Induction heating is a process that uses electromagnetic induction to heat electrically conductive materials, such as metals. Copper, being a highly conductive metal, does heat up in induction, but its heating behavior differs from that of ferromagnetic materials like iron or steel. This is because copper's low electrical resistivity and lack of magnetic properties make it less efficient at converting electromagnetic energy into heat compared to ferromagnetic materials. Below, we explore the key factors influencing copper's heating in induction systems.
Key Points Explained:
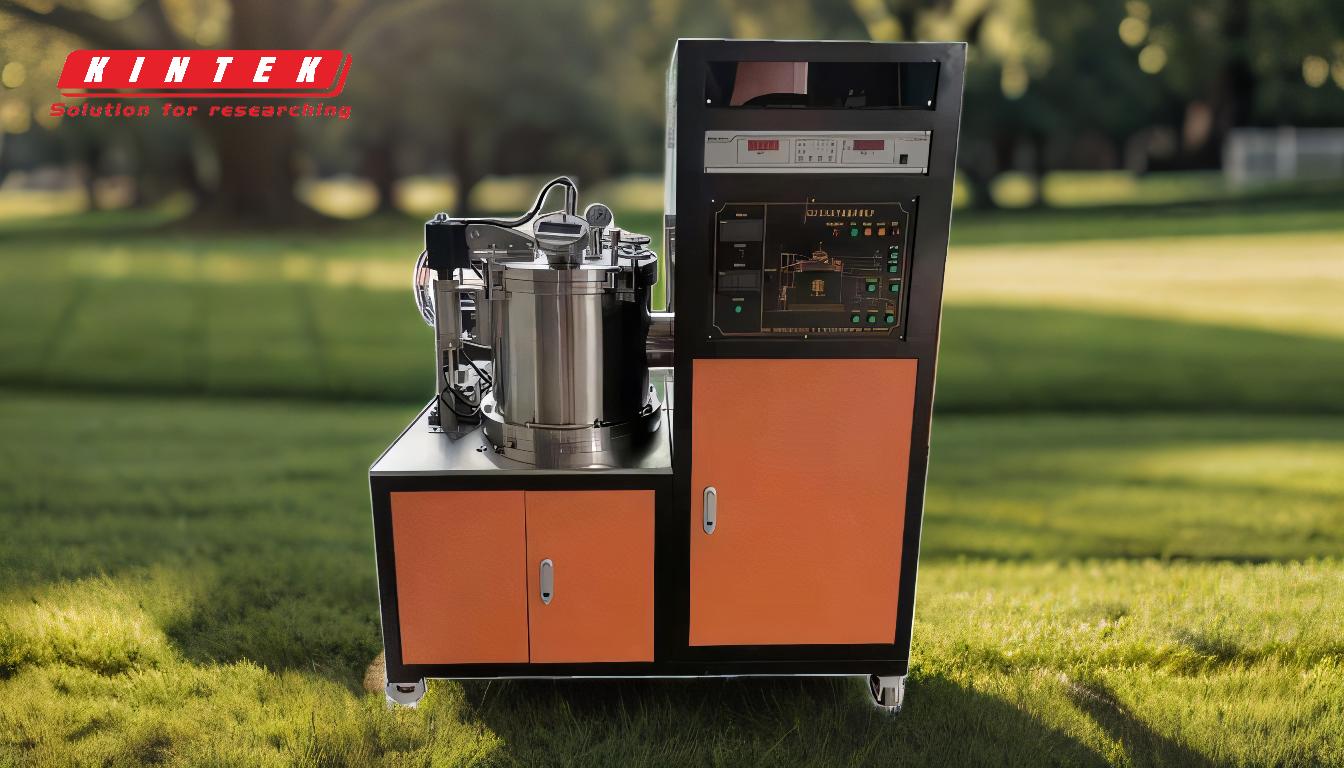
-
How Induction Heating Works:
- Induction heating relies on electromagnetic induction, where an alternating current (AC) passes through a coil, generating a magnetic field.
- When a conductive material (like copper) is placed within this magnetic field, eddy currents are induced within the material.
- These eddy currents generate heat due to the material's electrical resistance (Joule heating).
-
Copper's Electrical and Thermal Properties:
- Copper has very low electrical resistivity, meaning it conducts electricity extremely well.
- Its high thermal conductivity allows it to dissipate heat quickly, which can counteract the heat generated by eddy currents.
- Copper is non-ferromagnetic, so it does not experience hysteresis losses (a significant source of heat in ferromagnetic materials).
-
Why Copper Heats Less Efficiently in Induction:
- The low electrical resistivity of copper results in weaker eddy currents compared to materials with higher resistivity.
- The absence of magnetic hysteresis further reduces the heat generated in copper.
- These factors make copper less efficient at converting electromagnetic energy into heat compared to materials like iron or steel.
-
Factors Affecting Copper Heating in Induction:
- Frequency of the Induction System: Higher frequencies can improve heating efficiency in copper by increasing eddy current density near the surface (skin effect).
- Power Input: Higher power levels can compensate for copper's low heating efficiency.
- Geometry of the Copper Object: Thin or small copper objects heat more effectively than thick or large ones due to better penetration of the magnetic field.
-
Applications of Induction Heating for Copper:
- Induction heating is used for specific copper applications, such as brazing, annealing, or localized heating.
- Specialized high-frequency induction systems are often employed to achieve sufficient heating in copper.
-
Comparison with Ferromagnetic Materials:
- Ferromagnetic materials like iron or steel heat more efficiently in induction due to their higher electrical resistivity and magnetic hysteresis.
- Copper requires more energy and higher frequencies to achieve comparable heating results.
-
Practical Considerations for Heating Copper:
- Induction systems designed for copper often require higher power and frequency settings.
- The process may be less energy-efficient compared to heating ferromagnetic materials.
- Proper coil design and positioning are critical to ensure effective heat transfer to the copper object.
In summary, while copper does heat up in induction, its heating efficiency is lower compared to ferromagnetic materials due to its low electrical resistivity and non-magnetic nature. However, with the right induction system parameters (such as high frequency and power), copper can still be effectively heated for specific industrial applications.
Summary Table:
Aspect | Details |
---|---|
Induction Heating | Uses electromagnetic induction to generate heat in conductive materials. |
Copper's Properties | Low electrical resistivity, high thermal conductivity, non-ferromagnetic. |
Heating Efficiency | Less efficient due to weak eddy currents and no magnetic hysteresis. |
Key Factors | Frequency, power input, and object geometry affect heating efficiency. |
Applications | Used for brazing, annealing, and localized heating in copper. |
Comparison | Ferromagnetic materials like iron heat more efficiently than copper. |
Practical Tips | Higher frequency and power settings are needed for effective heating. |
Need help optimizing induction heating for copper? Contact our experts today for tailored solutions!