Induction heating does work on graphite, as graphite is a conductive material capable of being heated through induced eddy currents. This process is widely utilized in industries such as semiconductor manufacturing, where graphite crucibles are heated to process materials like silicon. Induction heating is effective for graphite due to its electrical conductivity, allowing it to generate heat when exposed to an alternating magnetic field. This method is advantageous for its precision, speed, and efficiency, making it suitable for applications ranging from melting and alloying to surface hardening and heat treatment.
Key Points Explained:
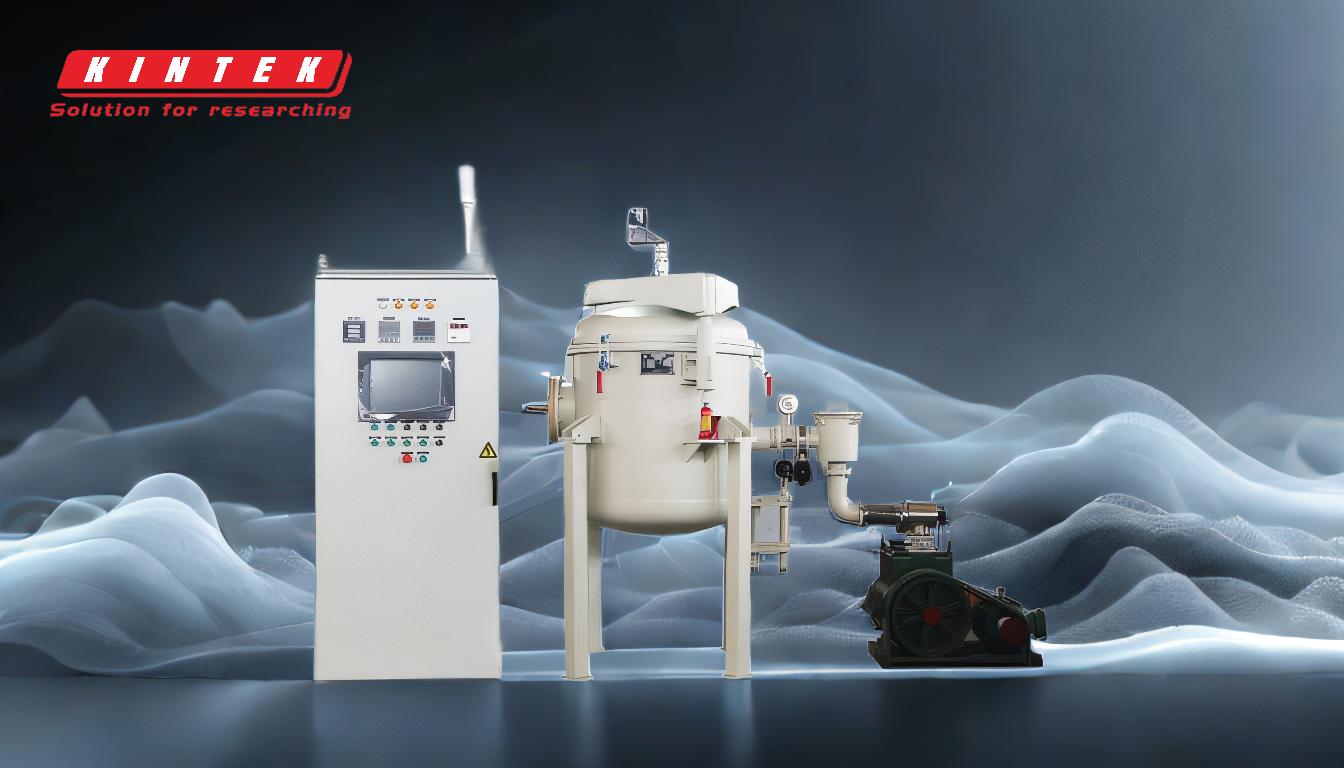
-
Graphite as a Conductive Material:
- Graphite is a form of carbon with high electrical conductivity, making it suitable for induction heating. When exposed to an alternating magnetic field, eddy currents are induced within the graphite, generating heat due to its resistivity.
- This property is why graphite crucibles are commonly used in induction heating processes, particularly in industries like semiconductor manufacturing.
-
Applications of Induction Heating on Graphite:
- Semiconductor Industry: Graphite crucibles are heated to process materials such as silicon, which is critical for semiconductor production. The precise control of induction heating ensures consistent results in these high-tech applications.
- Melting and Alloying: Induction heating can reach temperatures high enough to melt graphite or materials contained within graphite crucibles, enabling the creation of alloys and specialized materials.
- Heat Treatment: Induction heating is used for targeted heating, such as surface hardening or annealing, where graphite components or tools may require controlled thermal processing.
-
Advantages of Induction Heating for Graphite:
- Precision and Control: Induction heating allows for localized and precise heating, which is essential for applications like semiconductor processing or heat treatment.
- Energy Efficiency: The process is highly efficient, as heat is generated directly within the material, reducing energy waste.
- Speed: Induction heating provides rapid heating, which is beneficial for industrial processes requiring quick turnaround times.
-
Technical Considerations:
- Resistivity of Graphite: While graphite is conductive, its resistivity is higher than that of metals. This means that induction heating systems must be optimized to account for the specific electrical properties of graphite.
- Temperature Range: Induction heating can achieve the high temperatures required for melting or processing graphite, but the equipment must be designed to handle these extreme conditions.
-
Future Trends and Research:
- As technology advances, induction heating is expected to expand into new applications, including the processing of low-resistivity materials and specialized alloys. Research is ongoing to optimize process parameters for emerging uses, including those involving graphite.
-
Comparison with Other Heating Methods:
- Induction heating offers distinct advantages over traditional methods like resistance heating or flame heating. It provides faster heating rates, better control, and reduced contamination risks, which are critical in high-purity applications involving graphite.
In summary, induction heating is a highly effective method for heating graphite, leveraging its conductive properties to achieve precise and efficient thermal processing. Its applications span industries such as semiconductors, metallurgy, and materials science, with ongoing advancements promising even broader use in the future.
Summary Table:
Key Aspect | Details |
---|---|
Graphite Conductivity | High electrical conductivity enables efficient induction heating. |
Applications | Semiconductor manufacturing, melting, alloying, and heat treatment. |
Advantages | Precision, energy efficiency, and rapid heating. |
Technical Considerations | Higher resistivity than metals; requires optimized systems for high temps. |
Future Trends | Expanding into low-resistivity materials and specialized alloys. |
Ready to optimize your thermal processes with induction heating? Contact our experts today to learn more!