Diamond-like carbon (DLC) coatings are highly resistant to rust and corrosion due to their chemical inertness and excellent wear resistance. These coatings are composed of a mix of sp3 (diamond-like) and sp2 (graphite-like) carbon bonds, which contribute to their high hardness, low friction, and resistance to harsh environments. DLC coatings are widely used in applications requiring protection against wear, corrosion, and chemical attack, making them an ideal choice for surfaces exposed to corrosive or abrasive conditions. Their ability to maintain performance in corrosive environments further underscores their rust-resistant properties.
Key Points Explained:
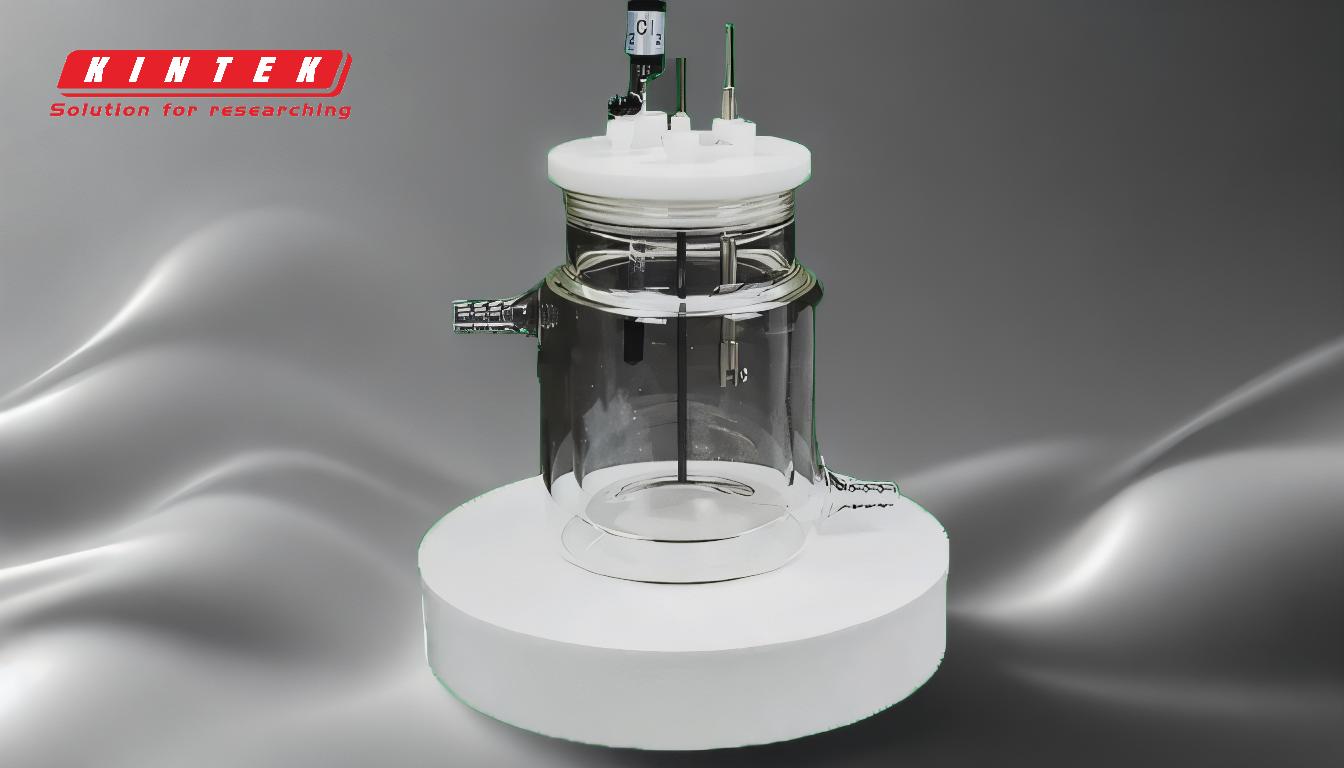
-
Chemical Inertness of DLC Coatings:
- DLC coatings are chemically inert, meaning they do not react easily with other substances, including oxygen and moisture, which are primary contributors to rust formation.
- This inertness is a result of the strong carbon-carbon bonds (sp3 and sp2) that make up the coating, providing a stable and non-reactive surface.
-
Resistance to Corrosive Environments:
- DLC coatings are specifically noted for their high performance in corrosive environments. This makes them highly effective in preventing rust, even when exposed to harsh chemicals or moisture.
- Their resistance to corrosion is further enhanced by their amorphous structure, which lacks grain boundaries that could otherwise serve as initiation points for corrosion.
-
Wear and Chemical Resistance:
- The wear resistance of DLC coatings ensures that the protective layer remains intact over time, even under abrasive conditions. This durability prevents the underlying material from being exposed to corrosive elements.
- Additionally, their chemical resistance ensures that the coating does not degrade when exposed to acids, alkalis, or other reactive substances, further preventing rust formation.
-
Applications in Corrosive and Abrasive Environments:
- DLC coatings are commonly used in industries where components are exposed to corrosive or abrasive conditions, such as automotive, aerospace, and medical devices.
- Their ability to protect surfaces in these demanding environments highlights their effectiveness in preventing rust and corrosion.
-
Comparison to Other Coatings:
- Unlike some metallic coatings that may corrode over time, DLC coatings maintain their integrity due to their carbon-based composition.
- This makes them superior to many traditional coatings in terms of rust prevention, especially in applications where long-term durability is critical.
-
Deposition Techniques and Coating Quality:
- The quality of DLC coatings, including their rust resistance, can be tailored by controlling deposition parameters such as gas phase composition and deposition techniques (e.g., PACVD).
- These techniques ensure that the coatings have low surface roughness, high hardness, and excellent adhesion, all of which contribute to their rust-resistant properties.
In summary, DLC coatings do not rust due to their chemical inertness, resistance to corrosive environments, and excellent wear and chemical resistance. These properties make them an ideal choice for applications requiring long-term protection against rust and corrosion.
Summary Table:
Property | Description |
---|---|
Chemical Inertness | Resists reactions with oxygen and moisture, preventing rust formation. |
Corrosion Resistance | Performs well in harsh, corrosive environments, even with exposure to chemicals. |
Wear Resistance | Maintains integrity under abrasive conditions, protecting underlying materials. |
Applications | Used in automotive, aerospace, and medical industries for long-term protection. |
Comparison to Other Coatings | Superior to metallic coatings in rust prevention and durability. |
Deposition Techniques | Tailored for low roughness, high hardness, and excellent adhesion. |
Interested in DLC coatings for rust prevention? Contact our experts today to learn more!