper refractory lining can help prevent overheating.
- Using high-quality materials and avoiding unauthorized modifications to the furnace or cooling system can also mitigate risks.
By understanding these key points, equipment purchasers can make informed decisions about the design, maintenance, and operation of induction heating systems to ensure optimal performance and longevity.
Summary Table:
Key Aspect | Description |
---|---|
Heat Generation | Coils generate heat due to resistive losses (I²R) and transfer energy to the workpiece. |
Cooling Systems | Water-based cooling systems regulate coil temperature to prevent overheating. |
Causes of Overheating | Restricted water flow, internal damage, or improper furnace design. |
Impact of Overheating | Reduced performance, shortened lifespan, and potential system failure. |
Preventive Measures | Regular maintenance, proper furnace design, and high-quality materials. |
Ensure your induction heating system operates efficiently—contact our experts today for tailored solutions!